Studien-, Projekt- und Abschlussarbeiten
In folgenden Arbeitsfeldern werden aktuell 18 studentische Arbeiten angeboten:
Passivierungsverhalten bei der plasmaelektrolytischen Oxidation (PEO) eines unlegierten Stahls
Aufgrund ihrer hohen Festigkeit, ihres hohen E-Moduls, der guten Verarbeitbarkeit und des vergleichsweise geringen Materialpreises besitzen Stähle ein hohes Anwendungspotenzial als metallischer Verbundpartner in Metall-Kunststoff-Verbunden. Die Verbundfestigkeit wird durch Oberflächenbehandlung des Metalls gewährleistet. Zudem müssen insbesondere unlegierte Stähle vor Korrosion geschützt werden, da Feuchtigkeit durch das Polymer an die Metall-Kunststoff-Grenzfläche diffundieren kann. Plasmaelektrolytisch erzeugte Oxidschichten eignen sich als Korrosionsbarriere und ermöglichen sowohl die chemische Anbindung als auch die mechanische Verklammerung von Polymeren. Im Rahmen eigener Vorarbeiten zur PEO eines unlegierten Stahls in einem literaturbekannten Silikat-Phosphat-Elektrolyt zeigte sich jedoch, dass die Zündspannung erst durch die Vorgabe sehr hoher Pulsstromamplituden erreicht wird. Daraus folgen sehr energieintensive Funkenentladungen und ein hoher Energieverbrauch. Für die Herstellung dünner, ausreichend schadenstoleranter PEO-Schichten in einem energieeffizienten Prozess ist eine verbesserte Passivierung des Stahlsubstrats grundlegend erforderlich.
DIm Rahmen der Studienarbeit wird deshalb die Beeinflussung des Passivierungsverhaltens eines unlegierten Stahls durch Zugabe unterschiedlicher Elektrolytkomponenten (z.B. Silikat, Aluminat, Phosphat) und ggf. Anpassung des pH-Werts mithilfe von Modellversuchen im Becherglas erforscht. Hierzu werden komplexe Spannungsrampen vorgegeben, die sowohl den Spannungsanstieg zu Beginn des Prozesses als auch die Beständigkeit von Passivschichten bei abnehmender Prozessspannung sowie ggf. eine Repassivierung simulieren sollen. Das wiederholte Durchfahren dieser Spannungsbereiche ist bei gepulster Stromführung von großer Bedeutung. Die nach dem Rampenversuch vorliegenden Oberflächen werden zudem u.a. mittels Rasterelektronenmikroskopie hinsichtlich der Eigenschaften (Dicke, Mikrostruktur, chemische Zusammensetzung) der Oberfläche bzw. Passivschicht untersucht
Durchzuführende Arbeiten:
- Literaturrecherche zum Stand der Forschung, unter besonderer Beachtung der PEO von Stählen (Prozessparameter und erzielbare Schichteigenschaften) und der anodischen Passivierung von Metallen
- Einbeziehung der bereits am Institut vorhandenen Kenntnisse zur Passivierung während der PEO
- Durchführung von Beschichtungsversuchen an der Laboranlage des Instituts für Werkstoffwissenschaft und Werkstofftechnik
- Planung und Durchführung experimenteller Arbeiten:
- Probennahme und -vorbereitung
- Dokumentation der Experimente unter Berücksichtigung der statistischen Absicherung
- Zerstörungsfreie Bestimmung der Schichtdicke
- licht- und elektronenmikroskopische Untersuchungen (inkl. Präparation)
- Auswertung und Diskussion der Ergebnisse im Vergleich zu dem internationalen Schrifttum
- Zusammenfassung und Schlussfolgerungen sowie Ausblick
Wissenschaftlicher Betreuer:
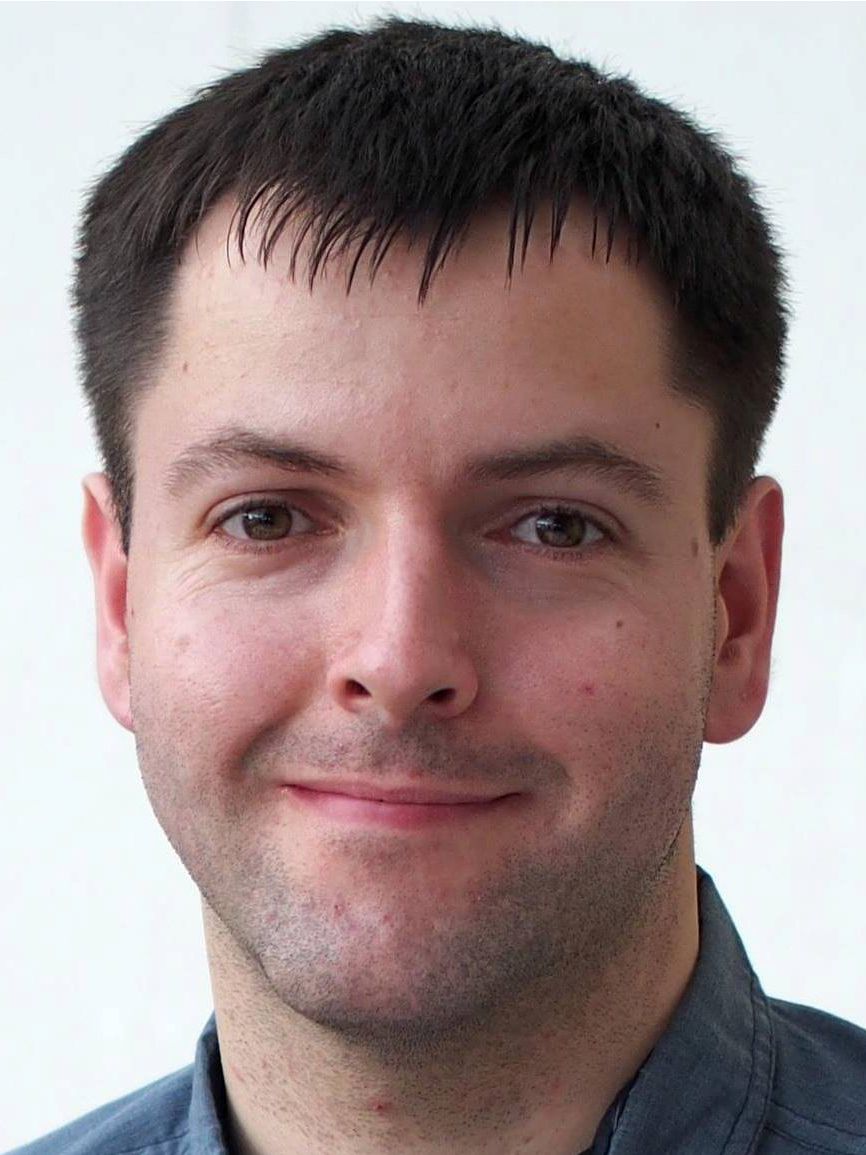
Plasmaelektrolytische Oxidation reibrührgeschweißter Aluminium/Stahl-Verbunde
Plasma electrolytic oxidation of friction stir welded aluminium/steel compounds
Die plasmaelektrolytische Oxidation (PEO) ist ein innovatives Verfahren zur Erzeugung anorganischer, oftmals keramischer Schutz- und Funktionsschichten auf metallischen Werkstoffen. Hierbei wird das zu behandelnde Bauteil innerhalb eines geeigneten wässrigen Elektrolyten bei hohen Prozessspannungen als alternierende Anode geschalten. Dies führt vorzugsweise innerhalb der anodischen Teilperiode des elektrischen Regimes zur Initiierung plasmaelektrolytischer Funkentladungen welche ausgehend vom Elektrolyt in das Substrat schlagen und hierbei eine Reaktionsschicht erzeugen.

Fotostrecke eines PEO-Prozesses (links), lichtmikroskopische Aufnahme eines FSW-Werkstoffverbundes (rechts)
Im Zuge der Arbeit soll der PEO-Prozess durch systematische Anpassung des Elektrolyten auf reibrührgeschweißte (FSW, friction sir welding) Werkstoffverbünde aus Al-6061 und Fe-DC04 übertragen werden. Dies geschieht vordergründig durch elektrochemische Polarisationsversuche wobei auf bereits funktionierende Versuchsstände und erfolgreich abgeschlossene studentische Arbeiten aufgebaut werden kann.
Durchzuführende Tätigkeiten:
- Literaturrecherche
- Einarbeitung in den Umgang mit MATLAB
- Polarisationsversuche an elektrisch gekoppelten Al/Fe-Anodenpaarungen
- Durchführung und Auswertung von PEO-Versuche auf Al/Fr-FSW-Verbünden
- Materialographische Präparation und Analytik der generierten Schichten
Voraussetzungen:
- gute bis sehr gute Chemiekenntnisse
- experimentelles Geschick
- Fähigkeit zum interdisziplinären Arbeiten
- sorgfältige und selbstständige Arbeitsweise
Die Ausschreibung richtet sich an Studierende ingenieur- und naturwissenschaftlicher Fachrichtungen.
The announcement is aimed at students of engineering and natural science studies.
Die Arbeit kann als Studienarbeit, Bachelorarbeit oder research project absolviert werden. Der Arbeitsumfang wird dementsprechend angepasst. Der Beginn der praktischen Arbeit ist bedingt durch Baunahmen nicht vor Dezember 2020 möglich. Darüber hinaus richtet sich der Verlauf der experimentellen Tätigkeiten nach den stetig aktualisierten Corona-Auflagen.
Wissenschaftlicher Betreuer:
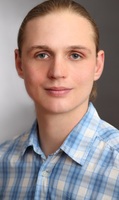
Einfluss kapazitiver Effekte auf die Lokalisierung der anodischen Schichtbildung
Die anodische Oxidation ist ein bewährtes oberflächentechnisches Verfahren zur Erzeugung korrosionsschützender und verschleißbeständiger Konversionsschichten auf Aluminiumlegierungen. Üblicherweise erfolgt die anodische Oxidation im Tauchverfahren, wobei der Konversionsprozess auf allen frei durch den Elektrolyten zugänglichen Oberflächen eines Bauteils stattfindet. Die Begrenzung des Prozesses auf ausgewählte Funktionsflächen ist konventionell nur durch aufwendiges Abdecken aller übrigen Flächen möglich. In vorangegangenen Untersuchungen wurde das Ziel verfolgt, die anodische Oxidbildung unter Verwendung eines Elektrolytfreistrahls auf einen kleinen Oberflächenbereich zu lokalisieren. Ein wesentliches Hindernis für das lokalisierte Schichtwachstum stellt das verstärkte Abfließen des elektrischen Stromes in radialer Richtung mit zunehmender Dicke der elektrisch isolierenden Oxidschicht im Zentrum der benetzten Fläche dar. Erste Voruntersuchungen belegen, dass kurze Spannungspulse im Millisekunden-Bereich geeignet sind, um eine erhöhte Lokalisierung zu erzielen. Es wird davon ausgegangen, dass die Doppelschichtkapazität am Elektrolyt-Oxid-Interface unter diesen Bedingungen zuerst im Zentrum überwunden und ein weiteres Schichtwachstum initiiert wird. Die Doppelschichtkapazität nimmt stark mit abnehmender Sperrschichtdicke zu.
Im Rahmen der vorliegenden Arbeit soll erforscht werden, inwiefern dieser Effekt nutzbar ist, um die Lokalisierung der Schichtbildung zu verstärken. Dazu wird eine „punktförmige“ Kathode in einem Elektrolytbad in geringem Abstand gegenüber der Anode (Al-Legierung EN AW-7075) platziert, wobei ein großes Flächenverhältnis Anode/Kathode vorliegt. Bei gleicher mittlerer anodischer Stromdichte (also vergleichbarer Oxidbildungsrate) werden unterschiedliche Sperrschichtdicken durch unterschiedliche Prozessspannungen realisiert, die durch Variation von Art und Konzentration der Säureanionen in einem weiten Bereich einstellbar sind. Die Lokalisierung der Schichtbildung wird anhand der Schichtdickenverteilung am metallografisch zielpräparierten Querschnitt mithilfe von Licht- und Rasterelektronenmikroskopie bewertet. In Ergänzung zu den Lokalisierungsversuchen mit Drahtelektrode erfolgt die Quantifizierung der Doppelschichtkapazität für die verwendeten Elektrolyte in einem separaten Versuchsaufbau während der flächigen anodischen Oxidation unter Gleichstrombedingungen durch überlagerte elektrochemische Impedanzspektroskopie (EIS).
Durchzuführende Arbeiten:
- Literaturrecherche zum Stand der Forschung, unter besonderer Beachtung der lokal begrenzten anodischen Oxidation und der elektrochemischen Vorgänge am Oxid-Elektrolyt-Interface während der anodischen Oxidation
- Einbeziehung der bereits am Institut vorhandenen Kenntnisse zur lokal begrenzten anodischen Oxidation und prozessbegleitenden EIS-Messungen
- Planung und Durchführung experimenteller Arbeiten:
- Probennahme und -vorbereitung
- lokal begrenzte anodische Oxidation mittels „Punktelektrode“ unter Verwendung von Pulsstrom
- EIS-Messungen während der anodischen Oxidation
- Dokumentation der Experimente unter Berücksichtigung der statistischen Absicherung
- licht- und rasterelektronenmikroskopische Untersuchungen (inkl. Präparation)
- Auswertung und Diskussion der Ergebnisse im Vergleich zum internationalen Schrifttum
- Zusammenfassung und Schlussfolgerungen sowie Ausblick
Wissenschaftlicher Betreuer:
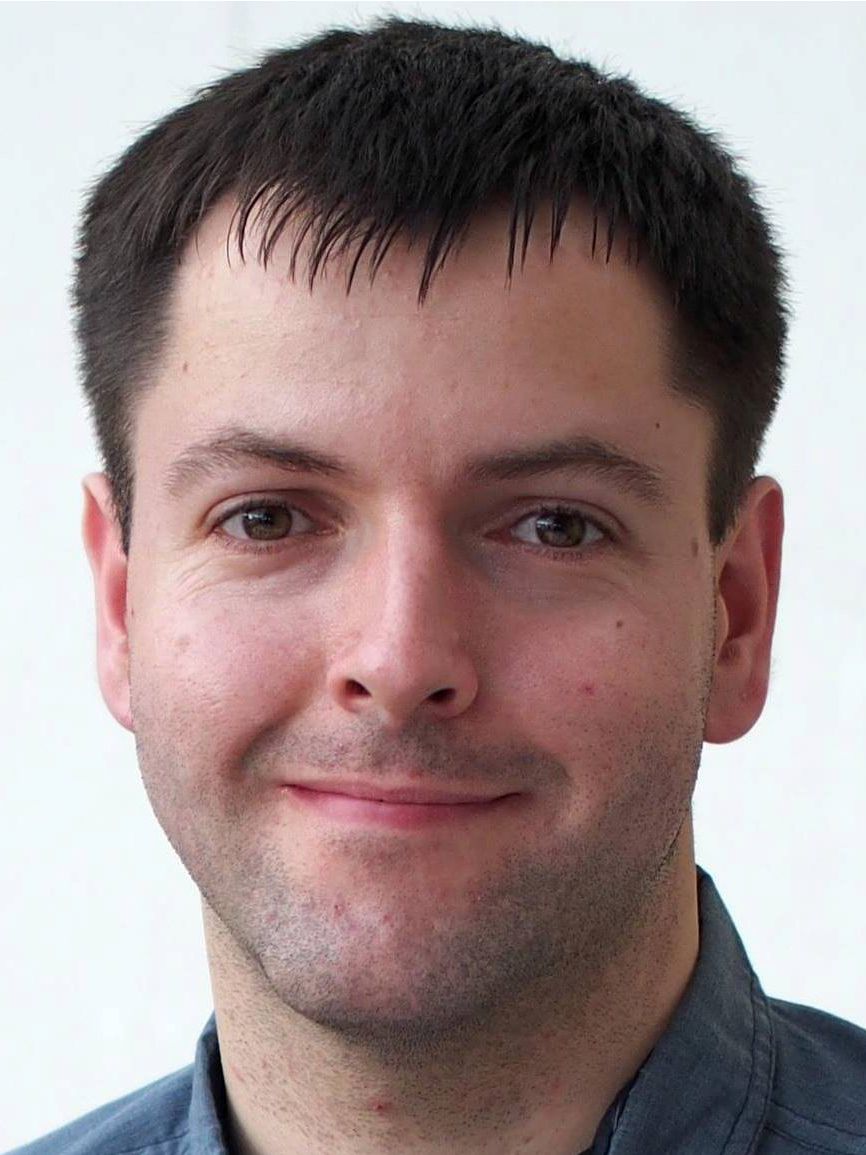
Vorbehandlung von Aluminiumsubstraten durch anodisches Oxidieren für das direkte Andrucken von Kunstoffen im additiven Fused Filament Fabrication Verfahren
Hybride Werkstoffverbunde aus Metallen und Kunststoffen werden für bewegte Komponenten eingesetzt, um die Bauteilmasse zu minimieren. Die Herstellung solcher Verbunde ist aufgrund der hohen Werkzeugkosten jedoch nur für große Stückzahlen wirtschaftlich darstellbar. Für kleine Chargen stehen daher die additiven Herstellungsverfahren im Fokus. Dazu zählt das Fused Filament Fabrication (FFF) Verfahren, bei dem ein vorkonfektioniertes Metallteil mit Kunststoff bedruckt wird. Für die mechanische Belastbarkeit ist die Grenzschicht der Materialien, und somit die Oberflächenvorbehandlung des Metallgrundkörpers, von entscheidender Bedeutung. Diesbezüglich wurde bislang jedoch nur sehr wenig in der Fachliteratur publiziert. Beispielsweise stellt das anodische Oxidieren eine potentiell geeignete Vorbehandlung für Aluminiumbauteile dar, da hiermit eine Oberflächenstrukturierung des Metalls in Form von nanoskaligen Poren erfolgt, die die mechanische Verklammerung des aufgedruckten Kunststoffs ermöglichen könnten.
Bei der Einstellung der Porengröße einer anodischen Oxidschicht ist begrifflich zu unterscheiden zwischen dem Durchmesser der hexagonalen Porenzelle und dem Durchmesser der Pore. Der Zellendurchmesser nimmt weitestgehend unabhängig von der Elektrolytzusammensetzung etwa linear mit der Anodisierspannung zu, wobei der maximale Porendurchmesser dem Durchmesser des Innenkreises der hexagonalen Porenzelle entspricht. Tendenziell steigt auch der Porendurchmesser, der zu Beginn des selbstorganisierten Porenwachstums vorliegt, mit der Anodisierspannung. Je nach Abtragsrate durch chemische Rücklösung werden die Poren im weiteren Verlauf unterschiedlich schnell aufgeweitet. Sowohl die Abtragsrate als auch der Arbeitsbereich der Anodisierspannung hängen vor allem von Art und Konzentration der Säure sowie von der Temperatur ab. Zur Einstellung verschiedener Zellengrößen ohne aufwendige experimentelle Bestimmung geeigneter Arbeitsbereiche wird die anodische Oxidation bei moderater Stromdichte für unterschiedliche Konzentrationen von Schwefel-, Oxal- und Phosphorsäure durchgeführt. Die dafür notwendigen Prozessspannungen werden erwartungsgemäß zwischen etwa 10 V (Schwefelsäure) und 250 V (Phosphorsäure) liegen. Die Variation der Porenaufweitung erfolgt durch unterschiedliche Anodisierdauern sowie ggf. eine zusätzliche Auslagerung in schwefelsaurer Lösung. Die Bestimmung der Poren- und Zellengröße wird anhand hochaufgelöster, rasterelektronenmikroskopischer (REM) Oberflächenaufnahmen durchgeführt. Auf dieser Wissensbasis erfolgt die Herstellung anodischer Oxidschichten mit definierter Porengeometrie für die Erforschung des Eindringens von Kunststoffen in die Oxidporen während des 3D-Druckens. Aufgrund der einstellbaren Größe und Periodizität der Poren haben die strukturierten Oberflächen zudem einen Modellcharakter und ermöglichen eine übergeordnete Aussage darüber, welche Geometriemerkmale nanoskalige Strukturen aufweisen dürfen, damit diese mit Kunststoff im FFF-Verfahren infiltrierbar sind. Diesbezüglich soll auch untersucht werden, wie sich der Chemismus des Kunststoffs – anhand typischer 3D-Druck-Kunststoffe wie Polymilchsäureester (PLA) und Polyamid – und die 3D-Druck-Parameter (Temperatur von Düse und Bauplattform, Druckgeschwindigkeit), auf die Infiltration der Poren auswirken. Die Eindringtiefe des Kunststoffs wird an Querschliffen untersucht, die mittels Rasterelektronenmikroskopie (REM) oder Rasterkraftmikroskopie (AFM) zu evaluieren sind.
Die Arbeit umfasst eine nationale und internationale Literaturrecherche zum Stand der Wissenschaft und Technik mit folgenden Schwerpunkten:
- Schichtbildungsmechanismus bei der anodischen Oxidation und Einflussgrößen auf die Strukturbildung
- Einfluss der chemischen Zusammensetzung des Elektrolyten und des diesbezüglichen Einbaus von (an)organischen Säurerestionen in die anodische Oxidschicht auf die Haftung zu verschiedenen Kunststoffen
- Auswahl von additiven Fertigungsparametern und von haftgebenden Oberflächenbehandlungen des Metallteils auf die Herstellbarkeit von Metall-Kunststoff-Bauteilen
Die Experimente umfassen die folgenden Aufgaben bzw. Themen:
- Planung und Durchführung der Anodisierexperimente zur Oberflächenvorbehandlung
- Probenpräparation und Begleitung der Schichtanalytik
- Kunststoff-3D-Druck auf den anodisch oxidierten Proben im FFF-Verfahren unter zielgerichteter Variation der FFF-Fertigungsparameter
- Charakterisierung der ausgebildeten Verbindungszone der Metall-Kunststoff-Bauteile in Abhängigkeit der Oberflächenvorbehandlung und der FFF-Fertigungsparameter durch Querschliffe und über Haftabzugsversuche mit begleitender Bruchflächenanalyse
- Dokumentation, Aufbereitung und Auswertung der Ergebnisse
Die Aufgabenstellung ist geeignet für folgende Formate: Studienarbeit, Bachelorarbeit, Praktikumsarbeit, Research Project oder ähnliches
.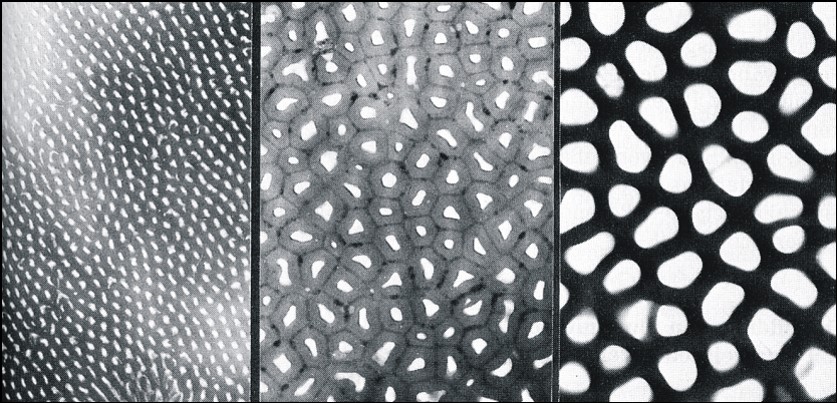
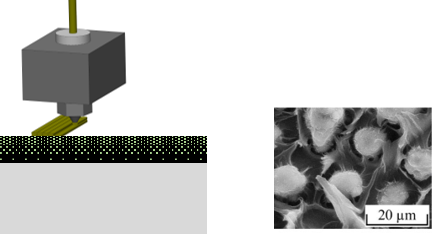
Elektronenmikroskopische Aufnahme einer anodischen Oxidschicht (links) sowie Schemata für das Andrucken von Kunststoff auf einem Metall mittels FFF (rechts).
Wissenschaftlicher Betreuer:
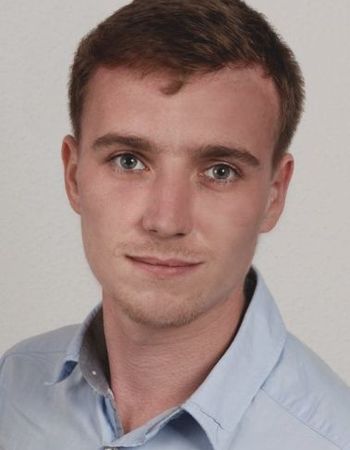
Elektrolyt- und Prozessdesign zur chemischen/galvanischen Abscheidung von REACh-konformen (Cyanid-freien) Au-Schichten
Die galvanische Vergoldung ist aufgrund der herausragenden chemischen Beständigkeit von Gold eine etablierte Methode, wenn es um die Sicherstellung langzeitstabiler elektrischer Kontaktierungen in mittleren und kleinen Lastbereichen geht. Der größte Teil galvanischer Feingoldabscheidungen für die Mikroelektronik erfolgt aus cyanidischen Bädern, da diese die nötige Langzeitstabilität aufweisen, die für die komfortable Anwendung der Elektrolyte im kommerziellen Einsatz benötigt wird. Der Bedarf an cyanidfreien Goldelektrolyten besteht schon lange: Der Umgang mit Cyaniden bezüglich Arbeits- und Umweltschutz ist jedoch mit hohen Risiken verbunden und Unternehmen sind dadurch gezwungen, einen erheblichen Mehraufwand an Bürokratie (Gefahrstoffmanagement) und Schutzmaßnahmen (Abluft, Abwasserbehandlung und Arbeitsschutz) auf sich zu nehmen. Aufgrund der Freisetzung von Cyanid in sauren Lösungen oder dem sogenannten „Underplating“ bei Verwendung von basischen Elektrolyten weisen cyanidische Goldelektrolyte deutliche Nachteile auf.
Ziel ist es, die chemische oder galvanische Abscheidung von Au-Schichten genauer zu betrachten und ein Elektrolyt- und Prozessdesign durchzuführen. Durch Variation von Elektrolyt- und Beschichtungsparametern wird ist es dabei möglich, die Schichtdicke- und eigenschaft zu beeinflussen. Eine mechanistische Betrachtung der unterschiedlichen Prozesse während der Abscheidung soll dazu einen vertieften Einblick in die Vorgänge der Au-Abscheidung liefern.
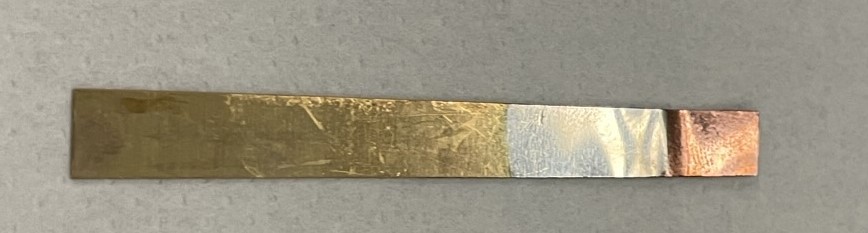
Im Bild: Chemisch abgeschiedene Au-Schicht
Durchzuführende Arbeiten:
- Literaturrecherche zum Stand von Forschung und Technik
- Einstellung eines Grundelektrolyten zur Abscheidung von Au-Schichten
- Planung, Durchführung und Dokumentation experimenteller Arbeiten
- Additivierung des Elektrolyten zur Optimierung der Abscheidebedingungen
- Prozessoptimierung & Verbesserung der Langzeitstabilität des Elektrolyten
- Schichtcharakterisierung (z.B. bzgl. Leitfähigkeit, Verschleiß und Korrosion)
- Auswertung und Diskussion der Ergebnisse im Vergleich zu dem internationalen Schrifttum
Voraussetzungen:
- Gute bis sehr gute chemische/elektrochemischen Kenntnisse
- Ev. Erfahrungen bzgl. Oberflächen und Beschichtungstechnik
- Experimentelles Geschick
- Fähigkeit zum interdisziplinären Arbeiten
- Sorgfältige und selbstständige Arbeitsweise
Wissenschaftlicher Betreuer:
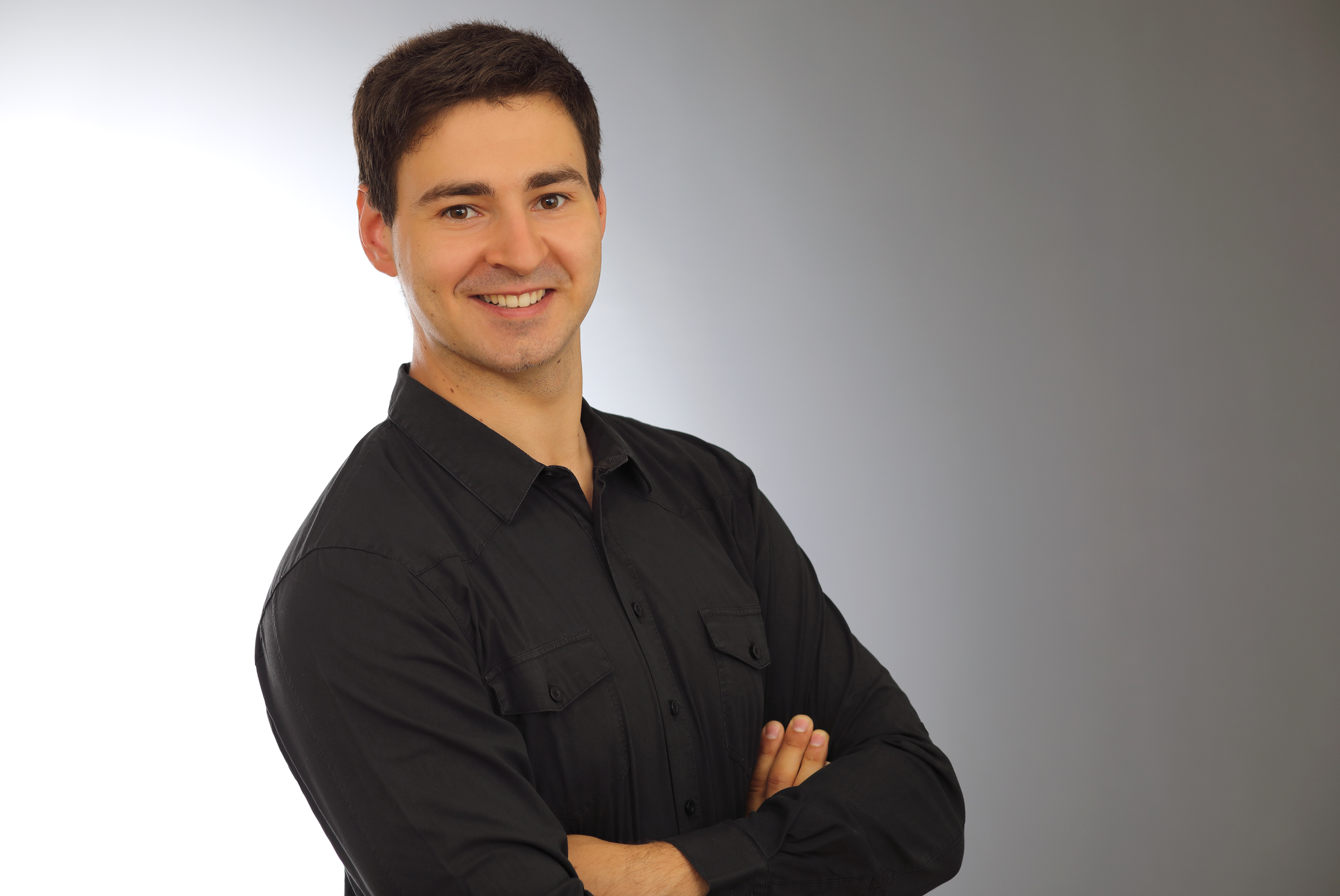
Elektrolyt- und Prozessdesign zur chemischen/galvanischen Abscheidung von magnetischen Fe-Co-Legierungsschichten zur Funktionalisierung von Kohlenstofffasern
Für den Leichtbau hochbeanspruchter Komponenten werden oft faserverstärkte Kunststoffe eingesetzt. In vielen üblichen Prozessen zur Bauteilherstellung besteht dabei das Problem, dass das Potential der Verstärkungsfasern nur teilweise genutzt werden kann, da die Fasern nicht gezielt mit dem im Bauteil wirkenden Kraftfluss ausgerichtet werden können. Durch galvanische Beschichtung der Fasern mit dünnen Fe-Co-Schichten werden diese um eine dauermagnetische Funktionalität ergänzt und können dadurch im Herstellprozess des Bauteils gezielt und lokal ausgerichtet werden. Die Schwierigkeit besteht allerdings in einer geeigneten Beschichtung, die ausreichend hohe magnetische Kräfte während des Verarbeitungsprozesses der Verbundwerkstoffe, etwa im Spritzgieß- oder Pressprozess, in der hochviskosen Polymermatrix zur Orientierung erlaubt und gleichzeitig fest genug an der Faser haftet.
Ziel ist es, die chemische/galvanische Abscheidung von Fe-Co-Legierungen genauer zu betrachten und ein Elektrolyt- und Prozessdesign durchzuführen, das sich auch für die Beschichtung von C-fasern eignet. Durch Variation von Elektrolyt- und Beschichtungsparametern wird ist es dabei möglich, Schichtzusammensetzung und Schichteigenschaften zu beeinflussen. Eine mechanistische Betrachtung der unterschiedlichen Prozesse während der Abscheidung soll dazu einen vertieften Einblick in die Vorgänge der Fe-Co-Legierungsabscheidung liefern.
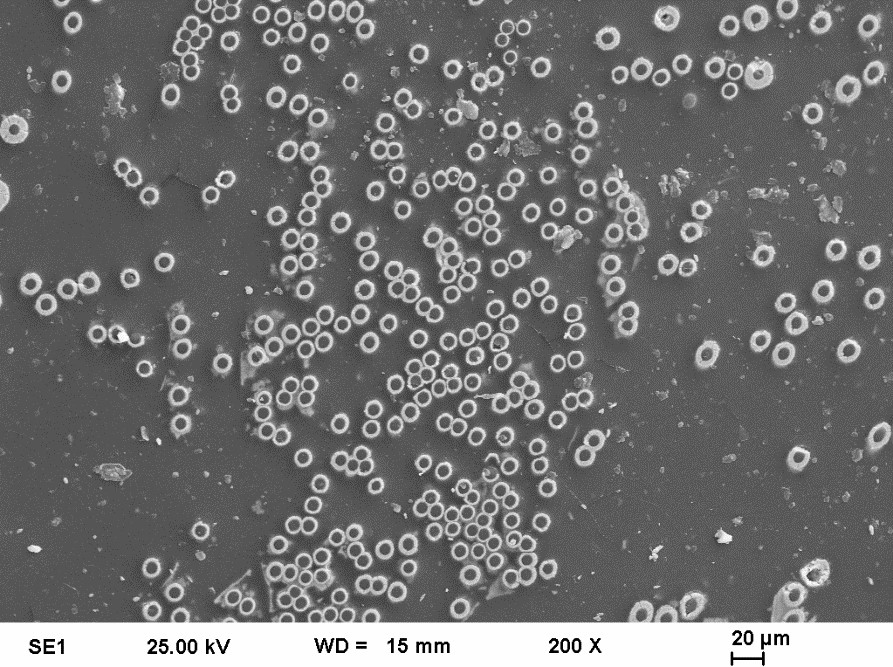
Im Bild: Querschliff von galv. abgeschiedenen Fe-Co-Legierungsschichten auf C-Fasern
Durchzuführende Arbeiten:
- Literaturrecherche zum Stand von Forschung und Technik
- Einstellung eines Grundelektrolyten zur Abscheidung von Fe-Co-Legierungen (auf unterschiedlichen Substraten)
- Planung, Durchführung und Dokumentation experimenteller Arbeiten
- Additivierung des Elektrolyten zur Optimierung der Abscheidebedingungen
- Prozessoptimierung & Verbesserung der Langzeitstabilität des Elektrolyten
- Schichtcharakterisierung (z.B. bzgl. Haftung und Duktilität)
- Auswertung und Diskussion der Ergebnisse im Vergleich zu dem internationalen Schrifttum
Voraussetzungen:
- Gute bis sehr gute chemische/elektrochemischen Kenntnisse
- Ev. Erfahrungen bzgl. Oberflächen und Beschichtungstechnik
- Experimentelles Geschick
- Fähigkeit zum interdisziplinären Arbeiten
- Sorgfältige und selbstständige Arbeitsweise
Wissenschaftlicher Betreuer:
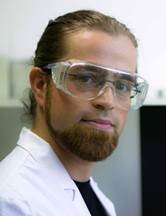
Elektrolyt- und Prozessdesign zur galvanischen Abscheidung von REACh-konformen Fe-Cr-Ni-Schichten
Im Fokus aktueller Forschungen stehen die Entwicklung und Optimierung technischer Errungenschaften zur Energiekostensenkung, Ressourcenschonung und Steigerung der Nachhaltigkeit. Hochlegierte Stähle wie z. B. 1.4301 (FeCr18Ni8) werden als Bulkwerkstoff standardmäßig für Anwendungen eingesetzt, die hohe Anforderungen an die Korrosions- und Verschleißbeständigkeit stellen. Leistungsfähige Bauteile können jedoch auch aus kostengünstigeren Werkstoffen gefertigt und mit dünnen metallischen Fe-Cr-Ni-Überzügen veredelt werden. Diese bieten dann die Vorteile einer hochlegierten Oberfläche, ohne das die Bauteile aus teurem Vollmaterial gefertigt werden müssen. Eine galvanische Applikation derartiger Legierungen könnte Kosten für Anwendungen erheblich senken. Des Weiteren bieten diese Legierungsschichten neben den guten Eigenschaften eine potenzielle Substitutionsmöglichkeit von Schichten, die bisher aus REACh-regulierten Cr(VI)-Elektrolyten abgeschieden werden und können eine Alternative zu Glanzchromsystemen darstellen.
Ziel ist es, die galvanische Abscheidung von Fe-Cr-Ni-Legierungen genauer zu betrachten und ein Elektrolyt- und Prozessdesign durchzuführen. Durch Variation von Elektrolyt- und Beschichtungsparametern wird ist es dabei möglich, Schichtzusammensetzung und Schichteigenschaften zu beeinflussen. Eine mechanistische Betrachtung der unterschiedlichen Prozesse während der Abscheidung soll dazu einen vertieften Einblick in die Vorgänge der Fe-Cr-Ni-Legierungsabscheidung liefern.
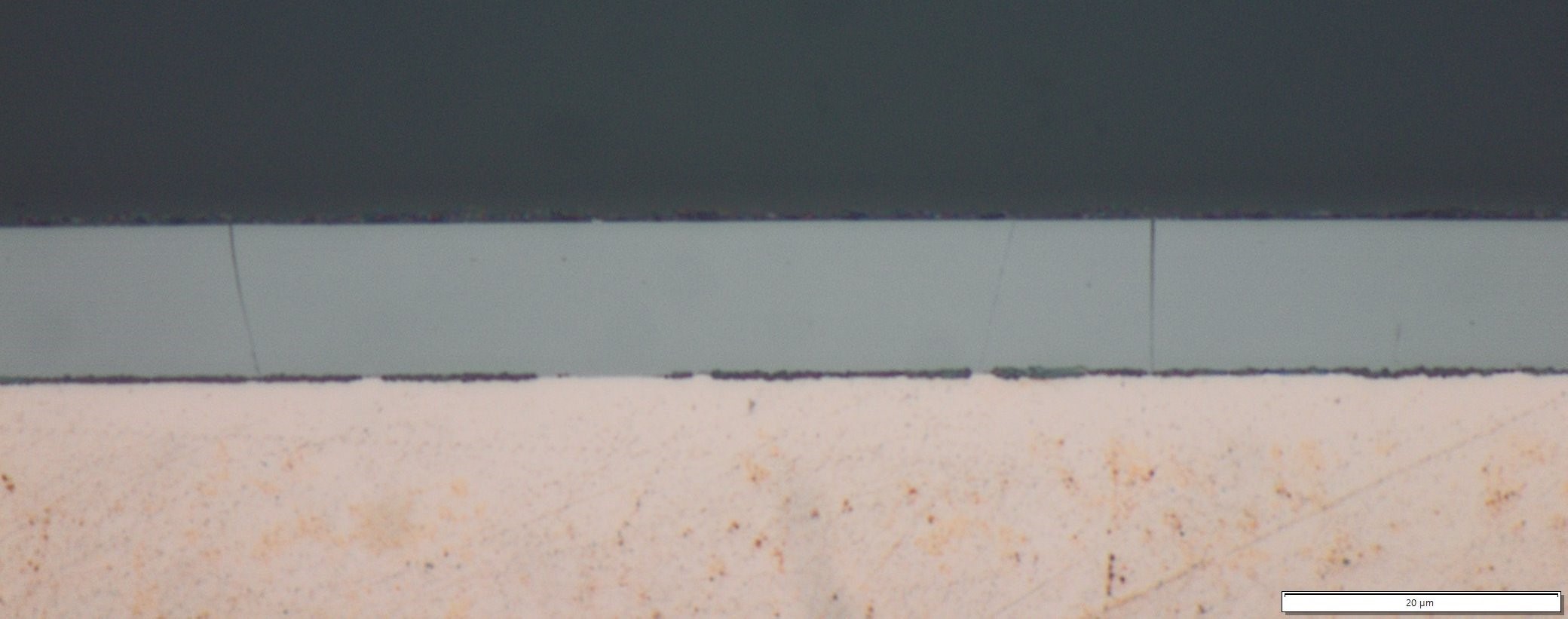
Im Bild: Querschliff einer galv. abgeschiedenen Fe-Cr-Ni-Legierungsschicht
Durchzuführende Arbeiten:
- Literaturrecherche zum Stand von Forschung und Technik
- Einstellung eines Grundelektrolyten zur Abscheidung von Fe-Cr-Ni-Legierungen
- Planung, Durchführung und Dokumentation experimenteller Arbeiten
- Additivierung des Elektrolyten zur Optimierung der Abscheidebedingungen
- Prozessoptimierung & Verbesserung der Langzeitstabilität des Elektrolyten
- Schichtcharakterisierung (z.B. bzgl. Verschleiß und Korrosion)
- Auswertung und Diskussion der Ergebnisse im Vergleich zu dem internationalen Schrifttum
Voraussetzungen:
- Gute bis sehr gute chemische/elektrochemischen Kenntnisse
- Ev. Erfahrungen bzgl. Oberflächen und Beschichtungstechnik
- Experimentelles Geschick
- Fähigkeit zum interdisziplinären Arbeiten
- Sorgfältige und selbstständige Arbeitsweise
Wissenschaftlicher Betreuer:
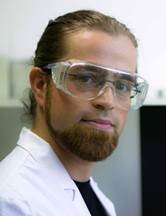
Elektrolyt- und Prozessdesign zur galvanischen Abscheidung von Multilagen-Schichtsystemen
Ziel der Arbeit ist die Entwicklung von gesundheitlich unbedenklichen Schutzschichten für den Korrosions- oder Verschleißschutz. Dies kann durch den Ausschluss von Nickel für den Korrosionsschutz oder durch Ausschluss von Cr(VI)-haltigen Elektrolyten für den Verschleißschutz realisiert werden. Bei den zu entwickelnden Multilagensystemen handelt es sich um es sich um mehrere übereinandergeschichtete Einzellagen zweier elektrochemisch abgeschiedener Metalle.
Hierunter sind auch Schichtsysteme zu verstehen, in denen sich binäre Legierungsschichten unterschiedlicher Zusammensetzung abwechseln. Galvanische Abscheidungen können dabei in unterschiedlichen Verfahren hergestellt werden: Zum einen kann die Abscheidung der alternierenden Schichten mit dem 2-Elektrolytverfahren (2-EL) mit Gleichstrom (2-EL-DC) in mehreren Prozessbädern oder mit dem 1-Elektrolytverfahren (1-EL) mit Hilfe von Pulsstrom- oder Gleichstrom-Abscheideprozessen (1-EL-PC/DC) in einem Prozessbad durchgeführt werden. Für den Korrosionsschutz werden alternierende Metalllagen unterschiedlicher Elektronegativität (Opferschicht und Schutzschicht) abgeschieden. So können z.B. konventionelle Zink-Nickel-Beschichtungen (jeweils 1 Schicht) durch alternierende zinkbasierte Multilagen, beispielsweise Zink-Eisen- oder Zink-Mangan ersetzt werden. Für den Verschleißschutz werden alternierende, nanometerdünne Metalllagen unterschiedlicher Härte abgeschieden. Die so abgeschiedenen Chrom- und Nickelbasierten Multilagenschichten könnten damit z.B. konventionelle Hartchrom- oder reine Nickeldispersionsschichten ersetzen.
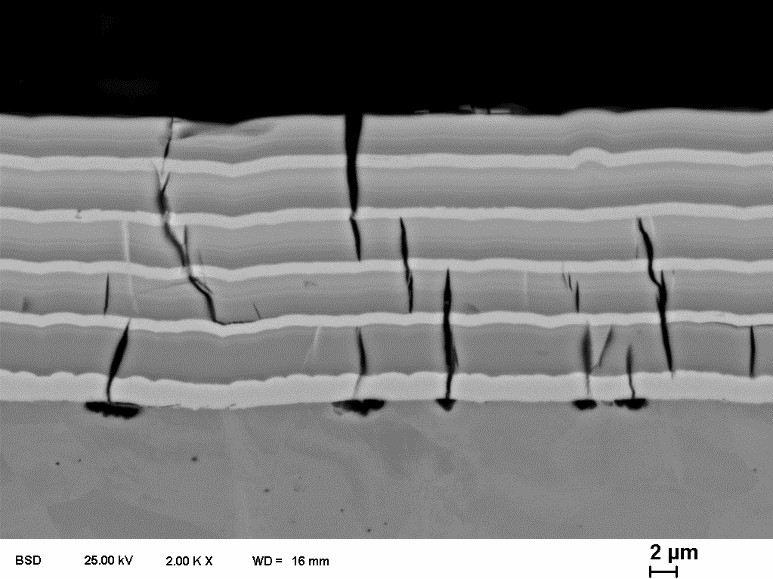
Im Bild: Rasterelektronenmikroskopische Aufnhame einer Cr-Ni-Multilayerschicht
Durchzuführende Arbeiten:
- Literaturrecherche zum Stand von Forschung und Technik
- Einstellung von Grundelektrolyten zur Abscheidung von Multilagenschichten
- Planung, Durchführung und Dokumentation experimenteller Arbeiten
- Additivierung des Elektrolyten zur Optimierung der Abscheidebedingungen
- Prozessoptimierung & Verbesserung der Langzeitstabilität des Elektrolyten
- Schichtcharakterisierung (z.B. bzgl. Verschleiß und Korrosion)
- Auswertung und Diskussion der Ergebnisse im Vergleich zu dem internationalen Schrifttum
Voraussetzungen:
- Gute bis sehr gute chemische/elektrochemischen Kenntnisse
- Ev. Erfahrungen bzgl. Oberflächen und Beschichtungstechnik
- Experimentelles Geschick
- Fähigkeit zum interdisziplinären Arbeiten
- Sorgfältige und selbstständige Arbeitsweise
Wissenschaftlicher Betreuer:
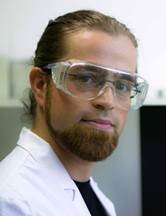
Abrasionsbeständigkeit hartstoffverstärkter lichtbogengespritzter Schichten im Rubber-Wheel-Test
Der Einsatz von Fülldrähten im Bereich des thermischen Spritzens ermöglicht die Herstellung hartstoffverstärkter Schichtsystem u. a. durch Drahtlichtbogenspritzen. Fülldrähte bestehen aus einem metallischen Hüllmantel sowie einer pulverförmigem Füllkomponente, welche sowohl metallischen als auch keramischen Charakter aufweisen kann. Die Verarbeitungseigenschaften der Einzelkomponenten unterscheiden sich z. T. erheblich, wodurch die Beschichtungsparameter entscheidend für die jeweilige Auftragwirkung der Pseudolegierung sind. Im Rahmen dieser Arbeit sollen die Verarbeitungseigenschaften verschiedener Fülldrähte mit Hartstofffüllung im Drahtlichtbogenprozess untersucht werden. Neben der Auftragwirkung der Einzelbestandteile soll insbesondere die Abrasionsbeständigkeit der resultierenden Schichtsysteme charakterisiert werden. Hierfür gilt es zunächst eine eingehende Charakterisierung ausgewählter Fülldrähte im Vorfeld einer Parameterstudie beim Drahtlichtbogenspritzen durchzuführen. Die hergestellten Schichtsysteme gilt es detailliert zu charakterisieren und hinsichtlich ihrer Abrasionsbeständigkeit im Rubber-Wheel-Test zu bewerten. Auf Basis der Ergebnisse sollen allgemeingültige Zusammenhänge zu Verarbeitungsbedingungen sowie dem Einfluss auf die Verschleißbeständigkeit abgeleitet werden.
Schwerpunkte der Arbeit:
- Recherche zu hartstoffverstärkten Fülldrähten auf Eisen-, Nickel-Basis als Spritzzusatzwerkstoff
- Metallographische und chemische Charakterisierung ausgewählter Fülldrähte
- Einarbeitung in die Anlagentechnik und Mithilfe bei den Drahtlichtbogenspritzversuchen (LS)
- Metallographische Charakterisierung der Schichtsysteme
- Bestimmung der Verschleißbeständigkeit im Rubber-Wheel-Test
Es ist eine Einzelarbeit einzureichen. Der Schwerpunkt der Projektarbeit kann in Absprache mit dem Betreuer individuell an den Stand der Arbeit bzw. die notwendigen Schritte angepasst werden.
Die Arbeit ist unter Berücksichtigung der Arbeitsanweisungen für die Anfertigung wissenschaftlicher Arbeiten der jeweiligen Fakultät der Technischen Universität Chemnitz zu verfassen.
Wissenschaftlicher Betreuer:
Infrarot Thermographie zur Überwachung thermischer Spritzprozesse
Die Oberflächentemperatur während des thermischen Spritzprozesses hat vielfältige Auswirkungen auf die späteren Schichteigenschaften. Neben der erhöhten Beanspruchung des Substratwerkstoffes fördern hohe Oberflächentemperaturen die Bildung von Eigenspannungen und erhöhen das Risiko der Rissbildung. Zudem besteht die Gefahr eines gesteigerten Oxidationsgrades. Eine Möglichkeit die Oberflächentemperatur kontaktlos im Beschichtungsprozess zu ermitteln, bietet die Infrarot (IR) Thermographie. Abhängig von dem Legierungssystem und der Oberflächenbeschaffenheit kann der Messwert aufgrund der unterschiedlichen IR Emission variieren. Zur Quantifizierung des potentiellen Fehlerbereiches und Beurteilung schichtspezifischer Einflussgrößen sollen im Rahmen dieser Arbeit an unterschiedlichen Legierungen und Schichtsystemen Temperaturmessungen mittels IR Thermographie (Optris XI80) und Thermoelement im Temperaturbereich 0–350 °C über induktive Erwärmung vergleichend durchgeführt werden. Hochgeschwindigkeitsflamm-, atmosphärischem Plasma- und Drahtlichtbogen gespritzte Schichten sind bei diesen Untersuchungen zu betrachten. Als Beschichtungswerkstoffe dienen Legierungen auf Eisen-, Nickel- und Kupfer-Basis.
Schwerpunkte der Arbeit:
- Recherche zu Schichtzusatzwerkstoffen auf Eisen-, Nickel- und Kupfer-Basis die sowohl in Draht als auch Pulverform verfügbar sind
- Einarbeitung in die Anlagentechnik und Mithilfe bei der Durchführung von thermischen Spritzprozessen wie Hochgeschwindigkeitsflammspritzen, atmosphärischem Plasmaspritzen und Drahtlichtbogenspritzen
- Einarbeitung in die Infrarot-Temperaturmessung und Thermografie
- Erstellung von Temperaturkalibrierkurven mit Hilfe taktiler Temperaturmesssysteme
- Anpassung und Kalibrierung der Infrarot-Thermografie-Messdaten
Es ist eine Einzelarbeit einzureichen. Der Schwerpunkt der Projektarbeit kann in Absprache mit dem Betreuer individuell an den Stand der Arbeit bzw. die notwendigen Schritte angepasst werden.
Die Arbeit ist unter Berücksichtigung der Arbeitsanweisungen für die Anfertigung wissenschaftlicher Arbeiten der jeweiligen Fakultät der Technischen Universität Chemnitz zu verfassen.
Wissenschaftlicher Betreuer:
Charakterisierung mikrostruktureller Einflussgrößen von oxidkeramischen Schichtsystemen hinsichtlich des tribologischen Eigenschaftsprofils
Keramische Werkstoffe zeichnen sich durch eine Reihe vorteilhafter Eigenschaften aus, die sie für verschiedene Anwendungen im Bereich der Oberflächentechnik qualifizieren. Neben einer hohen Härte und Verschleißbeständigkeit sind insbesondere die chemische Beständigkeit und eine hervorragende thermisch und elektrische Isolation charakteristisch. Ein aktueller Forschungsschwerpunkt ist die Entwicklung von keramischen Mischoxiden für überlagerte Beanspruchungsprofile. Das thermische Spritzen als Beschichtungsverfahren eignet sich in besonderer Weise für die Verarbeitung zur Oberflächenfunktionalisierung. Abhängig vom verwendeten Werkstoffsystem und den Beschichtungsparametern kann die Mikrostruktur der Schichtsysteme in einem breiten Spektrum variiert werden. Gleichzeitig kann die Phasenkonstitution durch die thermische Einwirkung im Prozess beeinflusst werden.
Die studentische Arbeit befasst sich mit der Erforschung von Wechselwirkungsbeziehungen zwischen Mikrostrukturausprägung und dem tribologischen Eigenschaftsprofil. Den Schwerpunkt bilden APS gespritzten Schichtsysteme aus dem binären Werkstoffsystem Al2O3-Cr2O3. Abhängig vom Belastungsprofil sollen die bestimmenden Verschleißmechanismen geklärt werden und qualitative Aussagen ausgehend von der Mikrostruktur abgeleitet werden.
Durchzuführende Arbeiten:
- Literaturrecherche: Thermisch gespritzte Schichten für tribologische Anwendungen, Schwerpunkt – keramische Schichten durch atmosphärisches Plasmaspritzen, Verschleißuntersuchungen
- Charakterisierung der Schichtsysteme hinsichtlich Härte, Porosität, Mikrostruktur, Phasenkonstitution
- Auswahl geeigneter Verschleißuntersuchungen, ggf. entsprechende Probenpräparation
- Durchführung und Auswertung der Verschleißuntersuchungen
- Beschreibung des Verschleißmechanismus
- Korrelation zwischen Mikrostruktur und Verschleißverhalten
Wissenschaftlicher Betreuer:
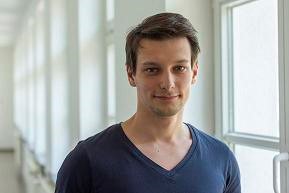
Untersuchung von Einflüssen der metallografischen Schliffpräparation thermisch gespritzter Hartmetallschichten auf die gemessene Porosität und Härte
Die Eigenschaften und Leistungsfähigkeit thermisch gespritzter Schichten hängen wesentlich von ihrer Mikrostruktur ab. Aus diesem Grund ist das Erlangen von Erkenntnissen zu den komplexen Wechselwirkungen zwischen Ausgangsmaterial, Spritzprozess sowie Schichtmikrostruktur von entscheidender Bedeutung bei der Entwicklung neuer Schichtsysteme.
Die Kennwerte Härte und Porosität spielen bei der Beurteilung neuer Schichtsysteme eine wichtige Rolle und werden zumeist an metallographisch präparierten Querschliffen ermittelt. Abhängig von der Präparationsroutine können jedoch während der metallographischen Schliffpräparation zusätzliche Defekte (z. B. durch Herausreißen einzelner Partikel / Splats) in die Beschichtung eingebracht werden. Diese Präparationsartefakte beeinflussen nachfolgende Messungen zur Bestimmung mikrostruktureller Kennwerte.
Im Rahmen der studentischen Arbeit wird der Einfluss metallographischer Präparationsroutinen auf die Ermittlung der wichtigen Kennwerte Porosität und Härte für unterschiedliche Schichtsysteme untersucht:
- Hartmetall-Schichten mittels Hochgeschwindigkeitsflammspritzen (HVOF)
- Oxidkeramische Schichten mittels atmosphärischem Plasmaspritzen (APS)
- Ni-Basisschichten mittels Pulverflammspritzen (PFS)
Dabei werden folgende Faktoren als wichtige Einflussgrößen während der metallographischen Präparation betrachtet:
- Entnahmeort (Lage bezogen auf Bewegung des Spritzbrenners)
- Trennschritt (z. B. Trennscheibe, Trenngeschwindigkeit, Trennwinkel)
- Schleifen und Polieren (z. B. Anpresskraft, Schleif- und Polierdauer, Schleif- und Polierschritte)
Zur Überprüfung des potenziellen Präparationseinflusses werden Porositäts- und Härtemessungen durchgeführt und in Abhängigkeit von der Präparationsroutine vergleichen. Die Porositätsmessung erfolgt mit Hilfe einer computergestützten Auswertung von lichtmikroskopischen Aufnahmen. Die Messung der Vickersmikrohärte HV0,3 erfolgt mittels Indenterverfahren nach DIN EN ISO 14923 bzw. DIN EN ISO 6507.
Durchzuführende Arbeiten:
- Literaturrecherche: Porositäts- und Härtemessungen an thermisch gespritzten Schichten, Schliffpräparation und mögliche Zusammenhänge mit den Messergebnissen
- Durchführung einzelner Präparationsschritte oder ganzheitliches Anfertigen von Querschliffen
- Anfertigung lichtmikroskopischer Aufnahmen
- Durchführung und Auswertung von Porositäts- und Vickersmikrohärtemessungen
- Zusammenfassung und Auswertung der Ergebnisse in Form einer schriftlichen, wissenschaftlichen Arbeit
Wissenschaftlicher Betreuer:
Einfluss adiabatischer Scherbänder auf das Korrosionsverhalten von hochgeschwindigkeits-schergeschnittenen Flächen
Inhalt:
Einfluss adiabatischer Scherbänder auf das Korrosionsverhalten von hochgeschwindigkeitsschergeschnittenen Flächen Spanlose Trennverfahren stellen die wirtschaftlich bedeutendsten Verfahren dar und kommen in nahezu jeder Großserienproduktion metallischer Bauteile zum Einsatz. Das Scherschneiden fasst alle spanlosen Trennverfahren zusammen, bei denen nach der Norm DIN 8588 die Werkstofftrennung durch zwei sich aneinander vorbei bewegende Schneiden erfolgt. In der Blechteilfertigung ermöglicht das Hochgeschwindigkeitsscherschneiden (HGSS) die Erzeugung von äußerst maßhaltigen, gratarmen Schnittflächen, die sich durch einen geringen Kanteneinzug sowie eine hohe Härte und geringe Rauheit auszeichnen und somit direkt als Funktionsflächen genutzt werden können. Dadurch entfallen aufwändige mechanische Nachbearbeitungen oder nachträgliches Härten, sodass eine Verkürzung der Prozesskette und damit eine Energieeinsparung ermöglicht wird. Die beim HGSS vorliegenden Anschnittgeschwindigkeiten von > 0,8 m/s können prozess- und werkstoffabhängig zur Ausbildung adiabatischer Scherbänder (ASB) führen. Dies sind lokalisierte, stark gescherte Werkstoffbereiche, die sich bei hohen Verformungsgeschwindigkeiten ausbilden, sich mikrostrukturell klar vom Grundwerkstoff abgrenzen sowie eine hohe Härte und Beständigkeit gegenüber Ätzangriffen aufweisen. Eine umfassende Betrachtung der Korrosionseigenschaften adiabatischer Scherbänder ist in der wissenschaftlichen Literatur bisher nicht gegeben. Daher ist das Ziel dieser Arbeit die Zusammenhänge zwischen den HGSS-Prozessparametern, der resultierenden Mikrostruktur des Werkstoffes und dem Korrosionsverhalten zu erarbeiten. Dafür werden vergleichend für normal- und hochgeschwindigkeitsschergeschnittene sowie unbehandelte Referenzproben aus dem Stahl 22MnB5 mikro- und makroskalige Korrosionsversuche und mikrostrukturelle Analyse durchgeführt.
Durchzuführende Arbeiten:
- Literaturrecherche zum Stand der Wissenschaft und Technik mit Fokus auf:
- Hochgeschwindigkeitsscherschneidprozesse (HGSS) und Beeinflussung der Mikrostruktur
- Korrosionsmechanismen und Einflüsse auf das Korrosionsverhalten
- Planung, Durchführung und Dokumentation experimenteller Arbeiten
- Makro- (Tauch- und Salzsprühnebeltest, Ruhepotentialmessungen) und Mikrokorrosionsversuche (Mikrokorrosionszelle) zur Bestimmung der Korrosionsneigung, -form und -rate
- Mikrostrukturelle Charakterisierung mittels Licht- und Rasterelektronenmikroskopie zur Charakterisierung der Mikrostruktur und des korrosiven Abtrags
- Oberflächenanalyse mittels Laser-Scanning-Mikroskopie
- Mikrohärtemessungen
- Auswertung und Diskussion der Ergebnisse und möglicher wirkender Mechanismen und Einflussfaktoren im Vergleich zu dem internationalen Schrifttum
Das Thema ist als Bachelor- oder Masterarbeit bzw. für vergleichbare studentische Arbeiten geeignet. Von den Studierenden wird eine selbstständige und verantwortungsvolle Arbeitsweise erwartet. Zudem sind gute Englischkenntnisse erforderlich, da die Mehrheit der zu recherchierenden Fachliteratur in englischer Sprache verfasst ist. Die Ergebnisse der Untersuchungen sind unter Berücksichtigung statistischer Auswertungsmöglichkeiten zu dokumentieren. Abweichungen zur Aufgabenstellung sind in Absprache mit dem Betreuer zu treffen.
Wissenschaftlicher Betreuer:
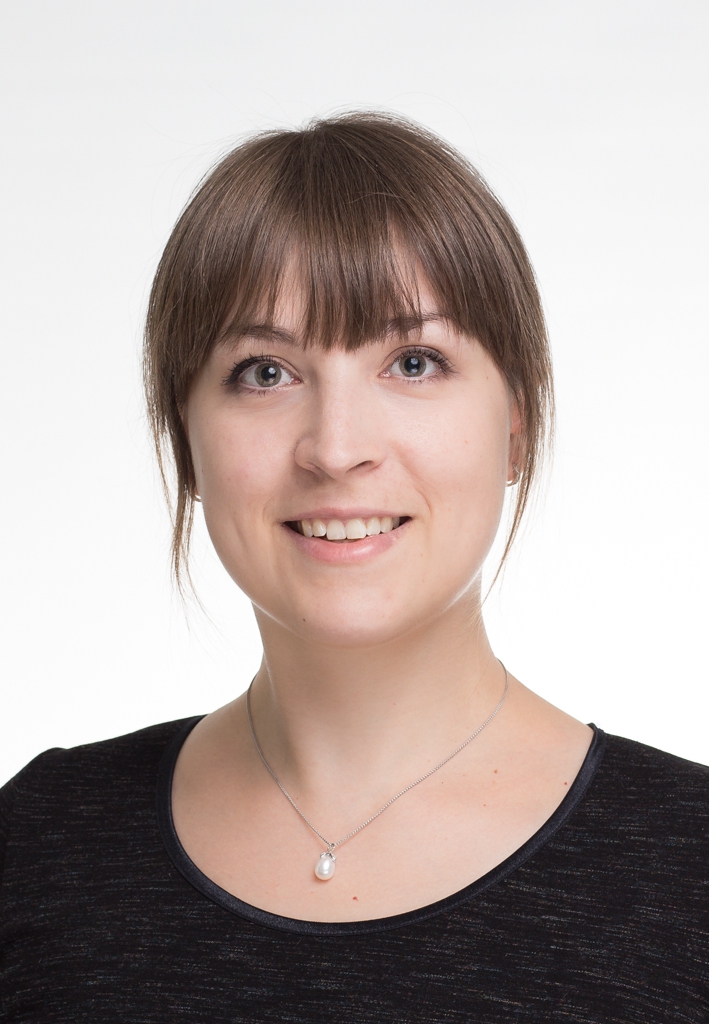
Elektrolyt- und Prozessdesign zur Herstellung cadmiumfreier Hartgoldschichten (extern)
Goldschichten zeichnen sich durch ihre ausgezeichnete Korrosionsbeständigkeit und ihre guten elektrischen Eigenschaften aus. Aus diesen beiden Eigenschaften resultiert die Anwendung in elektrischen Kontaktbauteilen, wie z.B. Steckverbindern, Kontakten für Relais oder Schaltern. In reiner Form ist Gold allerdings sehr weich und so werden dünne Goldschichten schnell durchgerieben. So werden in Schleifkontakten Hartgoldschichten eingesetzt in den bevorzugt das ternäre System Gold-Kupfer-Cadmium zum Einsatz kommt. Aufgrund der RoHS Verordnung für elektrische Kontakte ist die industrielle Verwendung von Cadmium ab Juli 2024 nicht mehr gestattet und es werden entsprechende Alternativen gesucht.
Ziel des Projektes ist es einen Hartgold-Elektrolyten zu entwickeln, welcher zäh-harte Gold-Legierungen mit hoher Verschleißbeständigkeit in hohen Schichtdicken > 10 μm abscheidet. Ebenso sollen ein tiefer Kontaktwiderstand und hohe Korrosionsbeständigkeit realisiert werden.

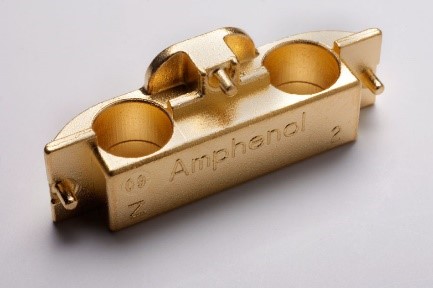
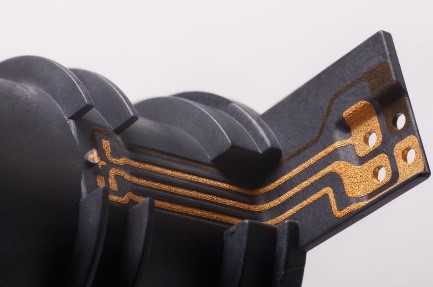
Dazu wird in Kooperation mit der Collini AG (www.collini.eu), einem international tätigen Unternehmen in der Oberflächenbeschichtung, eine Studienarbeit angeboten. Die Arbeit erfolgt mit direkter Anwendung in der Praxis am Standort von Collini in unmittelbarer Nähe zur Stadt Zürich in der Schweiz. Die Collini AG wird sich finanziell an den zusätzlich anfallenden Lebensunterhaltkosten bei einem Arbeitseinsatz in der Schweiz beteiligen.
Durchzuführende Arbeiten:
- Literaturrecherche zum Stand von Forschung und Technik
- Einstellung eines Grundelektrolyten zur Abscheidung von Hartgold-Legierungen
- Planung, Durchführung und Dokumentation experimenteller Arbeiten
- Addtivierung des Elektrolyten zur Optimierung der Abscheidebedingungen
- Schichtcharakterisierung bzgl. Verschleiß und Kontaktwiderstand
- Prozessoptimierung & Verbesserung der Langzeitstabilität des Elektrolyten
- Auswertung und Diskussion der Ergebnisse im Vergleich zu dem internationalen Schrifttum
Voraussetzungen:
- gute bis sehr gute Kenntnisse der chem. und elektrochemischen Beschichtungstechnik
- experimentelles Geschick
- Fähigkeit zum interdisziplinären Arbeiten
- sorgfältige und selbstständige Arbeitsweise
- Bereitschaft im Ausland (Schweiz) zu arbeiten
Wissenschaftlicher Betreuer:
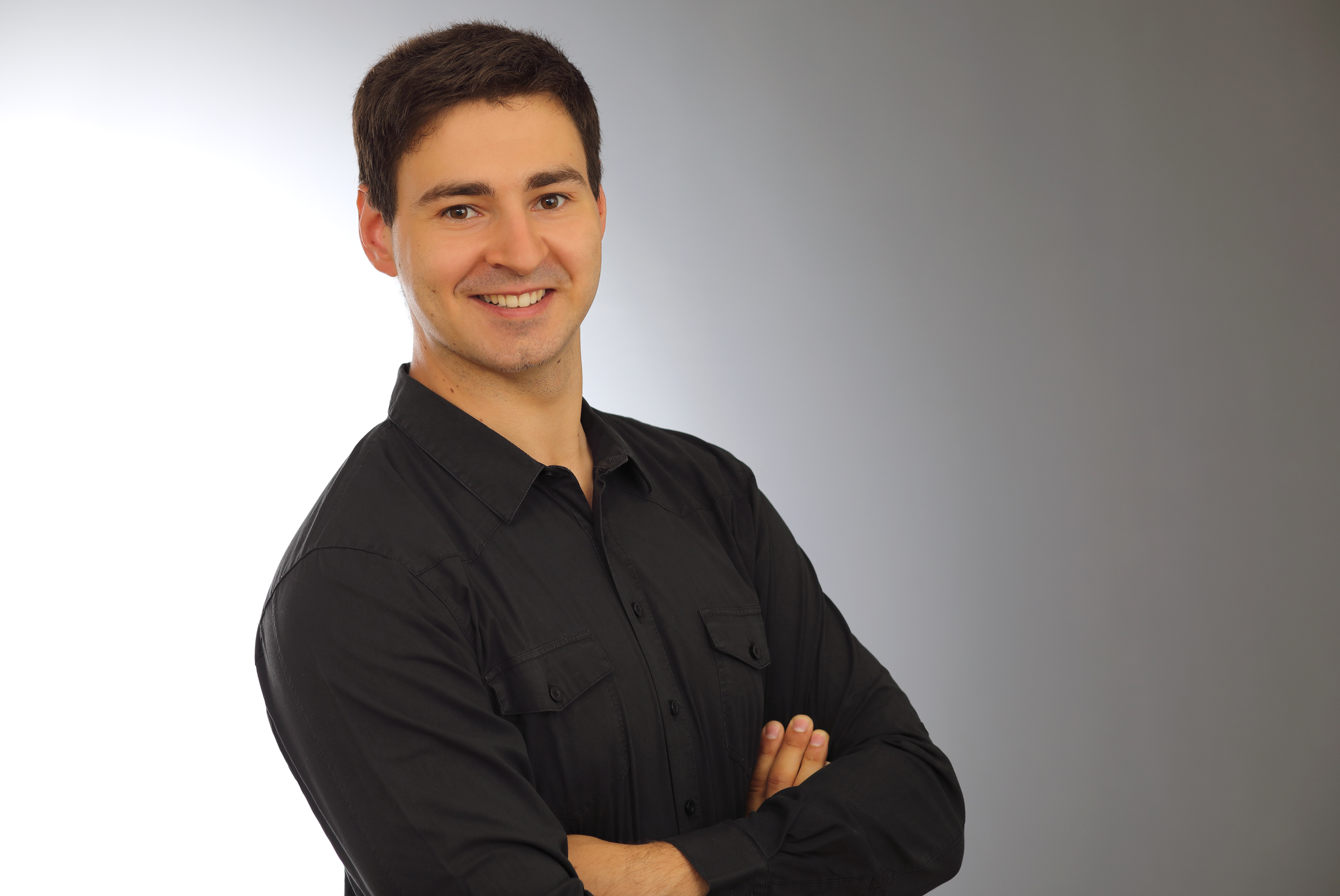
Synthese von plasmaelektrolytischen Schichten auf Eisenwerkstoffen für biomedizinische und industrielle Anwendungen
Die Firma MEOTEC ist ein innovatives Aachener Forschungsunternehmen, das auf die elektrochemische und plasmaelektrolytische Oberflächenmodifikation (Keramisierung) von Leichtmetallen spezialisiert und im Bereich der Medizingerätetechnik tätig ist.
Bei der anodischen Oxidation wird während eines Prozessablaufs traditionsgemäß mit konstanten Parametern (z. B. Stromstärke bzw. Stromdichte) gearbeitet. Diese Vorgehensweise birgt insofern einen Widerspruch in sich, als dass dem konstanten Regime eine nicht konstante, sich ständig verändernde Werkstoffoberfläche gegenüber steht.
Im Zuge der Arbeit sollen geeignete Elektrolyte und Parameter erforscht werden, um das Potenzial der plasma-elektrolytischen Oxidation (PEO) von Eisenbasiswerkstoffen für Anwendungen in der Medizintechnik und industriellen Bereichen wie dem Automobilbau oder der Luftfahrt grundsätzlichen bewerten zu können. Als Grundvoraussetzung wird der Nachweis der Machbarkeit technisch geschlossener und mechanisch belastbarer Eisenoxidschichten mittels PEO angesehen. Diese könnten Anwendung beispielweise als degradationsbeeinflussende Schichten für abbaubare Implantate auf Eisenbasis finden oder als thermische Barriere (TBC) und Verschleißschutz für Anwendungen im Motorenbau eingesetzt werden, z.B. bei der Veredelung des Kolbenbodens. Das Ziel der Arbeit ist daher, das Erheben eines umfassenden Standes der bislang publizierten Forschungsaktivitäten sowie das Ableiten geeigneter Parameterbereiche zur Erforschung und Optimierung von PEO-Schichten auf Eisenwerkstoffen.

Entwicklung des Entladungsverhalten währen der PEO von Al
Durchzuführende Tätigkeiten:
- Literaturrecherche
- Statistische Versuchsplanung (DoE)
- Probenherstellung (Elektrolyte, Beschichtungen)
- Materialographische Präparation und Analytik der generierten Schichten
- Auswertung der Versuche und Deduktion von Schichtbildungsmechanismen
Voraussetzungen:
- gute bis sehr gute Chemiekenntnisse
- experimentelles Geschick
- Fähigkeit zum interdisziplinären Arbeiten
- sorgfältige und selbstständige Arbeitsweise
Die Ausschreibung richtet sich an Studierende der Fachrichtung Medical Engineering
Bewerbung mit Nachweis bisheriger Studienleistungen an:
Dr. Alexander Kopp
Alexander.Kopp@meotec.eu
Phillipsstraße 8, 52068 Aachen
Wissenschaftlicher Betreuer:
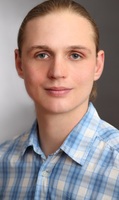
Kombi Kegelwalze für RAW 333
Als Teil der GMH- Gruppe betreibt die Schmiedewerke Gröditz an ihrem Standort ein Radial- Axial- Walzwerk (RAW330/260-4500/650).
Hier werden nahtlos gewalzte Ringe, Radreifen und Flansche bis zu einem Stückgewicht von 4.000kg und einem Außendurchmesser von 4.000mm hergestellt.
Im Zuge einer geplanten Modernisierungsmaßnahme schreiben wir für folgendes Projekt eine Diplom- bzw. Studienarbeit für den Bereich Maschinenbau/ Konstruktion aus.
Problembeschreibung:
Hohe Herstellungskosten und Rüstzeiten durch Wechsel der Kegelwalzen am RAW H330/ V260- 4500/ 650. Nach dem Erreichen der verschleißgrenze (wenige Millimeter) müssen 2 Kegelwalzen (ca. je 2t) komplett ausgebaut und aufgearbeitet werden.
Zielstellung:
Überprüfung der technischen und wirtschaftlichen Umsetzbarkeit einer Teilung der Kegelwalzen in Grundkörper (nicht wechselbar) und Arbeitskörper (Verschleißteil, wechselbar).
- Erarbeitung von Konzeptvorschlägen
- Untersuchung von Herstellungsmöglichkeiten
- Verfahrenstechnische Auslegung und Überprüfung der Konstruktion auf Lastsicherheit
- Auswahl der Vorzugsvariante anhand der technischen und wirtschaftlichen Rahmenbedingungen
- Errechnung der Amortisationsdauer
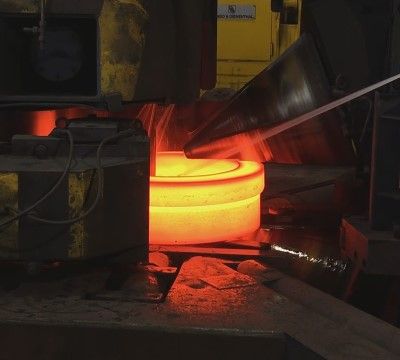
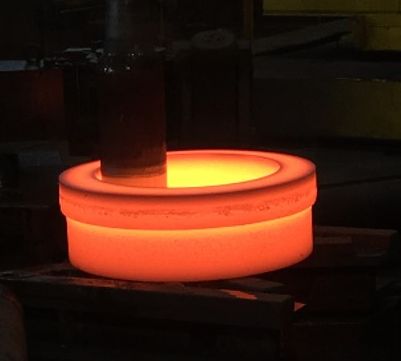
Industriepartner:
Weddin, Christopher
KVP Beauftragter Ringwalzwerk
Telefon: +49 35 26362 – 404
Mobil: +49 151 61558952
Christopher.Weddin@gmh-gruppe.de www.stahl-groeditz.de
Karasevich, Igor
Entwicklungsingenieur
Arbeitsvorbereitung Ringwalzwerk
Telefon: +49 35 26362 - 666
Mobil: +49 172 3602238
Igor.Karasevich@gmh-gruppe.de www.stahl-groeditz.de
Wissenschaftlicher Betreuer:
Walztischverstellung für RAW 333
Als Teil der GMH- Gruppe betreibt die Schmiedewerke Gröditz an ihrem Standort ein Radial- Axial- Walzwerk (RAW330/260-4500/650).
Hier werden nahtlos gewalzte Ringe, Radreifen und Flansche bis zu einem Stückgewicht von 4.000kg und einem Außendurchmesser von 4.000mm hergestellt.
Im Zuge einer geplanten Modernisierungsmaßnahme schreiben wir für folgendes Projekt eine Diplom- bzw. Studienarbeit für den Bereich Maschinenbau/ Konstruktion aus.
Problembeschreibung:
Keine automatisierte Verstellung der Walztische am RAW H330/ V260- 4500/ 650. Dieser muss bislang wöchentlich manuell mittels Schlagschrauber eingestellt werden.Keine automatisierte Verstellung der Walztische am RAW H330/ V260- 4500/ 650. Dieser muss bislang wöchentlich manuell mittels Schlagschrauber eingestellt werden.
Zielstellung:
Überprüfung der technischen und wirtschaftlichen Umsetzbarkeit einer automatisierten Walztischverstellung am RAW H330/ V260- 4500/ 650.
- Analyse vorhandenes System Walztischverstellung am RAW H160/ V100
- Überprüfung der technischen Rahmenbedingungen am RAW H330/ V260
- Erstellung der Konzeptvorschläge
- Auswahl der Vorzugsvariante anhand der technischen und wirtschaftlichen Rahmenbedingungen
- Errechnung der Amortisationsdauer
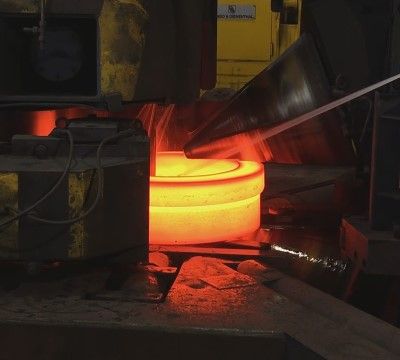
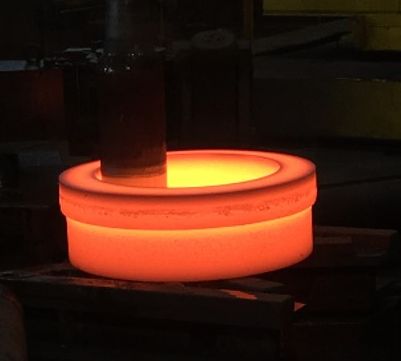
Industriepartner:
Weddin, Christopher
KVP Beauftragter Ringwalzwerk
Telefon: +49 35 26362 – 404
Mobil: +49 151 61558952
Christopher.Weddin@gmh-gruppe.de www.stahl-groeditz.de
Karasevich, Igor
Entwicklungsingenieur
Arbeitsvorbereitung Ringwalzwerk
Telefon: +49 35 26362 - 666
Mobil: +49 172 3602238
Igor.Karasevich@gmh-gruppe.de www.stahl-groeditz.de
Wissenschaftlicher Betreuer:
Themen für Praktikums- und Diplomarbeiten Schmiedewerke Gröditz
Anpassung des bestehenden Modells zur Berechnung der Walzkräfte beim Walzen
Adaption of the consisting calculation model of rolling forces
Erstellung Fehler- und Maßnahmekatalog für die Ringwalzerzeugnisse und Umformwerkzeuge
Generation of a catalogue of defects and measures for ring rolling products and forming tools
Tauchzeitberechnung in Abhängigkeit von der Ofenbelegung und des Werkstoffs für den Vergütungsprozess
Generation of a calculation model of quenching time in dependence on furnace occupancy and steel grade
Industriepartner:
Weddin, Christopher
KVP Beauftragter Ringwalzwerk
Telefon: +49 35 26362 – 404
Mobil: +49 151 61558952
Christopher.Weddin@gmh-gruppe.de www.stahl-groeditz.de
Karasevich, Igor
Entwicklungsingenieur
Arbeitsvorbereitung Ringwalzwerk
Telefon: +49 35 26362 - 666
Mobil: +49 172 3602238
Igor.Karasevich@gmh-gruppe.de www.stahl-groeditz.de
Wissenschaftlicher Betreuer:
Arbeitshinweise zum Erstellen von Studien-, Projekt- und Abschlussarbeiten
- Katalog zur Erstellung wissenschaftlicher Arbeiten
- Normensammlung zur Erstellung wissenschaftlicher Arbeiten
- Deckblatt für studentische Arbeiten
- Antrag zur Abschlussarbeit
- Antrag auf Verteidigung für Abschlussarbeiten
- Antrag auf Verlängerung einer Abschlussarbeit
- Selbstständigkeitserklärung für eine studentische Arbeit