Abteilung Chemische und galvanische Oberflächentechnik
Willkommen im Bereich der Abteilung Chemische und galvanische Oberflächentechnik.
Unsere Abteilung erforscht primär Oberflächenbehandlungen und Beschichtungen mittels nasschemischer Verfahren. Dazu zählen u.a. die chemische und elektrochemische Metallabscheidung, anodische, plasmachemische und chemische Konversionsschichten.
Die Abteilung beinhaltet die Arbeitsgruppen Kathodische Prozesse und Anodische Oberflächentechnik und umfasst 7 wissenschaftliche und 5 technische Mitarbeiter (Stand 12/17).
Im Folgenden finden Sie eine Auswahl unserer wichtigsten Forschungsthemen.
Gern beraten oder unterstützen wir Sie mit unserer Expertise bei der Lösung Ihrer Aufgaben.
Sprechen Sie uns einfach an!

Einfluss organischer Additive auf das Entladungsverhalten während der plasmaanodischen Oxidation einer Magnesiumlegierung

Die Mikrostruktur (Korngröße, Eigenspannungen, Textur) von elektrochemischen Nickelschichten sind durch Additive (Glanzbildner, Härtezusätzen, Entspannern) variabel einstellbar (Bild oben: lamellarer Aufbau; Bild unten: kolumnarer Aufbau). Dadurch können die mechanischen Eigenschaften gezielt eingestellt werden (Bild rechts).

Adsorption eines Glanzbildners auf einer Nickeloberfläche. Deutlich zu erkennen ist Änderung der Doppelschichtkapazität bei höheren Konzentrationen. Durch dieses Verfahren kann der Arbeitsbereich und die Wirkungsweise von Glanzbildnern effektiv bestimmt werden.
Härtekatalog
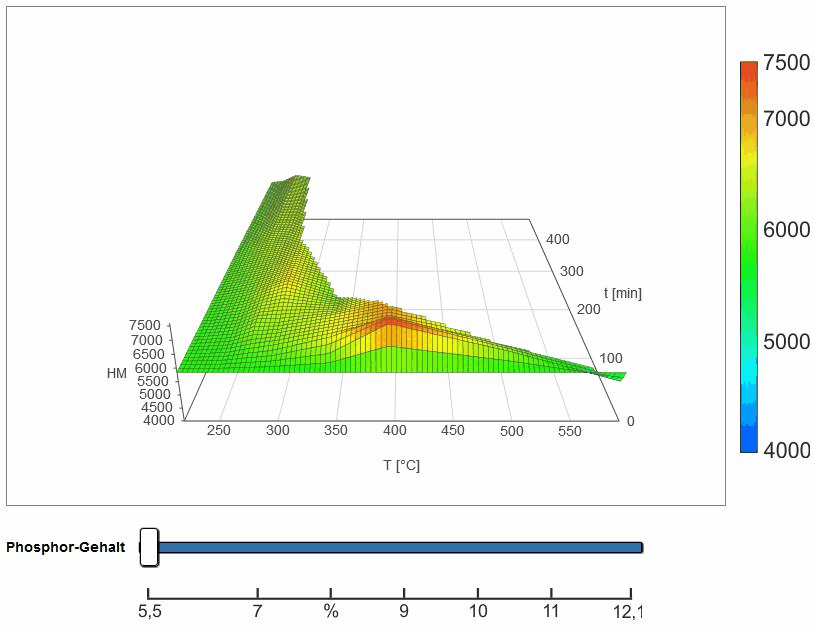
Im IGF-Vorhaben (AiF-Nr.: 16736BR/1) wurde die Gefüge- und Eigenschaftsentwicklung chemisch abgeschiedener und wärmebehandelter NiP-Schichten auf Basis blei- und cadmiumfreier Elektrolytsysteme untersucht. Ausgehend von repräsentativen, industriell angewendeten Elektrolyten wurden low-, mid- und highphos-Schichten untersucht.
Interaktiver Verschleißkatalog
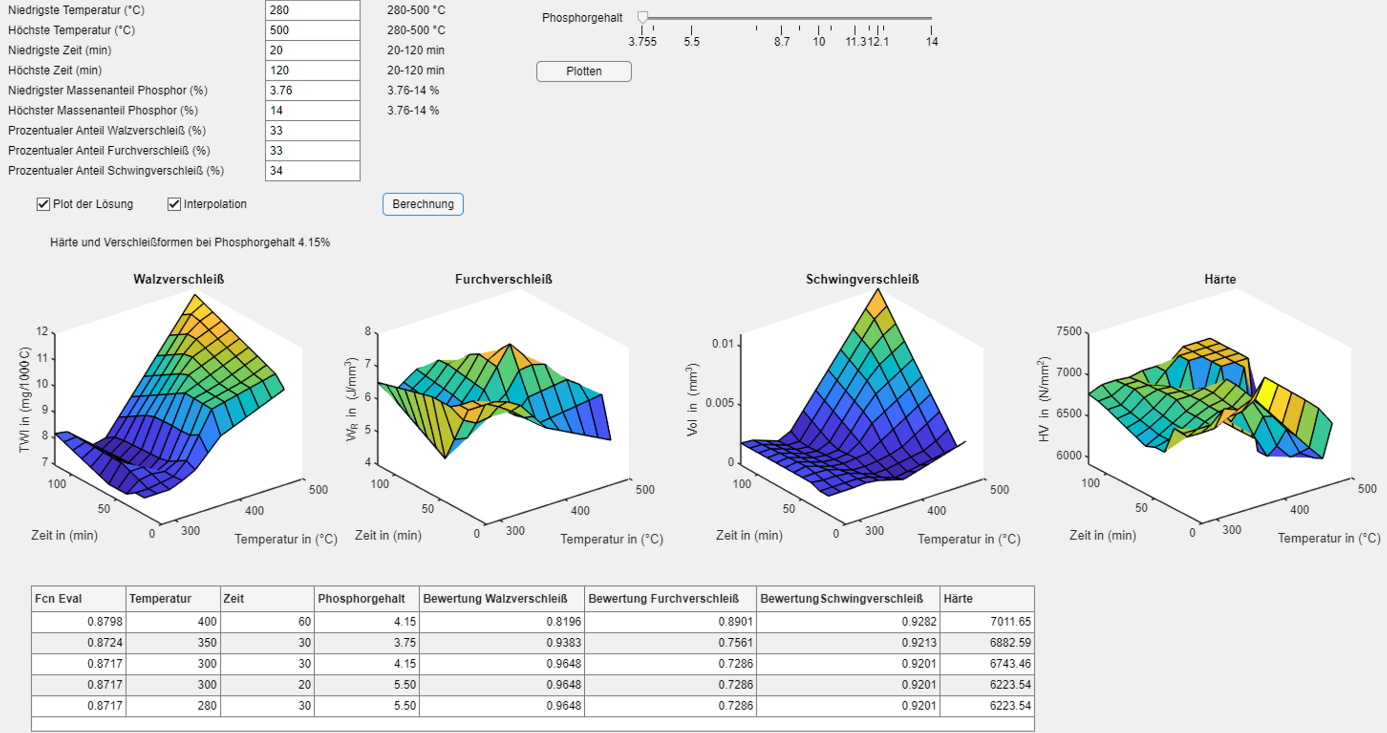
Im IGF-Vorhaben (AiF-Nr.: 20747 BR/1) wurden verschiedene Verschleißtests mit industriell hergestellten low-, mid- und highphos-Schichten durchgeführt. Aus den jeweiligen testabhängigen Kennwerten wurde ein interaktiver Verschleißkatalog erstellt. Da reale Verschleißbeanspruchungen sich aus Anteilen verschiedener Verschleißarten zusammensetzen, kann der Nutzer des Verschleißmodells die für seine Anwendung individuell relevanten Verschleißarten prozentual wichten und erhält dazu die optimierten Wärmebehandlungsparameter sowie den Phosphorgehalt.
Unsere technische Ausrüstung finden Sie nach Laborbereichen geordnet unter dem entsprechenden Reiter auf dieser Seite.
Standardmäßig bieten wir die folgenden Dienstleistungen an.
Sprechen Sie uns an, wenn wir Sie in speziellen Aufgaben unterstützen sollen!
- Korrosionsuntersuchungen
- Ermüdungsprüfung im LCF- und HCF-Bereich unter Zug-, Druck- und Biegebelastung
- Beschichten
- galvanische Schichten
- chemische Schichten
- elektrolytisch oxidierte Schichten
- Robotergestützte Galvanikanlage
- Galvanisieranlage ERO
- Anlage zur plasmaelektrolytischen Oxidation PEO
- Anodisieranlage MANZ
- Versuchsstand Phosphatieren
- Stromquellen
- Transientenrekorder Yokogawa DL850
- Ermittlung der el. Leitfähigkeit von Nichteisenmetallen
- pH-Wert-Messgerät
- Schichtdickenmessgerät
- Schichtdickenprüfgerät nach dem Kalottenschleifverfahren (z.B. DIN EN 1071-2)
- Röntgenfluoreszenz-Materialanalysegerät
- Farb- und Glanzmessgerät BYK Gardener spectro-guide
- Glanz- und Schichtdickenmessgerät BYK Gardener micro-TRI-gloss µ
- Hochenergiekugelmühle Zoz Simoloyer CM08-8l
- Hochenergiekugelmühle Zoz Simoloyer CM01-2l / SiN
- Planetenkugelmühle Fritsch Pulverisette 5
- Pulververdüsungsanlage
- AMC-Gießeinrichtung
- Lichtbogenofen (Nutzung über Professur PVW)
- Spark-Plasma-Sinteranlage (SPS) (Nutzung über Professur PVW)
- verschiedene Muffel- und Schutzgasöfen sowie Abschreckbäder
- Materialografische Präparationstechnik
- Elektronenmikroskopische Präparationstechnik
- Lichtmikroskopische Untersuchungstechnik
- Quantitative Gefügeanalyse OLYMPUS a4i
- Mikrohärte-Prüfgerät DURAMIN
- Registrierende Härtemessung FISCHERSCOPE HM2000 XYm
- Rasterelektronenmikroskop LEO1455VP mit Röntgenmikrobereichsanalyse EDAX GENESIS
- Feldemissions-Rasterelektronenmikroskop NEON40EsB mit EDXS und EBSD
- Transmissionselektronenmikroskop HITACHI H8100 mit Röntgenmikrobereichsanalyse EDAX GENESIS
- Nanoindenter UNAT
- MatLab
- Mathcad
- Deform
- Fluent
- JMatPro
- ABAQUS
- ANSYS
- MemBrain
- Modellversuche im Labor
- Kochversuch (Interkristalline und Spannungsriss-Korrosionsprüfung
- Korrosionsprüfkammer HK 400
- Potentiostat PS6 (Ermittlung von Stromdichte-Potenzialkurven)
- Elektrochemische MiniCell (ECMC)
- Loch- und Spaltkorrosionsprüfung, ASTM G48
- Klimaprüfschrank
- Mikrokorrosionszelle
- Korrosionsprüfkammer HK 430
- 3-D Profilometer
- pH-Wert-Messgerät
- Röntgenfluoreszenz-Materialanalysegerät
- Farb- und Glanzmessgerät BYK Gardener spectro-guide