Metallische Werkstoffe und Werkstoffermüdung
Willkommen im Bereich der Abteilung Metallische Werkstoffe und Werkstoffermüdung.
Fokus unserer Abteilung ist die Erforschung der Wirkbeziehungen zwischen dem Herstellungs- und Verarbeitungsprozess, der Mikrostruktur und den resultierenden Eigenschaften eines Werkstoffes (mechanisch, korrosiv, tribologisch). Das Verständnis dieser Wechselwirkungen ermöglicht die zielgerichtete Gestaltung des Werkstoffes für den jeweiligen Anwendungsfall.
Die mikrostrukturelle und mechanische Charakterisierung des Werkstoffes sowie insbesondere das Werkstoffverhalten unter zyklischer Beanspruchung, unterstützt durch Simulation, sind dabei Grundlage. Unser untersuchtes Werkstoffspektrum konzentriert sich vor allem auf metallische Werkstoffe, besonders Stähle, Aluminiumlegierungen sowie Hoch- und Mediumentropielegierungen. Unsere Expertise liegt zudem auch im Bereich der Ermüdung anodischer sowie plasmaelektrolytischer und thermisch gespritzter Schichtsysteme.
Unter den an der oberen Kante dieses Bildschirmbereichs dargestellten Reitern finden Sie genauere Ausführungen zu unseren Forschungsleistungen, den angebotenen Dienstleistungen und der umfangreichen geräte- und methodentechnischen Ausstattung unserer Abteilung.
Haben Sie darüber hinaus Fragen, oder können wir Sie in Ihren Aufgaben unterstützen? Dann sprechen Sie uns einfach unter unten stehender Telefonnummer oder E-Mail-Adresse an.
Wir freuen uns auf eine Zusammenarbeit!
Im Folgenden finden Sie eine Auswahl unserer aktuellsten Forschungsthemen und -projekte.
Gern beraten oder unterstützen wir Sie mit unserer Expertise bei der Lösung Ihrer Aufgaben. Sprechen Sie uns einfach an!
- Modellierung der Werkstoff- und Oberflächenveränderungen für die FEM-Simulation des Gesenkschmiedens von Kohlenstoffstählen
- Simulationsbasiertes Eigenschaftsdesign entlang der kombinierten Prozesskette Ur- und Umformtechnik
- Rissfortschrittsverhalten hochgradig plastisch umgeformter Mediumentropielegierungen in Abhängigkeit der Mikrostruktur
- Ermüdungsverhalten anodisch und plasmaelektrolytisch oxidierter hochfester Aluminiumlegierungen
- Mikrostrukturelle und mechanische Eigenschaften elektrochemisch und thermisch beschichteter additiv gefertigter Bauteile
- Qualifizierung metallischer Folien für ultra-dünne Bipolarplatten in Brennstoffzellenstacks
- DFG-Forschungsgruppe 5380 „Funktionsflächen durch adiabatische Hochgeschwindigkeitsprozesse: Mikrostruktur, Mechanismen und Modellentwicklung - FUNDAM3ENT https://www.for-5380.de/
- DFG Schwerpunktprogramm SPP2013: Verbesserung des Einsatzverhaltens inkrementell umgeformter Bauteile durch gezielte Eigenspannungsinduktion https://www.mec.ed.tum.de/utg/spp-2013/
Das Dienstleistungsangebot der Abteilung Metallische Werkstoffe und Werkstoffermüdung umfasst neben analytischen und untersuchenden Aufgaben auch die simulationsgestützte, gezielte Werkstoffentwicklung.
Die uns dafür zur Verfügung stehende technische Ausrüstung finden Sie nach Laborbereichen geordnet unter dem entsprechenden Reiter auf dieser Seite.
Standardmäßig bieten wir die folgenden Dienstleistungen an.
Sprechen Sie uns an, wenn wir Sie in speziellen Aufgaben unterstützen sollen!
- Röntgenfeinstrukturanalyse mittels XRD:
- qualitative und quantitative Phasenanalyse und Bestimmung der Gitterparameter
- Bestimmung von Teilchengrößen und Mikroverzerrungen
- Eigenspannungsmessung
- Texturanalyse
- Schichtdicken-, Rauheits- und Dichtebestimmung mittels Reflektometrie
- simultane Durchführung von Thermogravimetrie (TG) und wahlweise Differenz-Thermo-Analyse (DTA) oder Dynamische Differenz-Kalorimetrie (DSC)
- Thermomechanische Analyse (TMA) zur Bestimmung des Verhaltens von Werkstoffen unter mechanischer und thermischer Beanspruchung
- mechanische Prüfung unter Zug, Druck, Biegung und Scherung
- Verschleißprüfung im Festkörperkontakt
- Korrosionsprüfung
- Ermüdungsprüfung im LCF- und HCF-Bereich unter Zug-, Druck- und Biegebelastung
- Wärmebehandlungen nach Vorgabe und Entwicklung von Wärmebehandlungsroutinen
- Hochenergiekugelmühle Zoz Simoloyer CM08-8l
- Hochenergiekugelmühle Zoz Simoloyer CM01-2l / SiN
- Planetenkugelmühle Fritsch Pulverisette 5
- Pulververdüsungsanlage
- AMC-Gießeinrichtung
- Lichtbogenofen (Nutzung über Professur PVW)
- Spark-Plasma-Sinteranlage (SPS) (Nutzung über Professur PVW)
- verschiedene Muffel- und Schutzgasöfen sowie Abschreckbäder
- Materialografische Präparationstechnik
- Elektronenmikroskopische Präparationstechnik
- Lichtmikroskopische Untersuchungstechnik
- Quantitative Gefügeanalyse OLYMPUS a4i
- Mikrohärte-Prüfgerät DURAMIN
- Registrierende Härtemessung FISCHERSCOPE HM2000 XYm
- Rasterelektronenmikroskop LEO1455VP mit Röntgenmikrobereichsanalyse EDAX GENESIS
- Feldemissions-Rasterelektronenmikroskop NEON40EsB mit EDXS und EBSD
- Transmissionselektronenmikroskop HITACHI H8100 mit Röntgenmikrobereichsanalyse EDAX GENESIS
- Nanoindenter UNAT
- Resonanzpulsator RUMUL - Wöhlerversuche
- Resonanzpulsator RUMUL - Rissfortschrittsversuche
- MTS Landmark (100kN) Ausstattung – dehnungsgeregelte Ermüdungsversuche
- MatLab
- Mathcad
- Deform
- Fluent
- JMatPro
- ABAQUS
- ANSYS
- MemBrain
- Modellversuche im Labor
- Kochversuch (Interkristalline und Spannungsriss-Korrosionsprüfung
- Korrosionsprüfkammer HK 400
- Potentiostat PS6 (Ermittlung von Stromdichte-Potenzialkurven)
- Elektrochemische MiniCell (ECMC)
- Loch- und Spaltkorrosionsprüfung, ASTM G48
- Klimaprüfschrank
- Mikrokorrosionszelle
- Korrosionsprüfkammer HK 430
- 3-D Profilometer
- pH-Wert-Messgerät
- Röntgenfluoreszenz-Materialanalysegerät
- Farb- und Glanzmessgerät BYK Gardener spectro-guide
Ansprechpartnerin
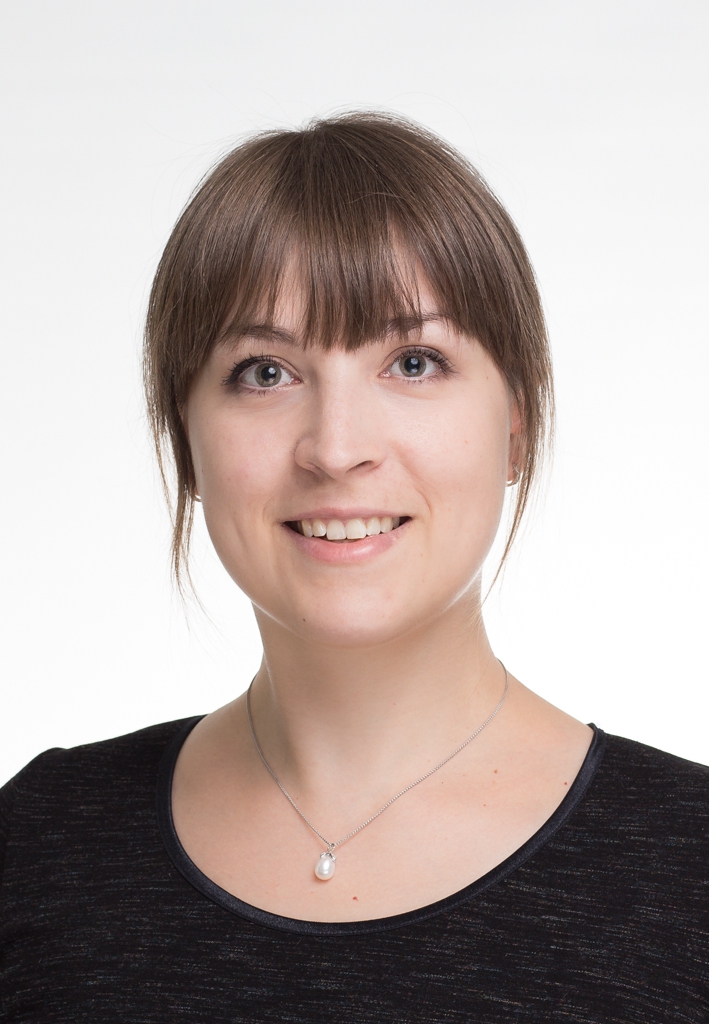