Projekte im Bereich der Grundlagenforschung
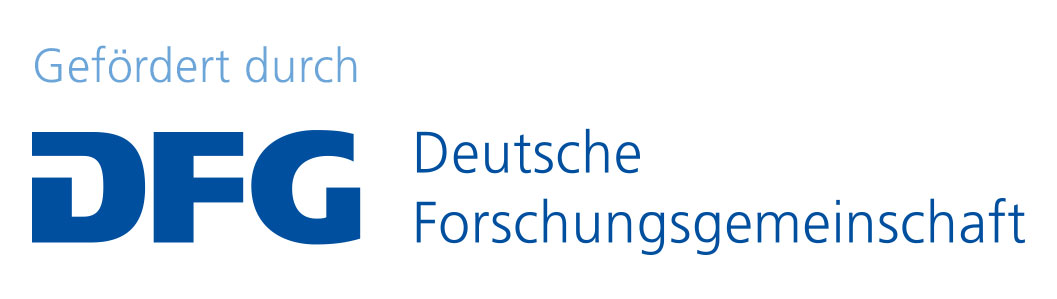
Kapazitätsorientierte Materialbewirtschaftung (KORMA): Bewertung und Erweiterung
Dauer: 36 Monate
Themen: Fertigungssteuerung, Auftragserzeugung, Auftragsfreigabe, Kapazitätssteuerung, Simulation
Überblick und Projektziele
Um die Produktivität weiter zu erhöhen, müssen Materialfluss und Kapazität besser mit der Nachfrage synchronisiert werden. Diese Synchronisierung wird durch die allgemeine Entwicklung zu kundenspezifischeren Produkten erschwert, da diese einen signifikant höheren Organisationsaufwand als die bisher vorherrschenden Make-to-Stock-Produkte (MTS) besitzen. Zusätzlich wird die Synchronisierung durch volatile Märkte und eingeschränkte Lieferketten gestört. Das Ziel der Fertigungssteuerung liegt in eben dieser Synchronisierung, wobei die vier Aufgaben Auftragserzeugung, Auftragsfreigabe, Sequenzierung und Kapazitätssteuerung den Kern bilden. Die Literatur konzentriert sich in der Regel auf eine dieser Aufgaben sowie auf die dafür verwendeten Methoden, die entweder für Make-to-Order (MTO) oder MTS geeignet sind.
Ein passendes Fertigungssteuerungssystem, das verschiedene dieser Aufgaben integriert und für hybride MTO/MTS-Kontexte ausgelegt ist, stellt die Kapazitätsorientierte Materialbewirtschaftung (KORMA) dar. KORMA ist jedoch nicht abschließend definiert, bisher nicht unter dem Aspekt der Leistung bewertet und es vernachlässigt die Kapazitätssteuerung. Dieses Projekt hat folglich drei Ziele: zu bewerten, wie die KORMA-Prinzipien die Fertigungssteuerung verbessern können, KORMA zu operationalisieren und KORMA weiter zu entwickeln.
Inhalte und Methoden
Im Projekt erfolgt die Bewertung der Leistungsfähigkeit des Reorder-Points anhand verschiedener Methoden zur Bestimmung von Sicherheitsbestandniveaus für Fertigungsaufträge unter Berücksichtigung von KORMA und der Integration von Synchro MRP. Das Projekt integriert Work-in-Process-Regulierungs- und Workload-Balancing-Release-Methoden in KORMA und bewertet deren Auswirkungen. Zudem wird die auf MTS fokussierte KORMA-Sequenzierung um eine für MTO geeignete Sequenzierung erweitert. Zur Weiterentwicklung von KORMA werden die Auswirkungen der Kapazitätssteuerung in KORMA bewertet. In der Projektbearbeitung erfolgt die Verwendung eines multimethodischen Ansatzes, bestehend aus Diskreter Ereignissimulation sowie konzeptionell-empirischer Forschung in Form eines iterativen Theorie-Praxis-Forschungszyklus. Das Projekt entwickelt ein Reorder-Point-System für die Auftragsgenerierung, das frühzeitige Freigaben bei nicht ausgelasteter Kapazität ermöglicht und gleichzeitig ein Aufstauen der Aufträge vermeidet. Es führt eine Freigabemethode ein, die von tatsächlichen Kundenanforderungen bestimmt wird und für MTS- und MTO-Produkte geeignet ist. Das Projekt führt hierbei ein neues Sequenzierungsverfahren (Probability Scheduling) ein, das sich auf den Nettobedarf und die Bedarfsrate statt auf Wiederbeschaffungszeiten konzentriert und für hybride MTO/MTS-Kontexte geeignet ist. Durch die gleichzeitige Bewertung der Leistung aller vier Fertigungssteuerungsaufgaben bietet dieses Projekt zudem wichtige Leitlinien für das zukünftige Design von Fertigungssteuerungssystemen.