Equipment
Controlled Environment Agriculture (CEA) Lab
In addition to standard equipment for the processing of biological samples (e.g., drying oven, precision scales, etc.), the following devices are already available for use in experiments:
- 3 lab-scale indoor vertical farm units
- Light intensity and spectrum measurement device
- NIR-spectrometer with reflectance sensor
- UV-VIS spectrophotometer
- Chlorophyll fluorometer
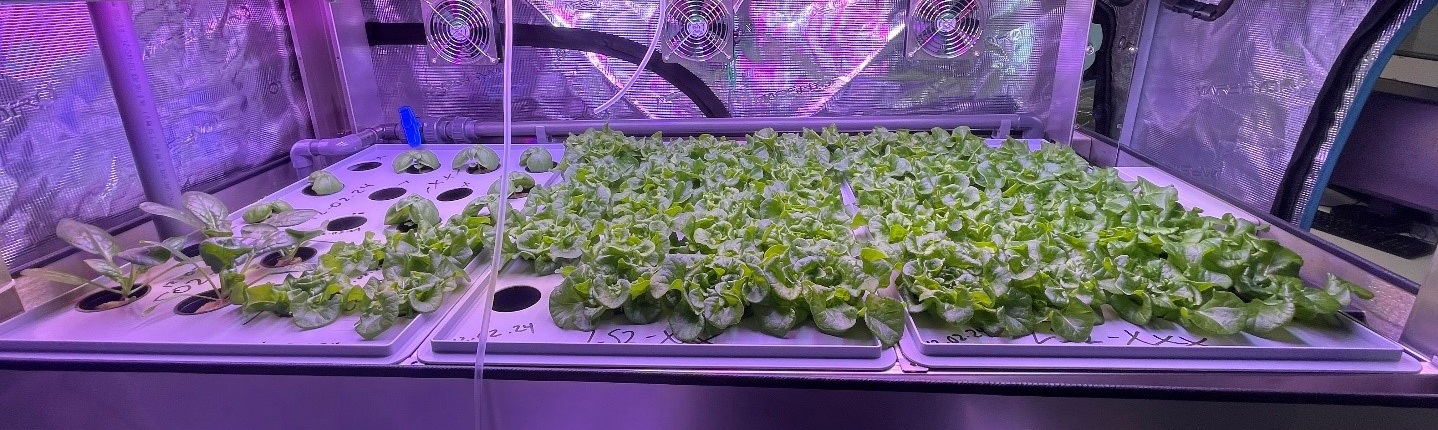
The equipment selection in the CEA lab is meant to produce and then characterize biological samples, particularly plants. The indoor vertical farm units are hydroponic culture systems that allow for the automatic control of several factors relevant to plant cultivation, such as pH, EC value, and light spectrum. The photosynthetic activity of the plants can be continuously monitored through the chlorophyll fluorometer, while the NIR-spectrometer and UV-VIS spectrophotometer can provide information about product composition and concentrations of species of interest. It is planned that the capabilities of the lab will be expanded further in the near future.
Research Laboratory for Agricultural and Energy Systems
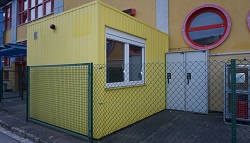
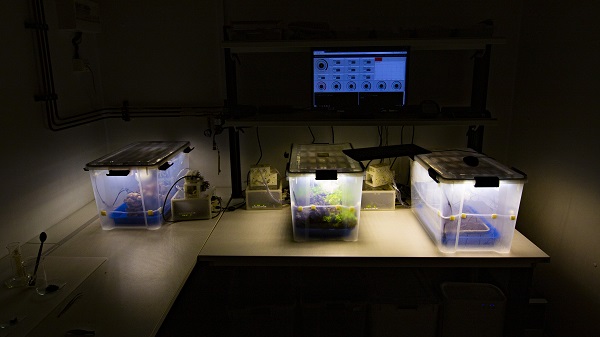
The laboratory is specially equipped with custom built growth chambers incorporated with an assortment of sensors and actuators to perform studies on growth of biological organisms (e.g. plants, mushrooms, larvae etc.) under controlled environmental conditions. These devices are used as test benches to perform specific experiments to capture data which is then used to develop mathematical models and control methods applicable to indoor food production. The laboratory is also facilitated with measurement equipment, biomass processing tools (e.g. drying oven, cooling chamber, etc.) and the infrastructure to perform studies on energy systems (e.g. Fuel cells etc.)
Sensor vehicle for investigation of soil parameters
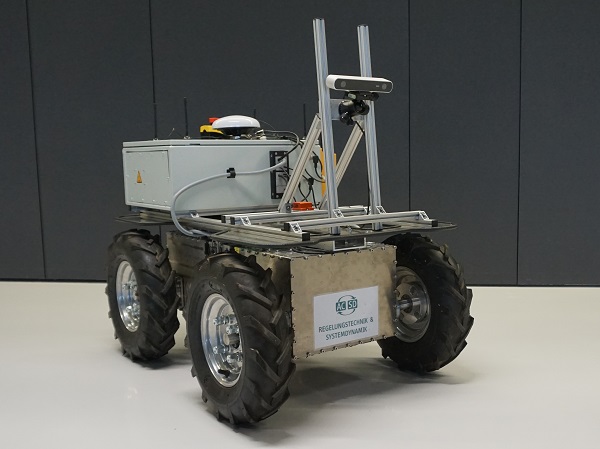
The vehicle is equipped with numerous sensors, which are important for investigating soil parameters and for traction control. Some of them are rotation and torsional sensors at the electric motor, a force-momentum-sensor at the right rear wheel, which measures forces in all directions and momentums around all axes, a traction sensor, a camera, GPS and an inclinometer.
For steering purposes, a Raspberry Pi is mounted on top of the vehicle, which acts as an interface between robot hardware and human and for data storage, data evaluation, and for control. The vehicle is used in our EiNES project.
Test stand for vehicle traction control and estimation
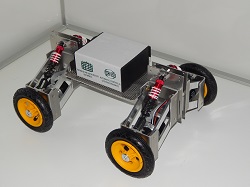
The stand comprises of a single-wheel-drive drive and a conveyor. It enables testing traction control algorithms in a lab environment.
The control is realized real-time by a dSPACE microcontroller with accompaying software and MATLAB. The test stand has a number of features, inlcuding single-wheel suspension, to improve authencity of imitating on-field traction conditions.
Due to the nonlinearities, varios disturbances and model uncertainties the rig offers the possiblity to implement and test advanced control methods in real time.
Control lab for student education
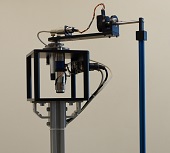
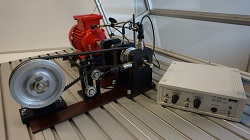
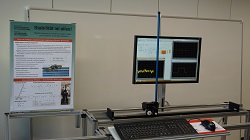
In the control lab students work on different relevant problems within our research topics and test, e.g., new methods for control and diagnostics. The here presented experimental setups also serve as demonstrations in lectures and exercises as well as on university events (e.g. open house day). Examples for the variety of control engineering experiments in our professorship are:
- Linear inverted pendulum from Quanser Inc. (Markham, Kanada)
- Condition-Monitoring-System PT 500 from G.U.N.T. Gerätebau GmbH (Hamburg)
- Rotatory inverted pendulum from Quanser Inc. (Markham, Kanada)
- Ball and plate system from Quanser Inc. (Markham, Kanada)
- Magnetic levitator from Quanser Inc. (Markham, Kanada)