Thermal Coating Department
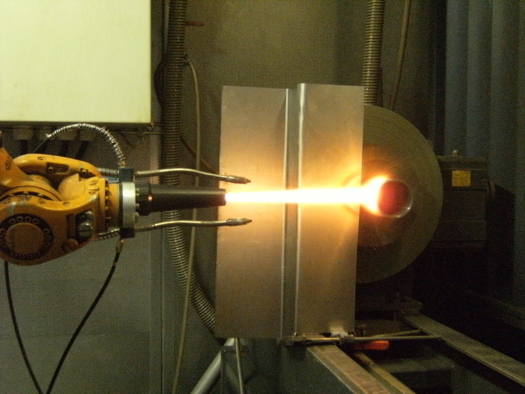
Welcome to the Thermal Coating Department.
Our department focuses on the holistic development of coating solutions using various thermal coating processes. In addition to the functionalisation of surfaces, our research work focuses on process analysis and the development of application-specific alloys and powder materials.
Our portfolio includes powder and wire flame spraying, arc spraying, high velocity oxy-fuel spraying (HVOF), atmospheric plasma spraying (APS) and cold gas spraying (CGS) - all important thermal spraying processes. A laser cladding system extends our range to include edge coating processes. We also have a state-of-the-art laboratory facility for the production of metallic and intermediate powders using ultrasonic atomisation, which allows alloys to be produced in small but systematically variable powder batches. In addition, high-energy ball milling is a flexible process that allows us to produce mechanically alloyed powders and optimise their alloying properties. Various processes are available to us for substrate preparation, with surface structuring also being a subject of research. In addition to our many years of experience in the field of thermal spraying, we can draw on extensive equipment for the detailed characterisation of the property profiles of thermally sprayed coatings. This includes extensive microstructure analysis using SEM, EDX, XRD, GDOES and numerous test rigs for wear and corrosion testing and adhesive tensile testing.
On the materials side, our research includes the application of metallic, ceramic and composite powders on a wide variety of substrate materials (metals, ceramics, polymers, glasses, organic natural materials such as wood, composites, etc.).
Under the tabs at the top of this screen you will find more detailed information on our research activities, the services we offer and the extensive range of equipment and methods available in our department.
Do you have any further questions or can we support you in your tasks? Then simply contact us at the telephone number or e-mail address below.
We look forward to working with you!
The research activities of the Thermal Coating department cover a broad spectrum of current issues and include both basic research and highly application-orientated research with industrial partners. Our excellent national and international network and many years of experience in the field of thermal coating form the basis for the successful processing of innovative projects.
Our research also pursues a holistic approach in which we consider the most important aspects of thermal spraying based on the alloy development of the powder materials, detailed process analysis and the detailed characterisation of the coating with regard to microstructure and property profile.
Below you will find our current and recently completed research projects.
We will be happy to advise or support you with our expertise in solving your tasks.
Just get in touch with us!
Funding organisations:
Project partner:
BorTec SMT GmbH & Co. KG
Running time:
Brief description
The market relevance of additive manufacturing processes is increasing as a result of their versatile production technology options in terms of design freedom. However, additively manufactured components often have a comparatively high roughness due to the process, which means that the full potential of additive manufacturing processes cannot usually be utilised, as the post-processing of integrated cooling channels, small holes, etc. to reduce the roughness is associated with a high level of effort. The aim of the research project is to develop a process chain for the surface conditioning of additively manufactured (SLM) components made of 17-4 PH using plasma polishing and low-temperature surface hardening. The central research questions are the possibilities and limitations of plasma polishing to reduce roughness in hard-to-reach areas (e.g. lateral surface of small bores) and the effect of the process-related microstructure and plasma polishing on subsequent low-temperature surface hardening. The aim of surface hardening is to increase wear resistance through the interstitial incorporation of carbon and nitrogen in the edge area without impairing corrosion resistance. The project is also looking at the influence of the powder fraction used on the microstructure and property profile of SLM-manufactured components.
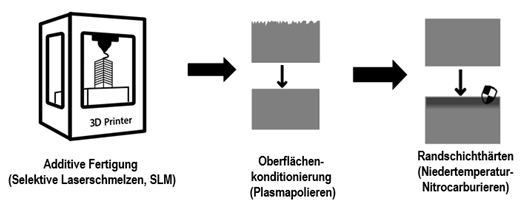
Funding organisations:
Project partner:
Running time:
Brief description
Tungsten carbide-cobalt (WC-Co) carbide coatings have dominated for many years as wear protection coatings in numerous areas of application. The extremely high performance of the coatings is based on the almost perfect interaction between hard tungsten carbide and ductile cobalt matrix. In recent years, however, efforts to replace this dominant coating system have intensified, as the future use of cobalt could be restricted due to its carcinogenic effect (REACH regulation) and tungsten could be restricted by the EU's classification as a "critical raw material" (CRM). The development of alternative coating systems is necessary to improve competitiveness. The performance of niobium carbide-based, cobalt-free hard metal coatings is therefore being investigated as part of the research project. Niobium carbide has a number of promising properties. These include high hardness, good oxidation resistance and improved interactions with cobalt-free binders (e.g. Fe-based) compared to WC. Within the project, several experimental powder materials are produced by agglomeration and sintering and processed by high-speed flame spraying and laser cladding. By adapting the powder material and the processing methods, the aim is to apply high-quality NbC-based hard metal coatings whose property profile is then characterised in detail and compared with industrially used reference systems (WC-Co, Cr3C2-NiCr, (Ti,Mo)(C,N)).
Funding organisations:
Project partner:
Running time:
Brief description
Self-flowing alloys are a proven coating material for applications with complex stress profiles. A media-tight and firmly adhering layer is formed by remelting the thermal spray coating. Remelted nickel-based alloys are established metallic sealing systems in the field of valve construction. Reducing friction losses in sealing systems significantly increases cost and energy efficiency. Currently, additional friction-reducing diamond-like carbon layers (DLC) are applied to the remelted metallic surface. Solid lubricants incorporated into the coating represent a promising alternative to the coating composite described above. The aim of current R&D activities is the development of a self-flowing alloy with structurally integrated solid lubricants and their processing in the thermal spraying process.
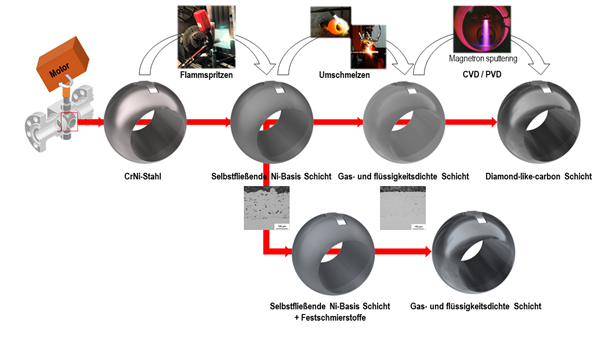
Funding organisations:
Project partner:
Amazemet Sp.z o.o (Poland)
HS Technik Beschichtungstechnologien GesmbH (Austria)
Iskenderun Technical University (Turkey)
Running time:
Brief description
Innovative material and production concepts can be used to fulfil the often contradictory requirements for processing and functional properties. Austenitic high-manganese steels (HMnS) offer great, previously untapped application potential in the field of surface technology. They are characterised in particular by high work hardening under impact and shock loads, which enables applications with superimposed tribological stresses. The production of the powdery base materials by gas atomisation and their processing with modern coating technologies such as HVOF and HS-LMD guarantee a high material quality of the coating system. Mechanical post-processing makes it possible to adjust the property profile with regard to the tribological stress profile. A process combination between thermal coating technologies and the refinement of HMnS coating systems thus enables surface functionalisation with gradation of the coating properties through work hardening. IronWorkCoat is aimed at sustainable coating solutions for applications with superimposed tribological stresses.
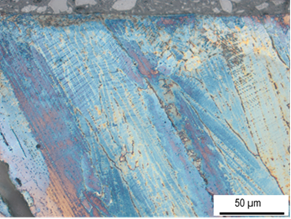
Cross-section of a diamond-smoothed and Beraha II-etched X120Mn12 LMD layer
Project partner:
Running time:
Brief description
Metal-thermoplastic composites have great potential for lightweight construction applications due to their high specific strength and damage tolerance. Thermal joining is an established production technology. The interlaminar strength of the composite is essentially set by mechanical clamping, as the materials have a materially divergent property profile. The aim of the project is to investigate the relationship between the surface fineness of the metallic joining partner and the interlaminar strength in the bond with the polymer partner. The structured surfaces are characterised by approximating fractal geometry by determining the fractal dimension. This scale-independent mathematical value is to be correlated with the interlaminar strength of aluminium EN AW6082 joined with polyamide 6 (glass fibre reinforcement 30 %). Based on this, an ultrasound-assisted, machining micromachining technology is to be developed together with the project partner, the Chair of Microfabrication Technology, with which the metallic components are to be structured and the interlaminar strength in the composite is to be adjusted in a defined manner.
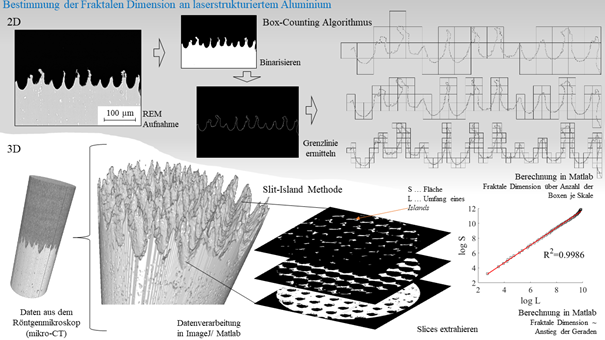
Funding organisations:
Project partner:
Running time:
Brief description
The aim of the project is to research the material- and technology-related influencing variables on the complex reaction processes in multi-component coating materials in the model system Al2O3-Cr2O3-TiO2 in order to specifically produce single-phase coatings with a homogeneous microstructure for highly stressable components (e.g. electrical insulation coatings in ball bearings or heating coating systems with simultaneous superimposed tribological and/or corrosive stress). To this end, both the formation and stability of novel, ternary phases (solid solutions such as α-(Al,Cr,Ti)2O3) under the conditions of spray processing and their property profile are being investigated in detail. With the help of experimental powder materials that differ in terms of their phase composition (powder mixtures, specially developed single-phase and multi-phase a&s powder materials) and the variation of important influencing variables of the injection moulding process (focus on APS), well-founded knowledge about the reaction site and the mechanisms of such multi-component powder materials is gained. In addition, post-treatment routines (heat treatment, laser remelting) are developed in order to subsequently homogenise multiphase layers, such as those to be expected when processing coarse powder mixtures (cost-effective, high flexibility). Ternary phases from the model system under consideration have a high potential to exceed the performance of known coating solutions.
Funding organisations:
Project partner:
Fraunhofer Institute for Machine Tools and Forming Technology (IWU)
Running time:
Brief description
The project aims to develop a process chain suitable for series production for the manufacture of coated C/C materials. The basis for this is the pultrusion manufacturing process, which is intended to provide cost-effective green bodies for subsequent pyrolysis to produce C/C materials. In addition to the qualification of PF resins for pultrusion, the project focuses primarily on the targeted production of graded multiaxially reinforced profile structures with a high-silicon surface and low-silicon core. This innovative approach is intended to positively influence the pore size and number on the C/C surface during pyrolysis by forming silicon carbide (SiC) in order to apply a well-adhering, ceramic protective layer in the final step by means of thermal spraying. The project thus addresses numerous current obstacles that prevent a broader application of C/C materials, with the research work at the WOT focussing on the application and the property profile of the thermally sprayed layer. This is illustrated by the example of C/C charging racks, which are already being used for heat treatment. The innovative manufacturing process of pultrusion eliminates the need for cutting from plate-shaped semi-finished products. In addition to aspects of resource efficiency, this avoids damage to load-bearing fibres as a result of separating manufacturing processes. The thermally sprayed layer protects the C/C materials from a range of environmental influences. As a mechanical barrier, the absorption of foreign substances (e.g. oils) into the often open pore structure of C/C materials is reduced. Furthermore, the thermally sprayed layer serves as a diffusion barrier for carbon, reduces susceptibility to oxidation at high temperatures and protects the substrate from abrasive wear.

Funding organisations:
Project partner:
Palacky University Olomouc (Czech Republic)
DRUGON International SRL (Romania)
Running time:
Brief description
Increasing the service life of functional surfaces forms the basis for the responsible use of available natural resources. This applies in particular to protective coatings used in machining and cutting applications. The aim of the project is to develop new types of super-hard protective coatings for wood cutting and machining tools. In order to prevent brittle failure of the thin layers when subjected to punctual forces, various surface functionalisation options are being researched. In addition to thermochemical processes for surface hardening, mechanical processes for work hardening are also being considered. The combination of both surface technologies allows the development of hierarchical nano-/micro-coatings. The use of the new generation of cutting tools is aimed at reducing energy consumption and operating costs and extending the application limits.
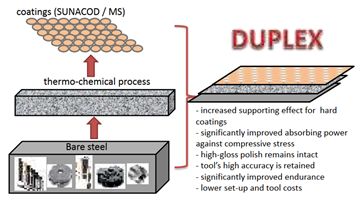
Current publications
-
Saborowski, E.; Steinert, P.; Lindner, T.; Schubert, A.; Lampke, T.
Pin-Shaped Surface Structures Generated by Laser Single Pulse Drilling for High-Strength Interfaces in Thermally Joined Polymer-Metal Hybrids
( https://doi.org/10.3390/ma16020687 ) -
Lindner, T.; Preuß, B.; Löbel, M.; Rymer, L.-M.; Grimm, M.; Schwarz, H.; Seyller, T.; Lampke, T.
Non-Metallic Alloying Constituents to Develop a Wear-Resistant CrFeNi-BSiC High-Entropy Alloy for Surface Protective Coatings by Thermal Spraying and High-Speed Laser Metal Deposition
( https://doi.org/10.3390/coatings13020291 ) -
Rymer, L.-M.; Lindner, T.; Lampke, T.
Nb and Mo Influencing the High-Temperature Wear Behaviour of HVOF-Sprayed High-Entropy Alloy Coatings
( https://doi.org/10.3390/coatings13010009 ) -
Maximilian Grimm, Susan Conze, Lutz-Michael Berger, Sven Thiele, Thomas Lindner, Thomas Lampke
Microstructures and property profiles of atmospheric plasma sprayed (Al,Cr,Ti) 2 O 3 solid solution coatings
( https://doi.org/10.1016/j.surfcoat.2023.129309 ) -
Aleksandra Małachowska, Ondrej Kovarik, Adam Sajbura, Pawel Sokolowski, Thomas Lindner, Mario Scholze, Miroslav Karlík, Jaroslav Čech, Thomas Lampke
Mechanical and fatigue properties of plasma sprayed (Fe 0.9 Co 0.1 ) 76 Mo 4 (P 0.45 C 0.2 B 0.2 Si 0.15 ) 20 and Fe 56.04 Co 13.45 Nb 5.5 B 25 metallic glasses
( https://doi.org/10.1016/j.surfcoat.2023.129361 ) -
Delgado Arroyo, D.; Richter, T.; Schroepfer, D.; Boerner, A.; Rhode, M.; Lindner, T.; Preuß, B.; Lampke, T.
Influence of Milling Conditions on Al x CoCrFeNiMo y Multi-Principal-Element Alloys
( https://doi.org/10.3390/coatings13030662 ) -
Preuß, B.; Lindner, T.; Uhlig, T.; Tapia Cabrera, J.E.; Schwarz, H.; Wagner, G.; Seyller, T.; Lampke, T.
Microstructure Evolution and Wear Resistance of the Eutectic High-Entropy Alloy Al 0.3 CoCrFeNiNb 0.5 Produced by Laser Metal Deposition
( https://doi.org/10.3390/coatings13030585 ) -
Rymer, L.-M.; Lindner, T.; Lampke, T.
Enhanced high-temperature wear behaviour of high-speed laser metal deposited Al 0.3 CrFeCoNi coatings alloyed with Nb and Mo
( https://doi.org/10.1016/j.surfcoat.2023.129832 ) -
Grimm, M.; Kutschmann, P.; Pluta, C.; Schwabe, O.; Lindner, T.; Lampke, T.
Quasi Non-Destructive Quality Assessment of Thermally Sprayed AISI 316L Coatings Using Polarisation Measurements in 3.5% NaCl Gel Electrolyte
( https://doi.org/10.3390/coatings13071256 ) -
Preuß, B., Lindner, T., Uhlig, T., Wagner, G., Lampke, T.
Niobium and molybdenum as alloying constituents in Al 0.3 CoCrFeNi to develop eutectic high-entropy alloys for HVOF spraying
( https://doi.org/10.1007/s11666-022-01417-w ) -
Development of CoCr
0.65
FeNi-BSiC as a self-fluxing high-entropy alloy for thermal spraying
( https://doi.org/10.1016/j.surfcoat.2023.130259 ) -
Forming Behaviour of Additively Manufactured Al/Ti Material Compounds Produced by Cold Spraying
( https://doi.org/10.1007/s11666-023-01699-8 )
Recently completed projects (since 2018)
AiF IGF | Overlay welding and mechanical post-processing of complex alloy systems as new coating materials for tribologically highly stressed components |
AiF IGF | Numerically based design and construction for thermally coated, residual stress-sensitive component structures on a polymer basis |
AiF IGF | Optimisation of the carbide grain size in WC-Co(Cr) coatings to increase wear resistance with simultaneous corrosive stresses |
AiF ZIM | Overlay welding and mechanical post-processing of complex alloy systems as new coating materials for tribologically highly stressed components |
AiF ZIM | Technology and tool development for combined forming and cutting |
AiF ZIM | Spot welding of metal-plastic composites by inductive heating of thermally sprayed layers; spot welding of metal-plastic composites |
AiF ZIM | Process development for surface layer hardening of thermally sprayed Inconel 718 coating systems by boriding |
AiF ZIM | Development of a gel electrolyte-based rapid corrosion test for thermally sprayed material systems with mobile application options that meets requirements |
AiF ZIM | Process development for bond coat-free nitriding of iron-based wear protection coatings for temperature-stressed components |
SAB | Ternary oxide ceramic functional materials and layers |
SAB | Low-temperature brazing of laser-structured and metal-coated fibre-plastic composites |
SAB | High entropy alloys as coating materials for surface protection applications |
DFG | Coating materials made from high-entropy alloys for tribologically highly stressed surfaces |
DFG | Production and forming of generatively manufactured Al-Ti material composites |
Cornet | Powder production of iron-based high-performance materials for generative manufacturing processes |
In addition to the application of thermally sprayed coatings, the range of services offered by the Thermal Coating department also includes their extensive characterisation in terms of microstructure (e.g. XRD, SEM, EDX) and property profile (adhesion, wear and corrosion resistance). The diagnostics of thermal spray processes and the production of powder materials, whether by mechanical alloying using high-energy ball milling or ultrasonic atomisation, are also part of our portfolio.
You will find the technical equipment available to us for this purpose organised by laboratory area under the corresponding tab on this page.
We offer the following services as standard.
Contact us if you would like us to support you in special tasks!
-
Conventional systems (in coop. with IFS) Combi spraying system
- Powder Flame Spraying (PFS)
- Wire flame spraying
- Arc spraying (AS)
- High velocity powder flame spraying (HVOF)
- High velocity wire flame spraying (HVCW)
- Atmospheric Plasma Spraying (APS)
- Cold Gas Spraying (CGS)
- Motion Pro Y4 high-speed camera
- Particle diagnostics Oseir SprayWatch / GTV NIR sensor
- Thermographic camera Optris Xi 80
- High Energy Ball Mill Zoz Simoloyer CM08-8l
- High energy ball mill Zoz Simoloyer CM01-2l / SiN
- Planetary ball mill Fritsch Pulverisette 5
- Ultrasonic atomisation system
- Vacuum arc furnace (utilisation via the PVW professorship)
-
X-ray fine structure analysis using XRD:
- qualitative and quantitative phase analysis and determination of the lattice parameters
- Determination of particle sizes and micro distortions
- Residual stress measurement
- Texture analysis
- Coating thickness, roughness and density determination by means of reflectometry
- Simultaneous performance of thermogravimetry (TG) and optionally differential thermal analysis (DTA) or dynamic differential calorimetry (DSC)
- Thermomechanical analysis (TMA) to determine the behaviour of materials under mechanical and thermal loading
- Mechanical testing of coatings (face tensile test/adhesive tensile test, tensile test, bending test)
- Fatigue testing of coated materials in the LCF range with servo-hydraulic testing machine (cyclic tensile testing in the tensile threshold range and cyclic bending testing with all load conditions).
- Various standardised wear tests in solid contact (Taber Abraser, Rubber Wheel, Miller test, vibration friction wear test (Ball-on-Disk, Pin-on-Disk etc.)).
- Fatigue testing in the LCF and HCF range under tensile, compressive and bending loads
- Powder flame spraying
- Wire flame spraying
- High velocity oxygen fuel spraying
- High velocity wire flame spraying
- Atmospheric Plasma Spraying (APS)
- Cold Gas Spraying (CGS)
- High Energy Ball Mill Zoz Simoloyer CM08-8l
- High energy ball mill Zoz Simoloyer CM01-2l / SiN
- Planetary ball mill Fritsch Pulverisette 5
- High Energy Ball Mill Zoz Simoloyer CM08-8l
- High energy ball mill Zoz Simoloyer CM01-2l / SiN
- Planetary ball mill Fritsch Pulverisette 5
- Powder atomisation system
- AMC casting device
- Electric arc furnace (use via Professorship PVW)
- Spark plasma sintering system (SPS) (use via Professorship PVW)
- Various muffle and protective gas furnaces as well as quenching baths
- Materialographic preparation technique
- Electron microscopic preparation technique
- Light microscopic examination technique
- Quantitative microstructure analysis OLYMPUS a4i
- Micro hardness tester DURAMIN
- Recording hardness measurement FISCHERSCOPE HM2000 XYm
- Scanning electron microscope LEO1455VP with X-ray micro-range analysis EDAX GENESIS
- Field emission scanning electron microscope NEON40EsB with EDXS and EBSD
- Transmission electron microscope HITACHI H8100 with X-ray microrange analysis EDAX GENESIS
- Nanoindenter UNAT
- Resonance pulsator RUMUL - Wöhler tests
- Resonance pulsator RUMUL - crack propagation tests
- MTS Landmark (100kN) equipment - strain-controlled fatigue tests
- MatLab
- Mathcad
- Deform
- Fluent
- JMatPro
- ABAQUS
- ANSYS
- MemBrain
- Model tests in the laboratory
- Boil test (intergranular and stress corrosion cracking test)
- Corrosion test chamber HK 400
- Potentiostat PS6 (determination of current density potential curves)
- Electrochemical MiniCell (ECMC)
- Pitting and crevice corrosion test, ASTM G48
- Climate test chamber
- Microcorrosion cell
- Corrosion test chamber HK 430
- 3-D profilometer
- pH-value measuring device
- X-ray fluorescence material analyser
- Colour and Gloss Meter BYK Gardener spectro-guide
Contact
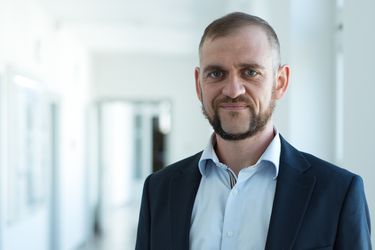
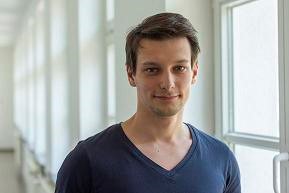