Services of the professorship
The Professorship Virtual Production Engineering is happy to support you in the analysis of your forming processes in the field of sheet metal and solid forming by means of various simulation systems. These can be supplemented by experimental investigations in our own test laboratory.
Are you interested in a cooperation? Then get in touch with us! Because for every practical problem there is a virtual solution.
Finite element analysis
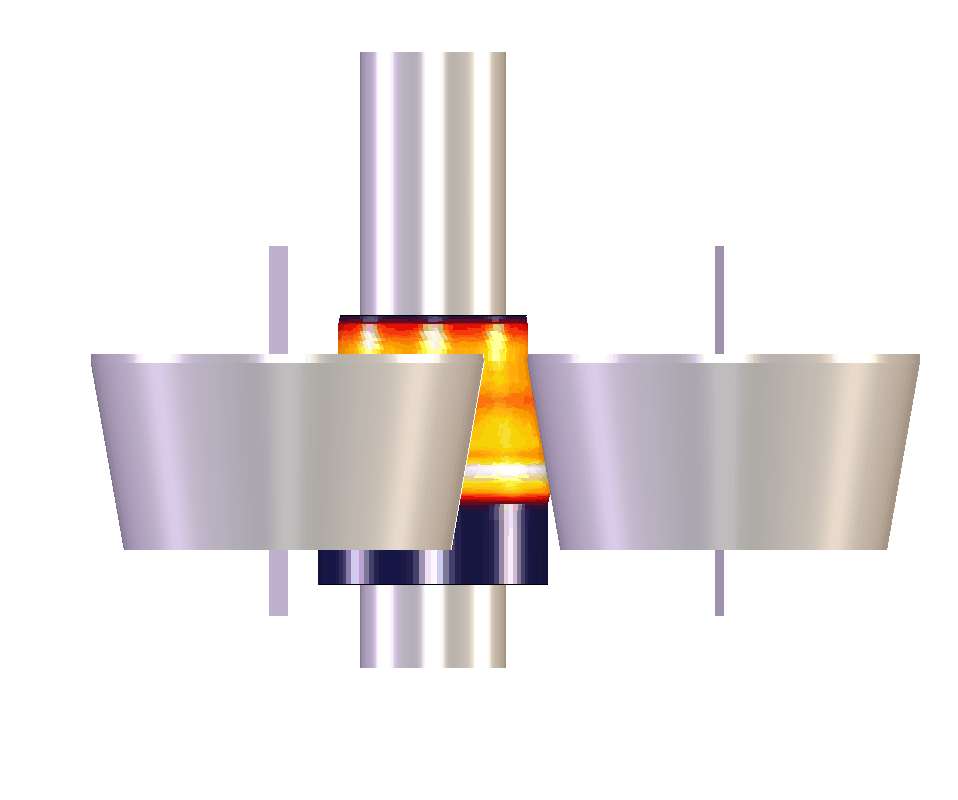
With the help of different FEM programs available at our professorship, we are able to map a wide range of forming manufacturing processes in the simulation. Specialized tools are available for sheet metal forming as well as for bulk metal forming. This enables us to identify any problems that may arise in the early planning phase, calculate required process forces and evaluate your processes based on the required performance parameters.
Process design and optimization
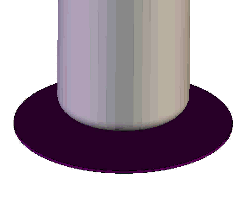
Even for components already in production, it is possible to use simulation to identify problems and, if necessary, optimize the existing processes. Especially for small and medium-sized companies, a cooperation with us offers the possibility to benefit from simulation techniques without having to acquire costly hardware, software and the corresponding specialists themselves. In our own test field and in cooperation with other professorships, we also have the possibility to carry out problem-related basic investigations, so that investigations on your production equipment can be reduced to a minimum, thus eliminating or minimizing downtime for production.
Stress tests and recording of flow curves
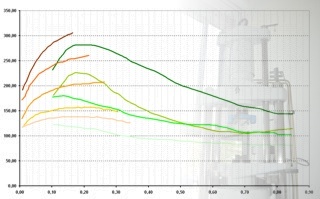
Material parameters are an essential basis for every simulation. We are able to record flow curves in compression tests (including cone compression tests, parallel compression tests). With our building material testing press, which has a nominal force of 2000kN, a wide range of static compression load tests or press-in tests are also possible. Thus, we can not only generate practical material data for us, but also perform various tests with similar loading conditions for you.
Analysis of deformation
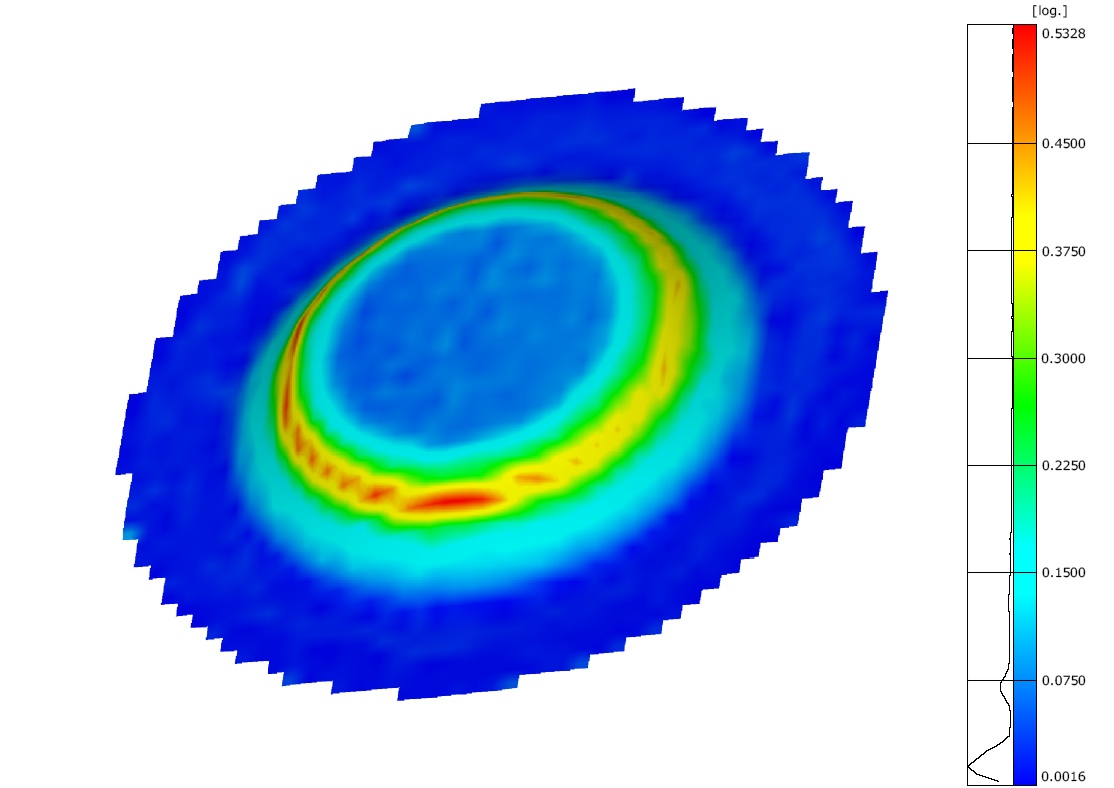
In addition to the material parameters, the key to a successful simulation is the verification in practice. Only if sufficiently accurate results have been obtained for a number of references, statements on the stress state in the component and subsequent statements in the planning process on the manufacturability of a component can be made. In order to measure the deformation condition of plane components, the professorship uses the optical 3D deformation analysis system ARGUS from the company GOM. If you are a manufacturer of components that need to be analyzed to know the forming degrees or to make a simulation comparison on the anlyses, we will be glad to help you.