Querschnittsarbeitsgruppe Modellierung und Simulation (QuAG-MoSi)
Willkommen bei der Querschnittsarbeitsgruppe Modellierung und Simulation (QuAG-MoSi)
Die Querschnittsarbeitsgruppe befasst sich mit der Modellierung und Simulation von
werkstoff- und oberflächenspezifischen Themen wie bspw. galvanische Abscheidung,
Wärmbehandlungsrouten, Nitrierprozesse und Lebensdauerbestimmung.
In unserer Gruppe arbeiten Wissenschaftler:innen zusammen, die entweder bereits Experten
sind oder sich bezüglich Modellierung und Simulation austauschen und weiterbilden wollen.
Inhaltlich hat die Gruppe folgende Schwerpunkte:
- Materialcharakterisierung und Datenbanken
- Mathematische und numerische Prozessmodellierung
- Prozess- und Werkstückauslegung anhand direkter Simulation
über die Reiter dieser Website finden Sie weitere Ausführungen zu unseren Forschungsleistungen.
Gern greifen wir auch Ihre FuE-Themen auf. Sprechen Sie uns bitte via Telefon oder E-Mail an. Wir freuen uns auf eine Zusammenarbeit!
Zu den aktuellen Forschungsgebieten der Querschnittsarbeitsgruppe Simulation gehören mathematische Modellierung, Validierung und Simulation galvanischer Abscheidungen, mathematische Modellierung von Nitrierprozessen, die Lebensdauerberechnung eigenspannungsbehafteter Bauteile sowie die Erstellung von Materialdatenbanken zur globalen Speicherung und Nutzung von experimentellen Ergebnissen.
Die oben aufgezählten Themengebiete stellen nur eine Auswahl aktueller und vergangener Forschungsgebiete dar. Durch den Zugriff auf klassische FE-Programme sowie die Erstellung eigener Solver via MatLab sind wir in der Lage, viele andere Themen aus der Werkstoff- und Oberflächentechnik zu modellieren. Zusätzlich können wir Materialdaten wie Fließkurven, Phasenumwandlungen, ZTU-Diagramme und Wöhlerkurven sowohl simulativ, als auch experimentell ermitteln.
Im Folgenden finden Sie eine Auswahl unserer wichtigsten Forschungsthemen in den o.g. Gebieten.
Gern beraten oder unterstützen wir Sie mit unserer Expertise bei der Lösung Ihrer Aufgaben. Sprechen Sie uns einfach an!
Das Erfüllen steigender Anforderungen in der Galvanotechnik an Abscheidungen auf komplex ausgeformter Ware mit hohen Ansprüchen an die Schichthomogenität erfordert eine aufwändige Elektrolyt- und Prozessentwicklung. Aktuelle Entwicklungen in der Modellierung elektrochemischer Prozesse, mathematische Algorithmik und Rechentechnik nehmen auch in der Galvanotechnik Einzug.
Unterstützend zur Prozess- und Elektrolytentwicklung forscht die Arbeitsgruppe an der Simulation galvanischer Abscheidungen. Beispiele:
- Simulation von Stromdichteverteilungen während der Abscheidung
- Mathematische Modellierung und Simulation der anodischen und kathodischen Stromdichte während der Abscheidung
- Simulation und Kennwertbestimmung für die Komplexbildung in Elektrolyten aus Titrationskurven
- Mathematische Modellierung und Methodenentwicklung der Prozesse während der Abscheidung in der Diffusionsgrenzschicht für DC- und Pulse-Plating-Abscheidungen
Ein weiteres wichtiges Thema ist die mathematische Modellierung und Simulation von Nitrierprozessen. Die Arbeiten konzentrieren sich auf die mathematische Modellierung der Stickstoff- und Kohlenstoffkonzentration in der zu nitrierenden Probe und die statistische Korrelation der simulierten Konzentrationsverläufe mit der Wirkung auf Oberflächenhärte, Nitriertiefe und Konversionsschichtgefüge.
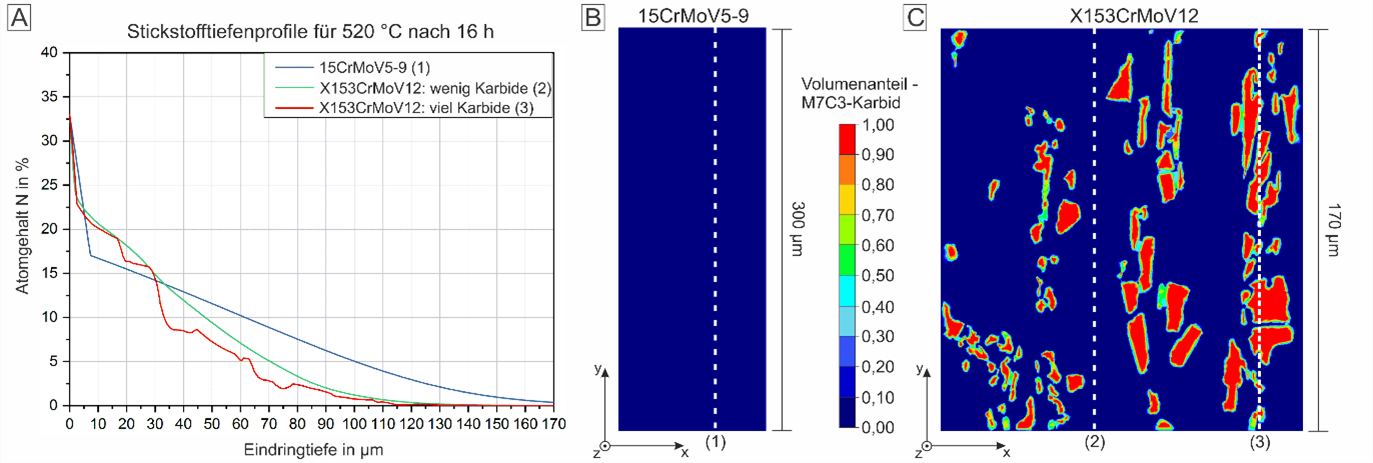
Ein weiterer essentieller Bereich ist die Ermüdung von Bauteilen. Durch die Programmverwandtschaft des FE-Programms ABAQUS mit dem Lebensdauertool fe-safe ist es möglich den Herstellungsprozess eines Blechzuschnittes durch inkrementelle Blechumformung zu simulieren und die durch den Fertigungsprozess entstandenen Eigenspannungen sowie Geometriebesonderheiten in der Lebensdauerberechnung zu berücksichtigen. Hierdurch lässt sich die Lebensdauer als Folge eines verbesserten Fertigungsprozesses über Optimierungsalgorithmen steigern.
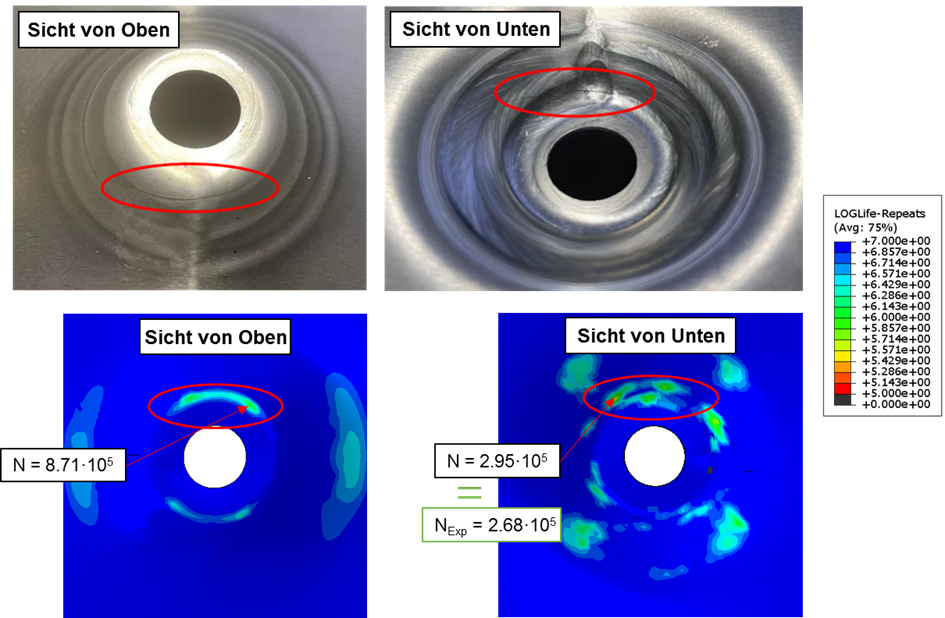
Zunder ist ein bekanntes Problem in der Warmumformung von Stählen oder Kupferlegierungen und wird wenig bis gar nicht bei Simulationen von Walz- und Schmiedeprozessen berücksichtigt. Durch die Charakteristik des Zunders weist das Eigenschaftsprofil der Eisenoxidphasen deutliche Unterschiede zum Grundmaterial auf. Aus diesem Grund kann eine stark verzunderte Oberfläche nicht nur das Umformverhalten des Werkstückes, sondern auch die Temperatur- und Spannungsverteilung beeinflussen. In einem Projekt wurden die Zunderwachstumskinetik und der Schichtaufbau für verschiedene Stähle bei variierenden Temperaturen und Zeiten ermittelt. Diese Daten wurden durch mathematische Modelle beschrieben und mittels Subroutinen in ein FE-Tool implementiert. Das Ergebnis ist eine dynamisch wachsende Schicht während der Wärmebehandlung, die innerhalb eines nachgelagerten Warmumformprozesses Berücksichtigung findet.
Der Umgang mit wissenschaftlichen Daten befindet sich im Umbruch. Noch werden die
meisten experimentell anfallenden Daten, bestehend aus der Fragestellung, der
Versuchsanordnung, der verwendeten Materialien und Methoden sowie der Analyse und
Interpretation der Ergebnisse, traditionell analog festgehalten.
über die Digitalisierung führen FDM-Systeme diesen Teil der Information, mit den ohnehin
digital vorliegenden Rohdaten, analysierten Daten und Skripten, zentral in einer Datenbank
zusammen. FDM-Systeme ermöglichen nicht nur das Speichern und Strukturieren von
sogenannten Forschungsdaten, sondern auch die ontologische Abbildung der
Versuchsdurchführung und aller damit verbundenen Entitäten, wie beispielsweise der
verwendeten Probe, der Messbedingung oder der wissenschaftlich verantwortlichen Person als
Initiator des Versuchs. Dem FDM liegt das Paradigma des Findable,
Accessible, Interoperable, Reusable-Prinzips
zu Grunde. über das FAIR-Prinzip wird das persistente Abspeichern und
Referenzieren der Forschungsdaten sichergestellt sowie über das Verwenden von quelloffenen,
etablierten Datenformaten, das Weiterverarbeiten auf unterschiedlichen Systemen ermöglicht.
Gegenwärtig etabliert die Professur Werkstoff- und Oberflächentechnik im Rahmen eines
DFG-Projektes ihr eigenes FDM unter Benutzung des FDM-Systems „openBIS“. Hierbei
handelt es sich um eine (Open Source) Datenbank, die speziell für Labore an
Forschungseinrichtungen entwickelt wurde.
Ansprechpartner
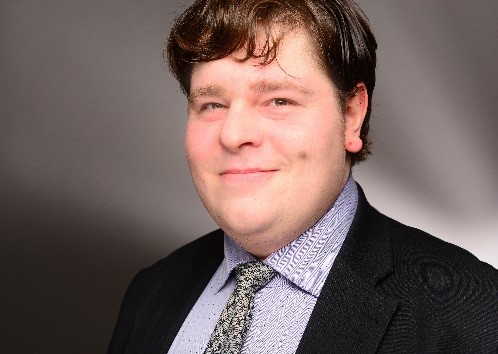