Current projects
ISyKat
BMWK - FKZ: 8 Online identifier: 100369765
Development of impinging jet microreactor synthesis processes for the cost-effective production of Pt, PtMx alloy and M@Pt core-shell PEMFC catalysts (M = Ni, Co etc.)
The project is a cooperation project with Umicore AG funded by the BMWK.
Modern electrocatalysts for PEM fuel cells are based on the use of platinum or platinum alloys on carbon support materials. The classic batch process used for production limits the production volume and can only be scaled up with quality losses and high costs. New, more efficient production processes are therefore being sought.
In impinging jet microreactor technology (also known as microjet reactor technology), two or more partial jets of different chemical reaction solutions are mixed within 0.1 ms before particle formation by nuclei begins after approx. 1 ms. This technology allows the controlled production of nanoparticles with high quality in a continuous, volume-scalable process. In this chemical-process engineering project, an alternative, significantly more energy- and material-efficient, continuous production process for catalyst and carrier components for fuel cell applications is being developed by further developing and optimizing this method.
For this purpose, a modular system consisting of two series-connected structurally improved microjet reactors and a water evaporator will be designed and constructed so that a continuous synthesis of metallic and intermetallic nanoparticles based on noble metals can be carried out by reductive (co-)precipitation under elevated pressures up to hydrothermal conditions.
The experimental design is based on a Design of Experiment (DoE) and the experiments are carried out accordingly. Variation parameters are precursors or precious metal salts, reducing agents, solvents, additives or auxiliaries, precipitants and their concentrations and pH-values, as well as reaction temperatures and fluid flows, from which pressures, mixing times and supersaturation result. The target parameters particle size, dispersion, morphology, texture and crystallinity are investigated in aging tests.
The characterization of the particle size and distribution of the obtained electrocatalysts is carried out after synthesis in dispersion with dynamic light scattering (DLS). A likewise continuous separation of obtained particles from dispersants and auxiliaries is enabled by a UF/NF filtration module. After drying, the obtained solid electrocatalysts can be examined with respect to particle morphology and texture by SEM/TEM and other methods such as XPS, SAXS, XRD, etc. Electrochemical activity tests via cyclic voltammetry (CV) of the obtained NP, especially in supported form, are exclusively performed by the cooperation partner Umicore AG.
RANS and DES simulations within CFD calculations are performed to model the flow behavior in the sequentially switched microjet reactors.
MeOHKat
Alfred Kärcher Support Foundation
Catalyst development for the utilization of climate-damaging CO2 via technical methanol synthesis
This project is an environmentally relevant research project supported by the Alfred Kärcher Support Foundation.
The aim of the development is to synthesize a catalyst material from the class of multinary transition metal oxides that is suitable for converting carbon dioxide (CO2) and hydrogen (H2) into methanol (H3COH) with high selectivity and thus contributing to the reduction of CO2 in the environment. So far with the catalysts described in literature in the state of art, the conversions and selectivities achieved still need further improvement. The decisive factor here is the methanol selectivity in thermodynamic equilibrium: this only reaches over 95% at pressures above 50 bar and temperatures of 200°C. The refining product methanol itself is not only a sought-after raw material in industry and can be reused in an environmentally friendly way in fuel cells for energy generation, for example, or used to produce fuels (methanol to gasoline), but is also an important energy storage compound: the hydrogen it contains can be released again by steam reforming, and the carbon dioxide that is released closes the carbon cycle.
For the synthesis of the catalyst materials to be developed, co-precipitates from aqueous media or impregnations of commercial carrier materials, for example, are to be used. These syntheses are subject to many influencing factors, such as the composition of solutions (reactants used, solvents, precipitants, anions, additives, pH), or physical phenomena (temperature, mixing sequences, supersaturation, aging), which control catalyst formation as variation parameters and must be optimized accordingly. For systematic investigation, combinatorial methods based on the principles of design-of-experiment (DoE) and high-throughput experimentation (HTE) are suitable for catalyst synthesis. The influence of the above parameters on the composition of the precipitate, its purity and homogeneity, the phases and modifications formed, crystallinity, morphology, particle size and texture significantly determine the catalytic product properties and will be investigated for the materials produced.
In a first phase, a screening of potentially interesting element combinations in combination with first variations regarding the above mentioned parameters will be carried out and introduced into the test reactor via a coating technique. Catalytic activity measurements are used as a criterion for the selection of catalysts for a subsequent optimization phase, in which the prepared samples are tested in existing parallel reactors using CO2 / H2 model gas mixtures. In addition to the pressures and temperatures required for the reaction, the degree of selectivity of the methanol formation is the decisive criterion for the selection for optimization. For this purpose, an analysis of the products formed must be carried out.
HT-H2-DeNOx
BMWK/AiF fundingnr.: 22407 BG
Catalytic NOx removal using H2 from the exhaust system of GHG-neutral lean burn H2 engines for stationary and mobile applications.
Cooperation partnership

The project is a cooperation project with the Technical University Bergakademie Freiberg (TUBAF) on environmentally relevant exhaust gas aftertreatment of potential GHG-neutral lean-burn H2 engines, funded by the BMWK and the AiF.
Lean H2 engines are a high-performance, GHG-neutral drive technology for use in large gensets in the mobile and stationary sectors (e.g. commercial vehicles, ships, CHPs). However, the high efficiencies of lean H2 engines are offset by the emission of NOx. Therefore, to comply with future ultra-low NOx limits (post-EU 7 for cars, post-Tier III for ships), exhaust gas aftertreatment for NOx removal is mandatory. In addition to established methods such as the SCR process, NOx reduction using H2 as a reducing agent (H2-DeNOx) is an effective method. This has been successfully demonstrated for both a lean burn H2 engine and a passenger car diesel engine. However, H2-DeNOx technology has so far been developed exclusively for low exhaust gas temperatures, so no H2-DeNOx catalysts currently exist for the common exhaust gas temperatures of lean burn H2 engines used in trucks, ships and CHP units. Therefore, the goal of this project is to develop an H2-DeNOx catalyst that is highly active at the relevant exhaust temperatures of 250 to 450°C, thus meeting future ultra-low NOx emission requirements.
For this purpose, more than 600 potentially active catalyst samples will be prepared and their activity investigated in cooperation between TUBAF and TUC. Using the principles of high throughput experimentation (HTE) and statistical methods for design of experiments (DoE) and data mining, a wide range of potentially active materials will be systematically screened. If the project is successful, the H2-DeNOx technique can be applied to the low-temperature and also the high-temperature range, so that AdBlue-SCR infrastructure (NH3-SCR process) can be dispensed with entirely.
On the part of the TUC-CT, a broad screening of the catalyst samples produced at the TUBAF is carried out in the first step via a sequential high-throughput screening on a motorized xyz movement unit. Analysis of nitrogen oxides for conversion calculation is performed via multivariate FTIR gas analysis in a process spectrometer. After hit identification and further optimization of the catalyst materials, a hydrothermal aging under extreme temperature conditions (T > 500 °C) in a 10-fold parallel aging reactor is carried out in the second step at the TUC-CT to verify the stability towards the catalyst poison H2O.
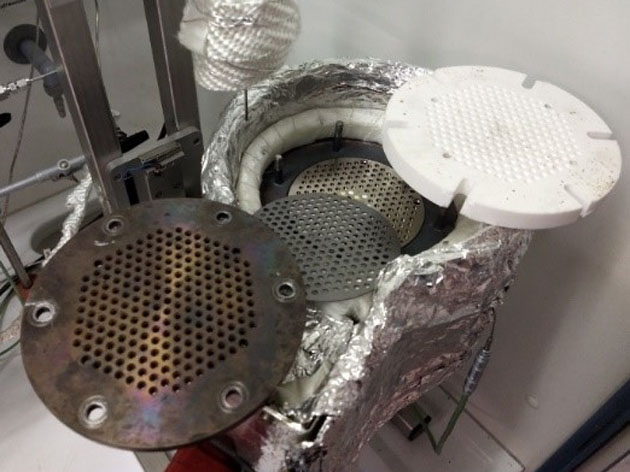
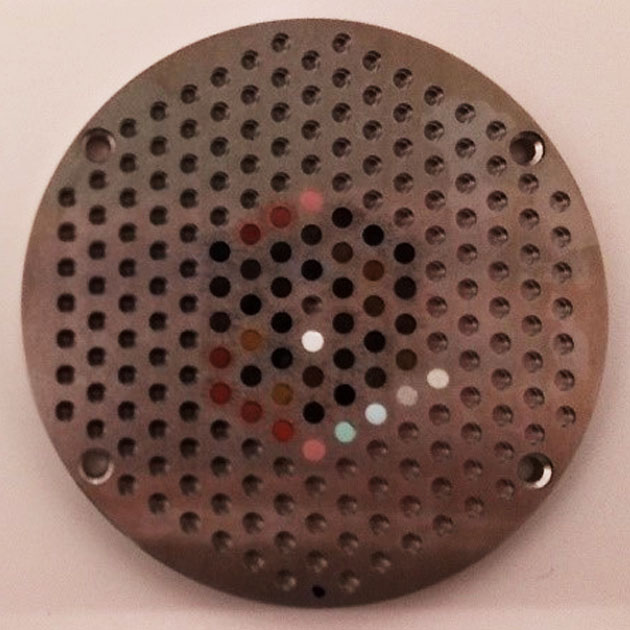
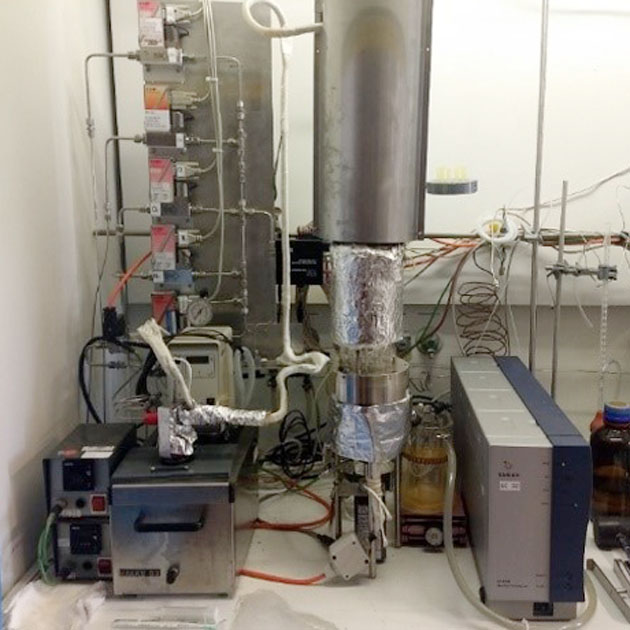
P2G-CatCarrier
AiF-IGF Project
Development of ceramic carriers for microstructured reactors for the chemical-catalytic methanation of C2
Cooperation partnership
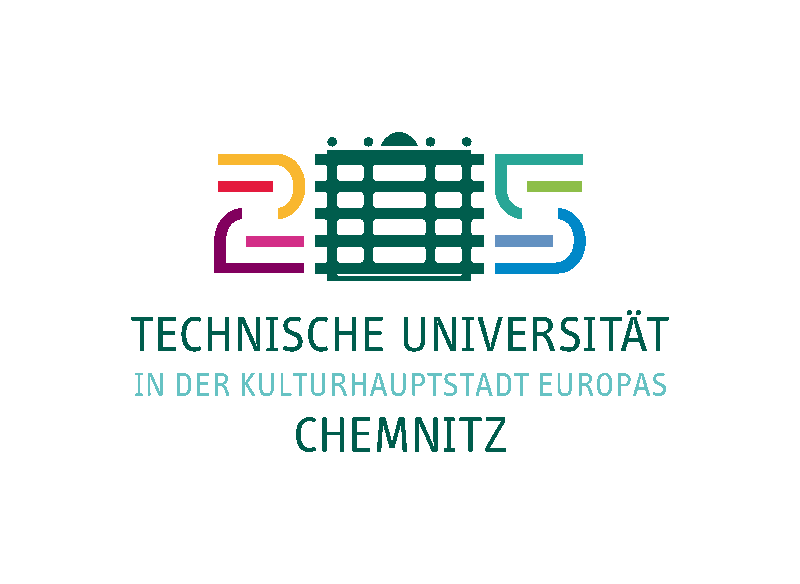
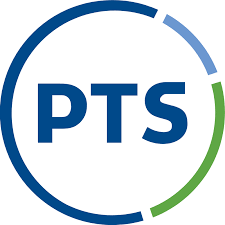
This project is an environmentally relevant research topic with funding by AiF-IGF. The increasing atmospheric concentration of the greenhouse gas CO2 creates a critical risk for the climate system, making the recyling of CO2 by chemical reaction attractive in today's environment. Using the Sabatier reaction CO2 is converted CH4, a useful storable energy carrier.
The cooperation between TUC and PTS enables the specific development of ceramic materials that serve as the basis for methanation catalysts. The impregnation technique is used to load the compact and porous ceramics with defined dimensions with active components. Physical properties such as mechanical stability, porosity and density are then tested. Imaging methods using SEM with EDX mapping provide information on the distribution of the catalytic components.
Reaction engineering testing in the microstructure reactor (p = 15 bar, T = 300 °C) taking advantage of beneficial microstructure effects such as an intensification of mass and heat transport, is used to test the CO2 conversion rates and CH4 selectivities of the incorporated catalyst.
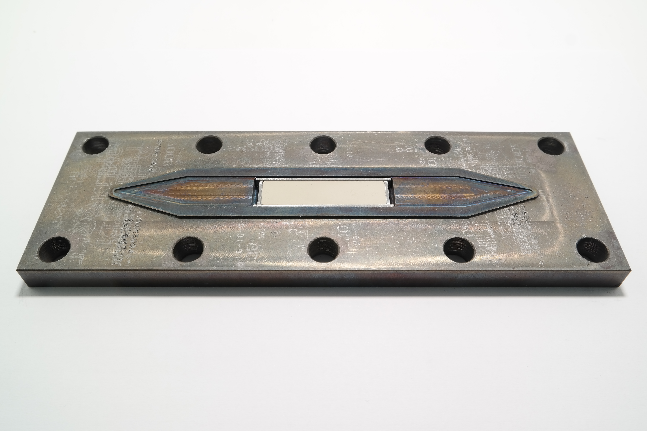