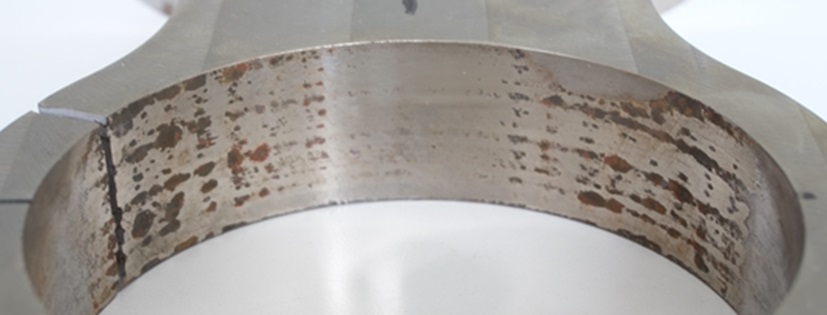
Fretting Fatigue
Interdisciplinary Research between Tribology and Strength Strength Assessment of Joints at Risk of Friction Fatigue Fracture
Today's machine elements are exposed to ever greater loads and correspondingly higher demands. This development has resulted in greater deformation of the components. In dynamically loaded Due to different stiffnesses of the connected parts, these deformations occur as relative movements appear. In contact, these initiate the damage process of the frictional fatigue as a function of the joint pressure. The research at the institute is therefore concerned with the topic of strength calculation under additional continuous frictional stress.
Quantification of the fatigue strength as a function of the tribological contact variables joint pressure and slip. In addition to the basic research of the contact parameters, the further consideration focuses on the influencing factors of the coefficient of friction, the wear and the material. Depending on the influences mentioned above, the aim is to determine the fatigue behaviour of joints subjected to long-term friction loads. generally valid and to be implemented in a strength analysis.
Experimental determination of fatigue strength on the test bench RKP100 (left) and at the connecting rod device of the HPP250 (right).
Conversion of the system-specific nominal stress related fatigue strength into a local stress state by means of contact simulation, taking into account the experimental friction values as well as the measured motion sequences between the contact partners. The simulations are carried out with the FE software ABAQUS.