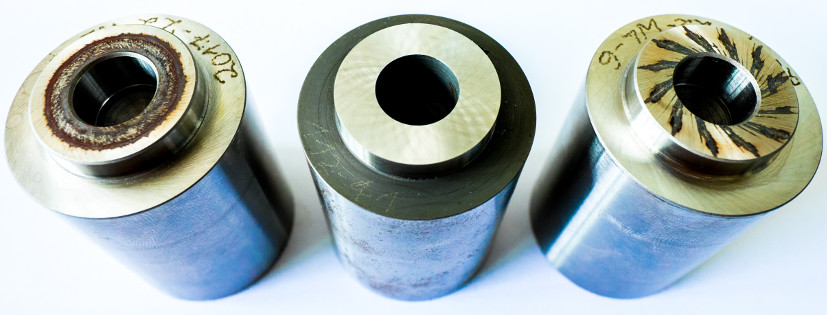
Friction coefficients for force-locked Connections
Investigations of the static/dynamic friction coefficient behaviour with standardized model test methods on laboratory samples
Growing economic and ecological pressure as well as increased technical requirements lead to higher power densities for the force-transmitting/force-locking components. The frequently used frictional connections (e.g. screw, flange, press-fit connections) offer a considerable increase potential in power density and wear resistance. For over 10 years, IKAT has been using model-based laboratory tests to investigate the coefficient of static friction (also: coefficient of friction or coefficient of friction) under static and dynamic conditions. dynamic load. The main areas of research are the characterization of friction-locking surfaces, friction-value-increasing applications, and Remedial measures against vibration wear (Fretting Wear).
The coefficient of static friction is to be understood as a system variable with a multitude of influencing parameters. In order to use existing potentials in friction-locking connections, an experimental investigation is indispensable. With the help of standardized Test methods on model samples are examined at the research centre with regard to their transfer behaviour in various tribological configurations. A main field of research is the synthesis of new design/selection tools for friction-enhancing measures (e.g. micro/laser structures, hard particles, coatings). for static and dynamic load cases. Furthermore, the suitability of remedial measures against vibration wear can be examined and evaluated with the aid of the test procedures.
Simulation of friction coefficient evolution in dynamically loaded machine component contacts
Funding agency: | BMWi |
Research association: | FVA |
Duration: | 24 Months |
End time: | Oct 2023 |
Editor: | Silvano Giuseppe Oehme |
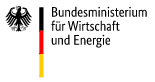
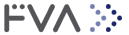
Friction coefficients in press-fit connections
Funding agency: | BMWk |
Research association: | FVA |
Duration: | 12 Months |
End time: | Jul 2022 |
Editor: | Jonathan Schanner |
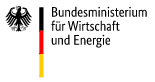
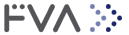
Investigations of fretting wear highly stressed hybrid shaft-hub joints
Funding agency: | Industrie |
Research association: | - |
Duration: | 24 Months |
End time: | Feb 2022 |
Editor: | Silvano Giuseppe Oehme |
Tribomaps for friction enhancing laser structures
Funding agency: | BMWk |
Research association: | FVV |
Project partners: | LHM Mittweida |
Duration: | 30 Months |
End time: | Oct 2022 |
Editor: | Jonathan Schanner |
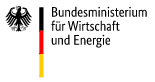

Research and development of a new type of rotor design using segmented sheet packs - Tribology subproject
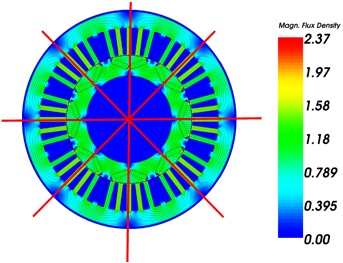
Funding agency: | SAB |
Research association: | - |
Duration: | 30 Months |
End time: | Aug 2020 |
Editor: | Silvano Giuseppe Oehme |

Investigations on the transferability of model-based static friction values and friction characteristics to joined real components
Development of an evaluation procedure for the design, selection and optimisation of anti-fretting coatings in line with the stresses involved
Benchmark study "Anti-fretting coatings"
GECKO - Design and Determination of Characteristic Values of Friction Optimized Surfaces | Subproject I: Analysis and Synthesis of Characteristic Values for Functional Design of Die Face Pairs in Frictional Joints

Funding agency: | BMWi/DFG |
Research association: | FVV |
Project partners: | IFMQ (TU Chemnitz); Institut für Maschinenkonstruktion (Otto-von-Guericke-Universität Magdeburg); Fraunhofer-Institut für Werkstoff- und Strahltechnik; Laserinstitut (Hochschule Mittweida) |
Duration: | 36 Months |
End time: | Jun 2014 |
Editor: | Matthias Gräfensteiner |
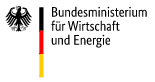

