Fields of Research
- the research and development of adapted carbon precursors in terms of porosity and processability
- the LPI process (Liquid Polymer Infiltration) for the development of high-temperature resistant C/C-SiC or C/C-SiCN composites
- the LSI process (Liquid Silicon Infiltration) or field-assisted siliconization (FAST-LSI) to provide high-temperature resistant C/C-SiC composites,
- mass production of C/C-SiC composites by injection molding as a shaping step
- fiber/matrix interface adaptation by means of CVD coating for SiCf/SiC composites
- the further processing of CMCs to hybrid components
- the joining of CMCs the characterization of CMCs (e.g. microstructure, phase analysis by Raman microscopy, damping, mechanical testing in SEM).
Metal matrix composites (MMCs) are metals and alloys that are reinforced with ceramic reinforcing components. This reinforcement is carried out with the aim of improving mechanical properties, such as Youngs modulus, strength, yield strength, or the wear resistance of the material. Particle-reinforced aluminum matrix composites have been developed within SFB692. MMCs can be produced by powder or melt metallurgy. Within the focus of the group is on the powder metallurgical process route by mechanical alloying in high energy ball mills and consolidation by field assisted sintering (FAST/SPS). The basis is the development of particle-reinforced powders (composite powders), which are investigated for additive manufacturing processes as well for foam generation in addition to the classical processing methods
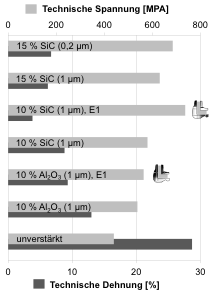
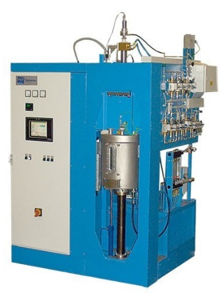
Funded by :
The CMC group of the professorship has been conducting research in the field of carbon fiber reinforced carbon composites (C/C) with subsequent siliconization (C/C-SiC) for many years. These materials have excellent chemical, thermal and mechanical properties. A major focus is the microstructure correlated research of different manufacturing methods and process variations in the states CFRP, C/C and C/C-SiC.
The Group of Composites and Material Compounds deals specifically with:
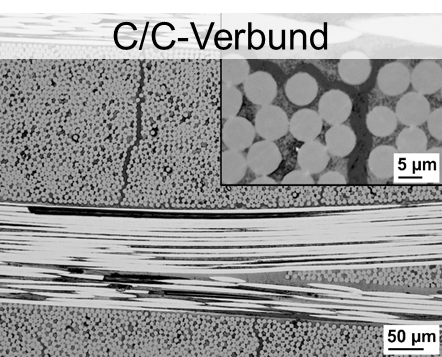
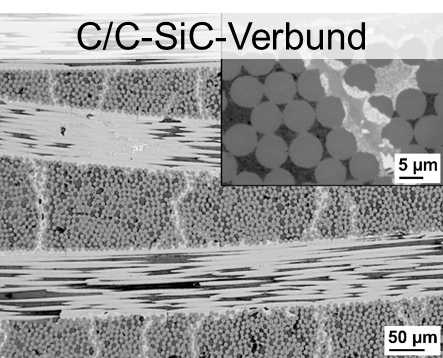
Contact Person: Dr.-Ing. Maik Trautmann, E-Mail: maik.trautmann@…
By chemical vapour deposition (CVD) and physical vapour deposition (PVD) techniques, thin layers of different materials can be fabricated. Our research in this area focuses on the coating of wires, single fibers and rovings as well as the development of a continuous CVD coating process for reinforcement components. Through such fibre coatings, it is possible to make specific adjustments in the fibre / matrix interface of composite materials (interface engineering) or to generate additional functionalization of the fibres (sensor or actuator).
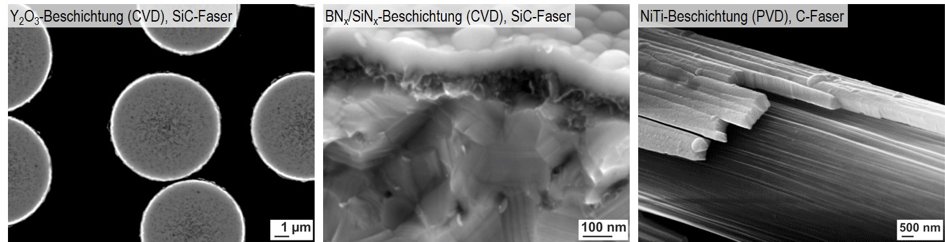
Contact Person: Dr.-Ing. Maik Trautmann, E-Mail: maik.trautmann@…
To qualitatively secure the functionality of novel composites and material compounds, the development of intrinsic condition monitoring systems is indispensable. For example, Structural Health Monitoring (SHM) measures allowable mechanical stresses within fibre-reinforced plastics. Film-based thin-film sensors and functionalized carbon single fibers offer the possibility of designing artifact-free sensor systems for fiber-reinforced plastics. Sensory active layer systems (NiC and NiTi), which are deposited by thin-film processes, are being researched. The aim is to achieve a higher sensitivity compared to commercially available strain sensors and a spatially resolved measurement.
Another focus is the integration of NiTi wires into hybrid laminates that can act as strain sensors or actuators.
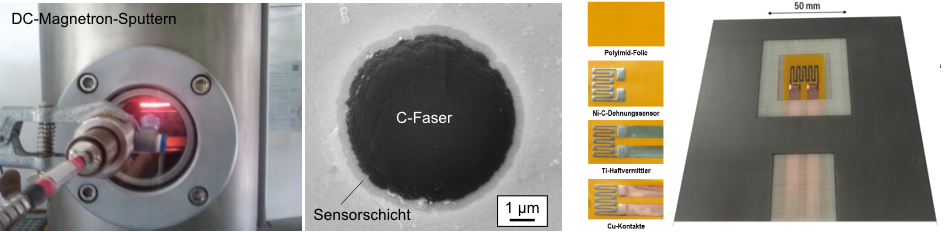
Contact Person: Dr.-Ing. Maik Trautmann, E-Mail: maik.trautmann@…
Hybrid laminates consisting of layers of light metals and fibre-reinforced plastics can cover a broad property profile by varying the materials as well as the number, thickness and orientation of the fibre-reinforced plastic. The thermoplastic matrix enables efficient and cost-effective production as well as good formability and recyclability. By integrating additional sensors (moisture, elongation), hybrid laminates can be functionalized excellently.
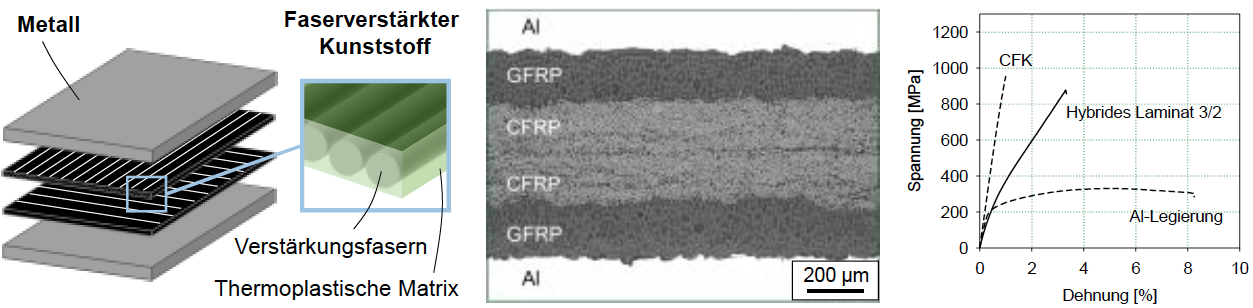
Contact Person: Dr.-Ing. Maik Trautmann, E-Mail: maik.trautmann@…
Metal/plastic compounds have great potential for industrial applications. Such material compoounds combine low density and the versatile processability of plastic with the high stiffness and strength of metal. The realization of such compounds requires joining solutions that are suitable for both the material and the application. The focus of the research work is on the production of suitable surfaces in order to utilize the various adhesion mechanisms, as well as the investigation of transition structures that influence the property gradient between metal and plastic.
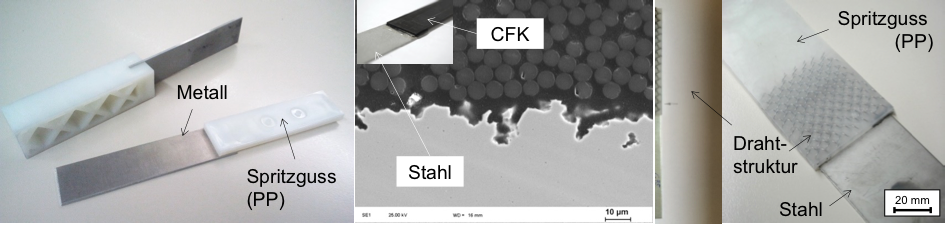
Sponsored by:
Contact Person: Dr.-Ing. Maik Trautmann, E-Mail: maik.trautmann@…
- The production of reliable soldered joints for power electronics in regenerative energy systems.
- The investigation of the wetting and flow behavior of brazing alloys.
- The influence of the brazing atmosphere on the fatigue life of brazed joints.
- Ultrasonic assisted resistance brazing processes.
- The active brazing of metal-ceramic compounds.
- Fe-base brazing fillers with improved corrosion resistance for use in drinking water-contacted components.
- Co-base brazing fillers for high-temperature brazing of high-strength, thermally heavily loaded components.
- Low-melting Al base brazing fillers for the production of aluminum-steel mixed compounds.
- Heat treatment strategies to improve the corrosion resistance of brazed plate heat exchangers.
- Arc brazing processes for the production of aluminum-steel mixed compounds.
- Furnace brazing processes (inert gas and vacuum).
- Ultrasonic assisted resistance brazing processes.
- Induction brazing processes.
Brazing and soldering make it possible to produce a large number of connections within complex assemblies in one process step. Our research topics range from soldered joints in electrical engineering to high-strength and temperature-resistant brazed joints of stainless steels. In particular, the Group of Composites and Material Compounds deals with:
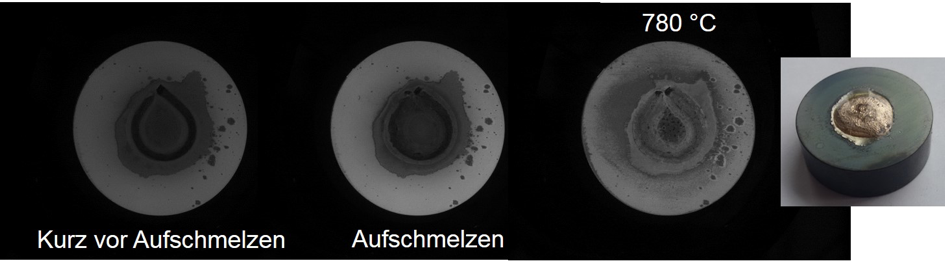
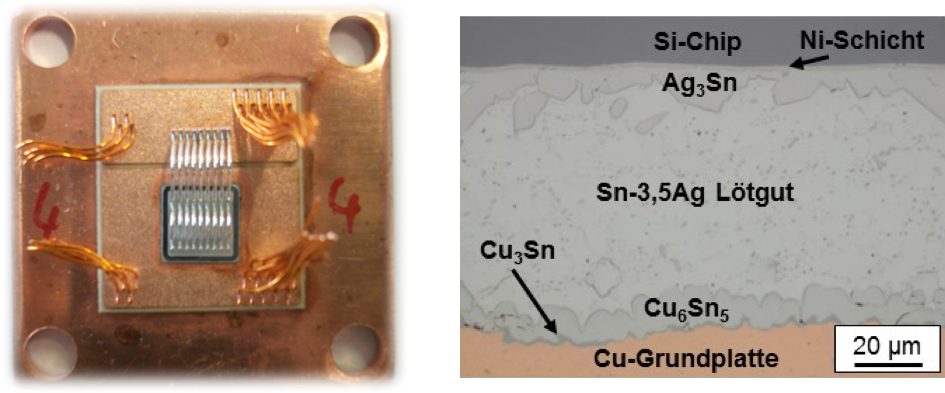
Sponsored by:
Contact Person: Dr.-Ing. Susann Hausner, E-Mail: susann.hausner@…
The continuous development of brazing processes also requires continuous development and modification of brazing fillers. Here are pursued a variety of goals. The Group of Composites and Material Compounds deals with the development and modification of:
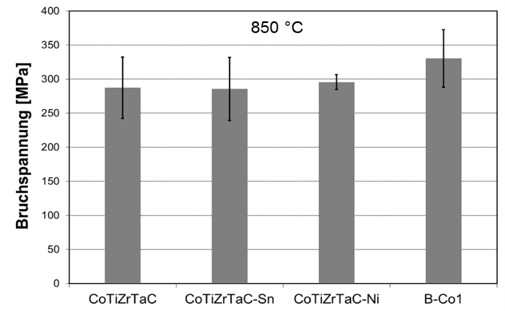
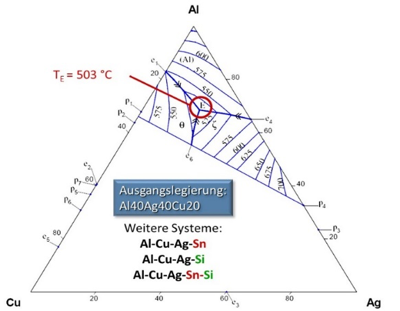
Quelle: Effenberg, G.; Ilyenko, S.: Light Metal Systems. Part 1: Ag-Al-Cu (Silver – Aluminium – Copper). Landolt-Börnstein, Volume 11A1 (2004), pp. 1-7.
Sponsored by:
Contact Person: Dr.-Ing. Susann Hausner, E-Mail: susann.hausner@…
To produce reliable brazed joints, accurate process control is essential. The further development and monitoring of brazing processes contributes significantly to improving the properties of brazed joints. The Group of Composites and Material Compounds deals with the development and optimization of:
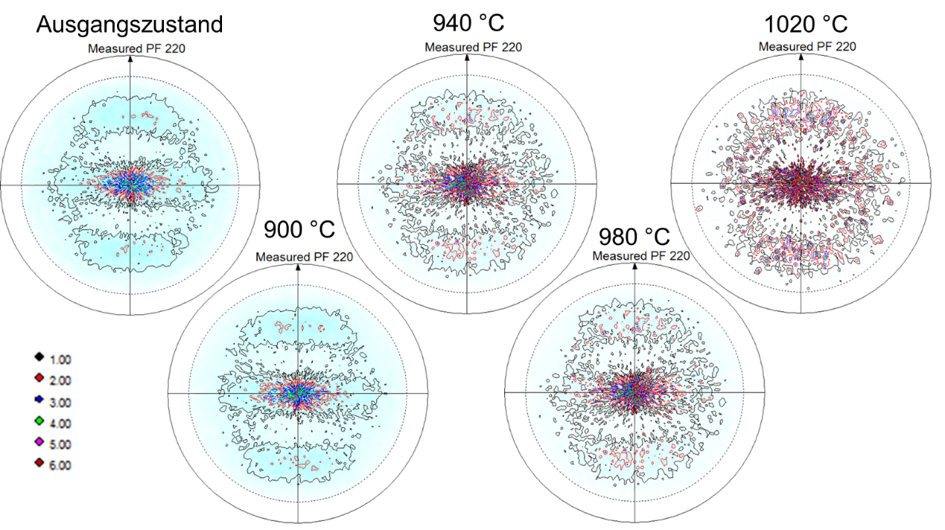
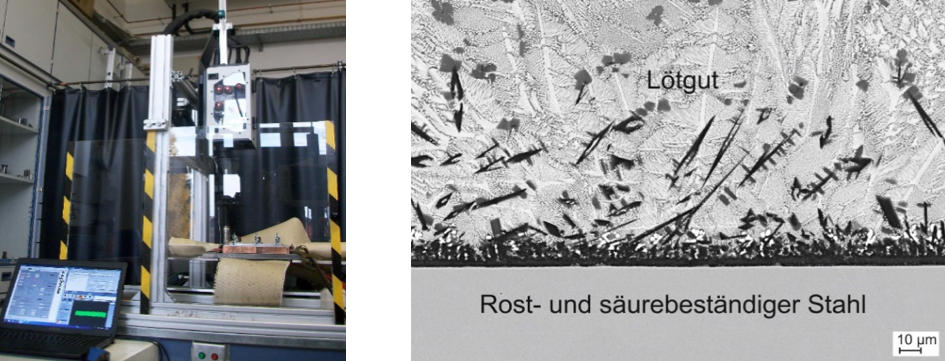
Sponsored by:
Contact Person: Dr.-Ing. Susann Hausner, E-Mail: susann.hausner@…
- metallic and non-metallic similar or dissimilar material compounds realized by friction stir welding with and without ultrasound enhancement (USE-FSW)
- local near-surface gradation of metallic and non-metallic materials by friction stir processing (FSP)
- generative realized metallic and non-metallic structures by friction stir build-up welding
Nanoparticles exhibit a reduced melting and sintering temperature compared to the corresponding bulk material. After melting or sintering of the nanoparticles, the material behaves like the bulk material. Therefore, high-strength and temperature-resistant joints can be produced at low temperatures, which is of big interest for various joining tasks. The Group of Composites and Material Compounds focuses in particular on the joining of metallic and polymeric substrates using Ag and Ni nanoparticles.
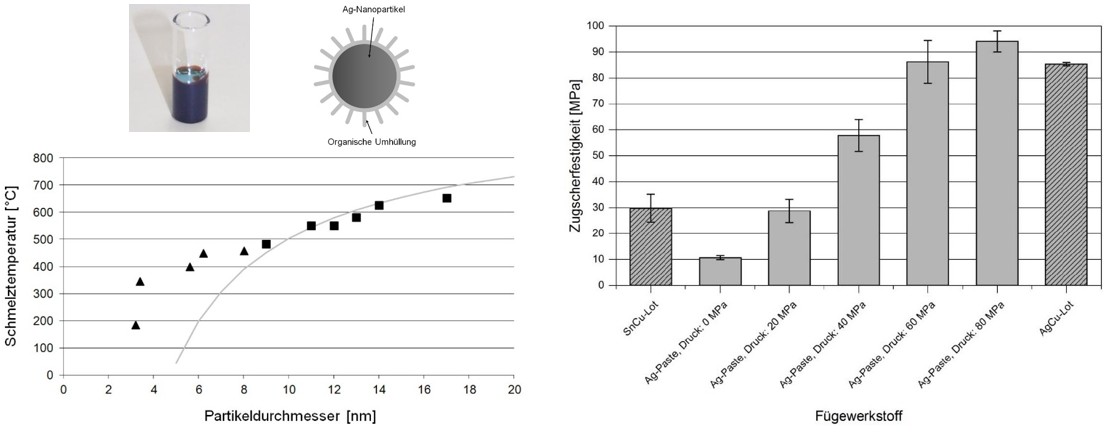
Another direction in which nanojoining is being developed is the use of nickel nanoparticles for structural joining solutions. The high-metal content pastes produced from these particles can be used, for example, to join nickel superalloys and steels.
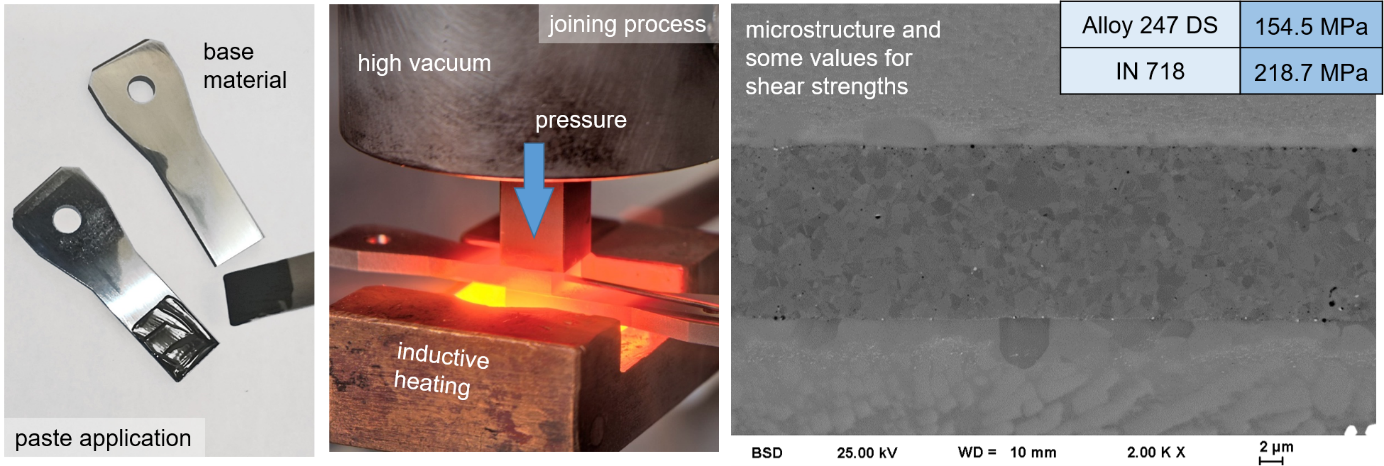
Contact Person: Dr.-Ing. Susann Hausner, E-Mail: susann.hausner@…
Friction Stir Welding (FSW) is an innovative pressure welding process for the realization of similar and dissimilar material compounds. In this process a rotating tool with a deducted probe at its head is applied on two joining partners with a defined welding force and then moved along the joint geometry. This solid-state joining process, regulated by the introduced frictional heat, results in a firmly bonded material compound.
The Group of composites and material compounds works in the department of low-heat joining processes on the realization and optimization of:
Contact Person: Dr.-Ing. Andreas Gester, E-Mail: andreas.gester@…
Ultrasonic Metal Welding (USMW) is an innovative process for joining metals that is mainly used in the automotive and electronics industries. In this process, the metal parts to be joined are subjected to a combination of static pressure and high-frequency ultrasonic vibrations. These vibrations create a relative motion at the contact surfaces of the joining partners, removing contaminants and achieving a high degree of surface proximity. The resulting joints show very high strengths and the method is able to join various metals, including these that are considered difficult or impossible to weld. The process is highly energy-efficient, requires no filler materials or shielding gases, and allows for joining within a very short time (welding times from 10 ms to 2 s). Another advantage of USMW is the operation below the melting temperature of the materials, i.e., in the solid phase, which largely avoids undesirable thermal effects such as the formation of brittle intermetallic phases. The following excitation directions are investigated at the department:
Contact Person: Dr.-Ing. Andreas Gester, E-Mail: andreas.gester@…
- Wear-resistant Fe-based alloys with high carbide contents
- High impact and abrasion resistant Fe-based alloys for wear protection layers
- Carbide-reinforced Fe base alloys with good corrosion resistance
For the wear protection of systems and components, surface coatings by thermal spraying or cladding are used. The development of new alloys opens up new fields of application. For this purpose, a laboratory arc furnace and a melt atomization plant for powder production are available. The Group of Composites and Material Compounds deals with the development and optimization:
Additionally, the research of the metallurgy group focuses on the properties and microstructure of high entropy alloys (HEA). Based on the well-investigated system CoCrFeNi, the influence of the alloying element Al as well as of elements from side group IV and V is considered. The samples are produced on a laboratory scale by melting pure elements in an electric arc furnace. This leads to a very homogeneous distribution of the alloying elements within the samples. The subsequent correlation between the microstructure and the melting behavior offers a comprehensive understanding on the properties of these materials. The described alloy development is part of the junior research group HEA SurfProtect. br>
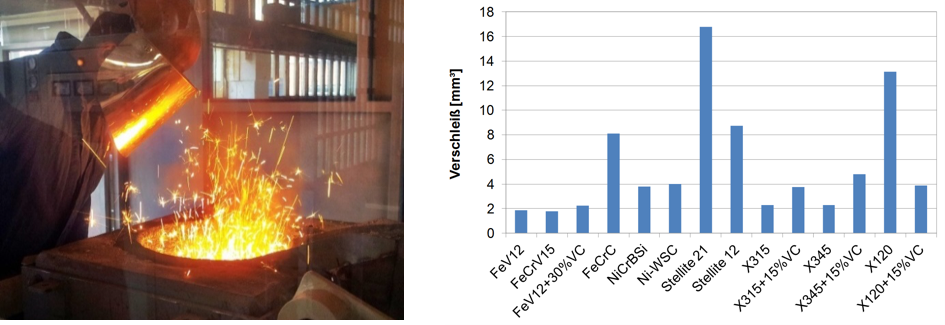
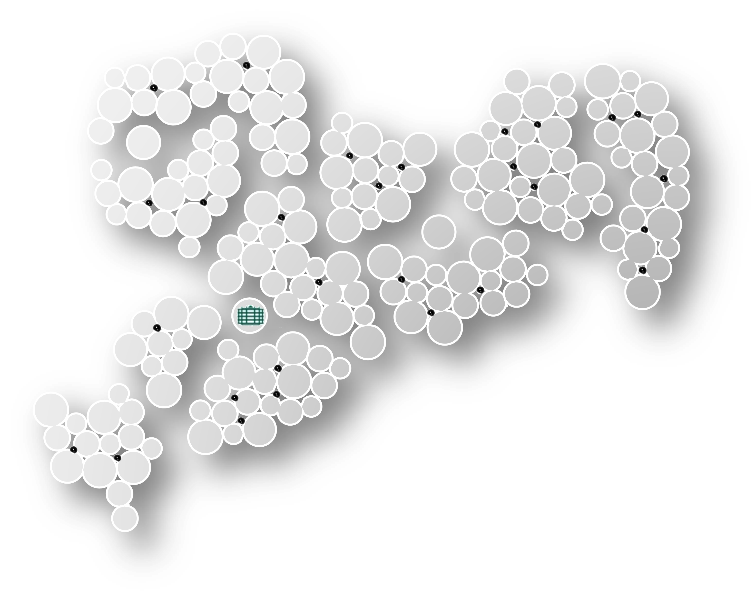
Sponsored by:
Contact Person: Dr.-Ing. Susann Hausner, E-Mail: susann.hausner@…
- High resolution microstructure analysis
- materialography
- failure and damage analysis
- Various analysis methods
For more information about our characterization methods, see Services.
Ansprechpartner: M. Sc. Andreas Gester, E-Mail: andreas.gester@…