Fully automated robot-assisted electroplating plant - LaborRob
Due to increasing technical requirements (e.g. high corrosion resistance) and the regimentation of proven coating systems and chemicals, the development of new electrolytes and processes for the electrochemical deposition of metallic coatings is necessary. In particular, alloy deposition enables the substitution of "problematic" coating systems and/or the improvement of coating properties using pulsed current forms. In view of the large number of combinatorially possible alloy systems, the wide variety of available complexing agents and additives as well as the large variety of pulse shapes, research into new electrolyte systems is hardly manageable according to the conventional, empirical approach.
Therefore, within the framework of the joint project "REACH-compliant corrosion protection by pulse plating (ReKoPP)" funded by the BMBF, a robot-supported electroplating plant was planned and implemented in close cooperation between the companies KleRo GmbH Roboterautomation, OTE Oberflächen- & Elektrotechnik Scheigenpflug GmbH, plating electronic GmbH and the Chair of Materials and Surface Engineering. After defining a statistical test plan that enables maximum coverage of the parameter space with a minimum number of tests, the coating processes are carried out fully automatically, with the exclusion of individual disturbing influences and, if necessary, also overnight. Thanks to the multitasking mode, up to 3 coating processes can be carried out in parallel.
Instrumentation:
Industrial robots:
- Company ABB, 5 rotary axes
- Gripper for holding the sample carriers
- Magnetic holder for pipetting device
9 exchangeable coating baths:
- Volume: 0.5 l to 2 l
- Coating area: max. 5 × 10 cm²
- Fabric movement parallel to the counter electrode
- heatable through heating plate
- Sensors: filling level, pH value, temperature
2 solid coating baths:
- Volume: approx. 10 l (incl. electrolyte circuit)
- Coating area: max. 5 × 10 cm²
- Electrolyte movement through pumping
- Heatable through heat exchanger
- Sensors: filling level, pH value, temperature
Power sources:
- 18 Pulse current sources for coating baths
- Synchronous operation of 2 pulse current sources possible
- 2 separate power sources for pre-treatment
2 pre-treatment baths:
- (electrolytic) degreasing
- (Electrolytic) pickling
Cascade sink:
- up to 4 rinsing levels
- Variable flow rate
- Counterflow principle
other components:
- Storage area for 12 sample carriers
- Dryer
- 4 Additive container
- Photo documentation
- Video documentation and remote diagnosis
Typical workflow:
- Removal of a sample holder
- (electrolytic) pickling, (electrolytic) degreasing, rinsing steps
- Electrochemical coating, in multitasking mode the pre-treatment of a second and third sample takes place during sufficiently long coating times
- Sinks
- Drying
- Photo documentation of the sample
- Sample deposit
- if required: Subsequent dosing of additives or taking of an electrolyte sample by means of a pipetting device
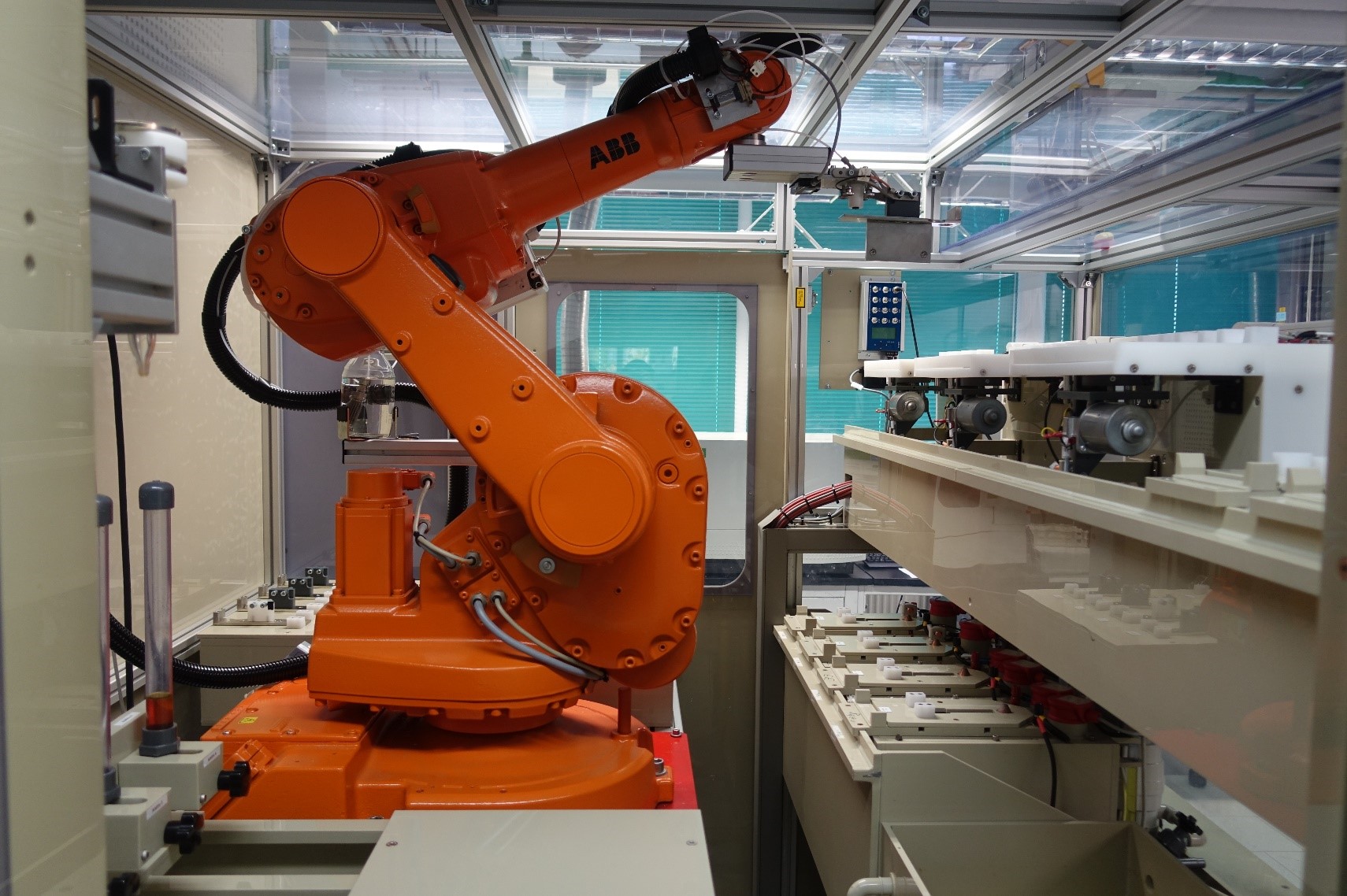
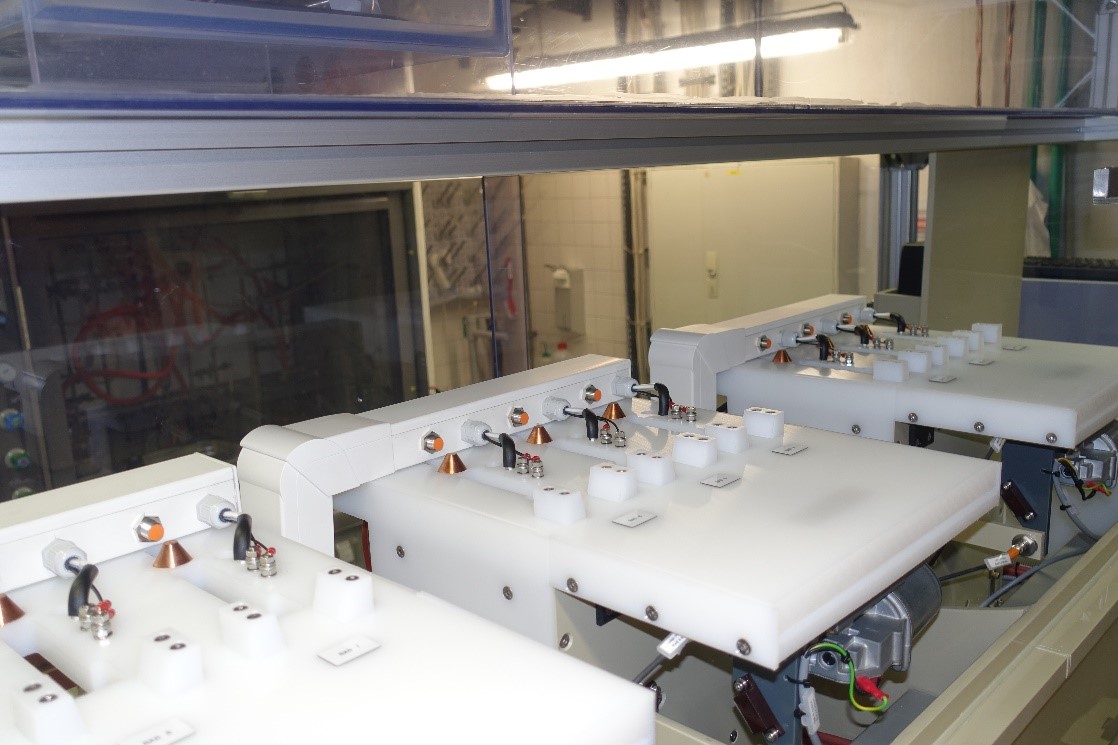
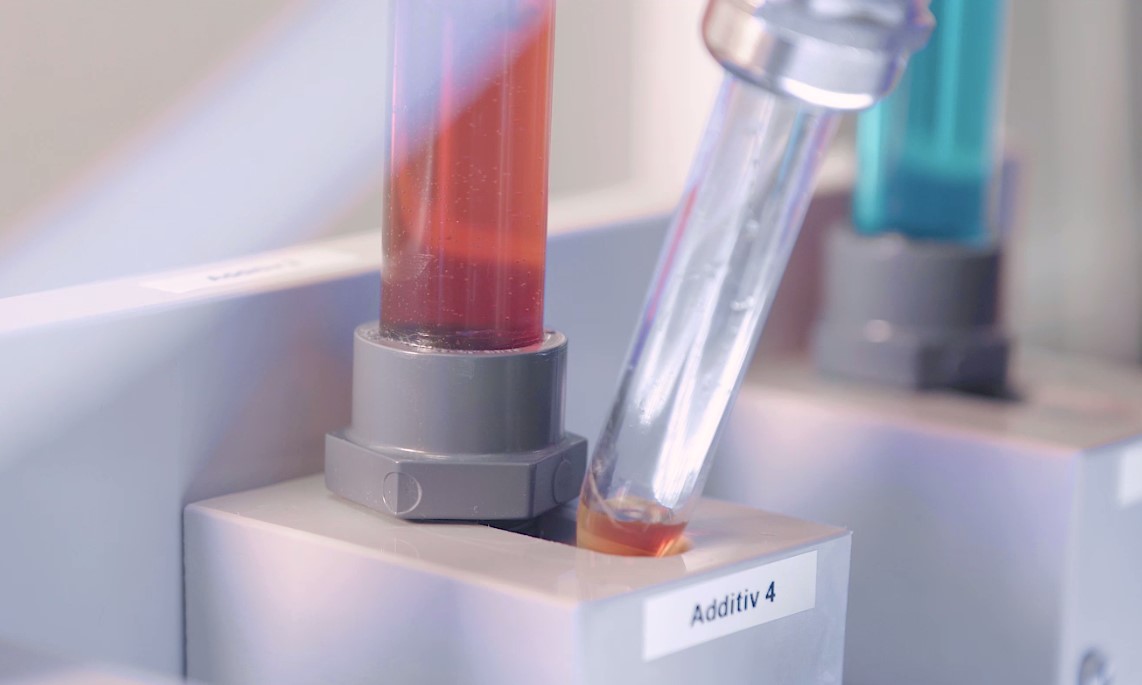