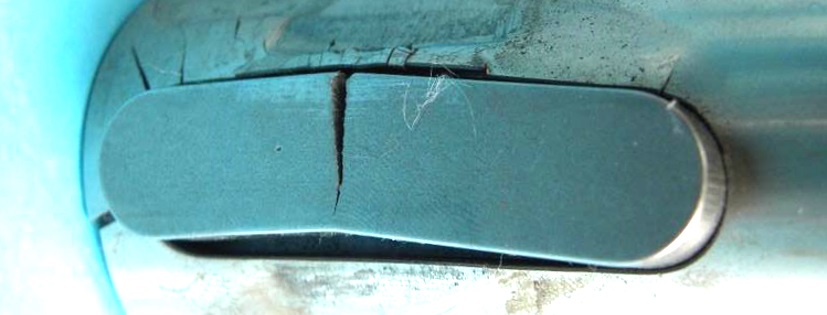
Shaft-Hub Connections
Strength tests in time, fatigue and fatigue strength on selected positive and non-positive joints
In the course of the globalisation of markets and the associated increases in performance, the ever more compact drive train is forcing the utilisation of the available power. of all strength reserves. For this reason, the design of selected shaft-hub connections (SHC) in the area of fatigue, fatigue and fatigue strength has been the main focus for decades. at IKAT. The behaviour under individual loads (bending, torsion) as well as combined dynamic loads is analysed and interpreted.
The complex interaction between stress mechanical stress and other wear parameters (e.g. friction corrosion) make experimental use of the Investigations on the transmission behaviour of SHC are irreplaceable. These are accompanied by various simulation tools and ultimately also serve to their validation. The tests are carried out on taper and cylinder interference fit as well as feather key, knurled and polygonal joints. The focus of the investigations is the fatigue strength (or long-term strength) of the SHC. However, investigations are also carried out in the fatigue strength range and the fatigue strength.
The numerical structural analyses of the WNV are carried out by the FE software ABAQUS. A Professure calculation cluster is available for this purpose. Other mathematical problems are solved with MathCAD or MATLAB®.
The current state of research can be applied to a complete gearbox design via the FVA Workbench.