Die übergeordneten Interacting Research Domains (IRD) entsprechen den technologieorientierten Kerngebieten zur Untersuchung und Entwicklung von passiven und aktiven Leichtbaustrukturen. Abgeleitet sind die IRDs vom Forschungsfokus des Forschungsclusters. Dieser beinhaltet das Verschmelzen von etablierten Schlüsseltechnologien für die Massenproduktion.
Halbzeuge und Preform-Technologien
Das Handlungsfeld IRD A befasst sich mit der Verarbeitung von Textilien, Kunststoffen und Metallen in einem In-line-Herstellungsprozess für großserientaugliche Anwendungen (Rolle-zu-Rolle). Das Forschungsprogramm inkludiert die Funktionalisierung von hybriden Strukturen, z. B. durch Einbindung verschiedener artefaktfrei wirkender Sensoren mittels modular verfügbarer Prozessschritte, die in die Fertigungslinie eingebaut werden können. Dabei werden Halbzeuge bzw. Preforms für die anderen kooperierenden Handlungsfelder zur Verfügung gestellt. Durch die Verknüpfung von bislang separaten Prozessschritten führen die synergetischen Effekte zur Minimierung der Fertigungszeit und Erhöhung der Funktionsdichte, wodurch maßgeblich zur nachhaltigen Material-, Energie- und Ressourceneffizienz beigetragen wird.
- Großserientaugliche Herstellung von hochfesten, hochsteifen hybriden Werkstoffverbunden, variabel in der Faser-, Kunststoff- und Metallkomponente sowie in der Struktur
- Bereitstellung von Konzepten für die In-line-Fertigung von mehrschichtigen Verbunden aus Metall/Kunststoff und Metall/FKV sowie nachfolgender Umformprozesse
- kontinuierliche Herstellung von intelligenten hybriden Verbunden mit sensorischen Komponenten für strukturelle Zustandsüberwachungssysteme (SHM)
- Integration von Umformprozessen für endkonturnahe hybride Bauteile
- Anpassung des Herstellungsprozesses für textile thermoplastische Verbundwerkstoffe für eine optimale Gestaltung der Bauteilstrukturen mit bionisch inspirierten Strukturen
- Entwicklung eines komplexen kontinuierlichen Orbitalwickelprozesses (COW-Technologie) zur Herstellung von unsymmetrischen Strukturbauteilen (konkav, konvex)
IRD A1 | Großserienherstellung von hochfesten, hochsteifen hybriden Materialverbundwerkstoffen |
IRD A2 | Neuartige Orbitalwickeltechnologie für einstellbar faserverstärkte thermoplastische Halbzeuge |
IRD A3 | Entwicklung belastungsgerecht ausgelegter Halbzeuge nach bionischem Vorbild |
IRD A4 | Kontinuierliche Herstellung von Sensoren zur Strukturüberwachung in hybriden Werkstoffverbunden |
Metallintensive Technologien
Zielstellung des IRD B ist die funktionale Erweiterung metallintensiver Technologien zur Herstellung hybrider Metall-Kunststoff-Verbunde. Die Motivation besteht darin, die Effizienz der Fertigungstechnologien für metallische Werkstoffe zu nutzen, um hybriden Bauteilen den Weg in die Großserie zu öffnen. Aufgabenschwerpunkte liegen in der Grundlagenerforschung für die Implementierung von Kunststoff, Textil- und Elektronikelementen durch Technologieintegration in effiziente Prozessketten für metallische Basisstrukturen. Formgebung und Funktionalisierung des Bauteils sollen dabei durch Technologiefusion, nicht durch isolierte Fügeprozesse in sich optimierter Baugruppen, erfolgen.
Die wissenschaftlichen Untersuchungen von rohstoffeffizienten Verfahren für hybride Leichtbaustrukturen basierend auf Metallen und deren Herstellungstechnologien verfolgen die nachstehenden wissenschaftlichen Strategien des Forschungsprogrammes in den Teilprojekten:
- Entwicklung von Sandwichbauteilen mit Metallschaum und Faserverbund-Decklagen
- Erarbeitung der thermischen und rheologischen Prozessparameter für die Kombination von Metallumformung und Kunststoffspritzgießverfahren
- Erweiterung der Prozessgrenzen bei Umformprozessen von Metallen durch integrierte Spritzgießprozesse
- Herstellung funktionaler Oberflächenstrukturierungen auf metallbasierten Hybriden
- Entwicklung geeigneter, integrativer Fügetechnologien für Metall-FKV-Hybride
- Planung von Evaluationsmethoden und Gestaltungsprozessen für hybride Bauteile
- Weiterentwicklung von IT-Werkzeugen für Wissensmanagement und Prozessplanung
-
Entwicklung adaptiver Metall-Textil-Verbundstrukturen bestehend aus FGL-Metallfilamenten,
Textilfasern und integrierter Elektronik und Sensorik
Die Problemlösungen und Methoden werden durch die Konstruktion, Simulation, Herstellung und Untersuchung von Grundstrukturen und generischen Funktionsdemonstratoren überprüft. Die ausgewählten Lösungen werden in die MERGE-Demonstratoren integriert und getestet.
Die Forschungsarbeit im IRD B wird in Kooperation mit dem Fraunhofer-Institut für Werkzeugmaschinen und Umformtechnik (IWU) durchgeführt.
IRD B1 | FKV-Metallschaum-Hybridstrukturen (Demonstratorprojekt, Verbindung zu A1) |
IRD B2 | Wirkmedienbasierte Herstellung von Metall-Kunststoff-Hybridbauteilen |
IRD B3 | Funktionale Metall-Kunststoff-Übergangsstrukturen |
IRD B4 | Ressourceneffiziente Prozesse für die Herstellung von hybriden Strukturen |
IRD B5 | Funktionale Hybridtextilien mit Metallfilamenten |
Textil-/Kunststoffbasierte Technologien
Endlosfaserverstärkte Kunststoffe sind in der Schlüsseltechnologie Leichtbau von großer Bedeutung, da sie sich durch sehr hohe richtungsgebundene spezifische mechanische Eigenschaften auszeichnen und ein hohes Potenzial zur Funktionsintegration bieten. Zudem können die Verstärkungsfasern aufgrund der vielfältigen textilen Flächenbildungstechniken optimal an die herrschenden Belastungen angepasst werden.
Das Ziel, endlosfaserverstärkte Leichtbaustrukturen in großen Stückzahlen herstellen zu können, erfordert aber auch die Entwicklung effizienter thermoplastbasierter Kunststoffverarbeitungsverfahren wie etwa Spritzgieß- oder Presstechnologien mit der Integration von Textilverstärkungen. Neben der gleichzeitigen Verarbeitung mehrerer Kunststoffe lassen sich weitere metallische oder elektronische Komponenten im Verfahren in Bauteile integrieren, wodurch Hybridbauteile effektiv und ohne aufwändige Fügeverfahren hergestellt werden können. Im Sinne der Nachhaltigkeit ist auch die Verwendung von Naturfasern sowie biobasierten oder bioabbaubaren Kunststoffen vorgesehen.
- Entwicklung von Methoden für das Verschmelzen von ähnlichen Funktionsprinzipien innerhalb des Spritzgießens von faserverstärkten Kunststoffen, Metallleichtbaustrukturen und der Oberflächenfunktionalisierung
- Optimierung des Faserverbundes in kraftflusskompatiblen textilen Halbzeugen
- Mehrkomponentenspritzgießtechnologie für die In-Situ-Kontaktierung und Kombination von aktiven Elementen mit Hilfe von elektrisch leitenden und isolierenden Thermoplasten
- Zusammenführung von Spritzgieß- und Tapelegetechnologien für die Integration von miniaturisierten Elektronikeinheiten und elektromechanischen Mikrosystemen
- Technologieforschung von hochgradig verstärkten multifunktionalen Hybridbauteilen und deren Fertigungsverfahren für die Herstellung von Leichtbauteilen aus Naturfasern mit biologisch abbaubaren Polymeren
- Auswertung der prozessadaptierten, mechanischen Eigenschaften von physiologisch kompatiblen Textil-/Kunststoffbauteilen durch Beobachtung der anisotropischen Effekte
- Ausführlicher Test der Konstruktionen in einem primären Systemdemonstrator, dem Chemnitz Car Concept (CCC)
IRD C1 | MERGE Technologien mit Textil-/Metallbauteilen und funktionalen Oberflächen durch integrative Kunststoffspritzgießverfahren für den CCC Systemdemonstrator |
IRD C2 | Prozessverschmelzung von Metalldruckguss-/Kunststoffspritzgießtechnologien für Bauteile von Leichtbauförderanlagen |
IRD C3 | Großserientaugliche Herstellungstechnologie und Messdatenauswertung für sensorische Hybridlaminate |
IRD C4 | Flexible Textil-/Kunststoffverfahren mit erneuerbaren Rohstoffen |
IRD C5 | MERGE Technologien für physiologisch kompatible Textil-/Kunststoffbauteile durch anisotropische Effekte |
Integration von Mikro- und Nanosystemen
Um Leichtbaustrukturen viel intelligenter zu machen, werden im Forschungsbereich „D-Mikro- und Nanosysteme Integration“ Mikrosysteme, intelligente Sensoren, Aktoren und Elektronik integriert. Dabei stehen Themen der Technologieentwicklung für die Integration der Sensoren, Aktoren und Sensormaterialien in bestehende Fertigungsprozesse, sowie die Integration ihrer Stromversorgung, neuer Kommunikationsmethoden basierend auf der Integration von Metamaterialien in die Strukturen im Fokus der Arbeiten. Zuverlässigkeitsuntersuchungen und Fehlererkennung komplettieren diesen Forschungsbereich.
Innerhalb dieses Forschungsbereiches werden Methoden für intelligente Strukturleichtbauten mit
erhöhter Funktionsdichte entwickelt Die Forschungsaktivitäten konzentrieren sich auf alle
Aspekte solcher „intelligenten“ Textilleichtbaustrukturen und Systeme, inklusive
Systemkonstruktion, Technologieentwicklung für die Integration von sensorischen und aktorischen
Funktionalitäten, Stromversorgung und Kommunikation, als auch Zuverlässigkeitsuntersuchungen.
Innerhalb der vier vernetzten Teilprojekte (D1 bis D4) werden im Detail folgende
Forschungsthemen bearbeitet:
- Entwicklung neuer Konstruktionsmethoden mit den ihnen jeweilig zugeordneten In-Situ Technologien um die Integration von elektromechanischen Umformern in heterogenen Verbundkomponenten zu ermöglichen, und eine Konzeption von Modellen und Instrumenten für eine wirtschaftliche Beurteilung von Hybridtechnologien
- Bandfertigungsherstellungsstrategien für das Integrieren von innovativen, folienbasierten Sensoren und Generatoren
- Integration der Stromversorgung und Übertragung dieser Sensoren und Generatoren
- Kommunikationsmethoden für Sensoren und Aktuatoren durch systemintegrierte Metawerkstoffe
- Integration siliziumbasierter Sensorsysteme, als auch Zuverlässigkeitsuntersuchungen und Fehlererkennung in FPR Bauteilen
Um die Ressourceneffizienz zu erhöhen, ist es notwendig, die sensorischen, aktuatorischen, und elektronischen Elemente direkt in den Herstellungsprozesses zu integrieren. Das erfordert die Weiterentwicklung von Technologien, um die werkstoffliche Einbindung von Siliziumsensoren zu ermöglichen. Darüber hinaus ist es notwendig die gegenseitigen Wechselwirkungen zwischen dem Sensor und des Verbundwerkstoffes zu verstehen, zu analysieren und zu kontrollieren.
Bei der Beobachtung von Lastzuständen in Leichtbaubauteilen wird der innovative Ansatz der Integration folienbasierter Großsensoren verfolgt. Diese werden in die Strukturen eingebunden und visualisieren eine mechanische Belastung durch eine Helligkeitsänderung bzw. einen Farbwechsel.
Die Einbindung von extrem kleinen Sensoren, Aktuatoren, und Geräten für die Datenverarbeitung und Kommunikation erleichtert innovative Anwendungen, benötigt allerdings ebenfalls neue Integrationskonzepte. Davon abgesehen sind Kraftübertragung und Kommunikation entscheidend in Bezug auf die hohe Dichte dieser Sensorknoten, welche wiederum die Entwicklung von neuen innovativen kabellosen Energie- und Informationsübertragungsmethoden notwendig macht.
Um ein höheres Level an Zuverlässigkeit sowie auch an niedrigeren Herstellungs- und Betriebskosten zu erreichen, werden Konzepte für die Auswertung des erreichbaren Profits in Zusammenhang mit den angewandten Ressourcen bereitgestellt.
IRD D1 | Entwurfsverfahren und -technologien für die Integration von elektronisch funktionalen Elementen in heterogenen Bauteilen |
IRD D2 | Technologien für die Einbettung folienbasierter Sensoren und Generatoren |
IRD D3 | Verfahrenstechnik für die Integration von Metamaterialien für Energieübertragung und Kommunikation |
IRD D4 | Technologien für die Integration von miniaturisierten Silizium-Sensorsystemen zur Fehlererkennung in Hybridbauteilen |
Interface Technologien, Interface Engineering
Die Kombination unterschiedlicher Werkstoffgruppen in funktionsoptimierten, hybriden Leichtbaukonstruktionen erfordert die Anwendung definierter Grenzflächenverbindungen, welche die gestellten Anforderungen an Festigkeit, Steifigkeit, Korrosion, Verschleiß, Alterung und andere Eigenschaften erfüllen.
IRD E dient als Querschnittsforschungsgebiet, in welchem grundlegende Wechsel-mechanismen für eine bestmögliche Kontaktflächenhaftung bei FKV, Polymer- und Metallverbundsystemen untersucht werden. Das Hauptziel der Entwicklungsarbeit liegt auf der Realisierung hoher interlaminarer Zug- und Scherfestigkeiten, um herstellungs- und einsatzbedingt überhöhte Belastungen in die Verbindungsfläche einleiten zu können. Eine geeignete Interfacekonstruktion wird durch den Einsatz chemischer oder mechanischer Oberflächenveränderungen und durch das Auftragen haftungsunterstützender Zwischen-schichten entwickelt. Darüber hinaus wird für die Integration elektronischer und funktionaler Elemente mit punktuellen und flächigen Füge- bzw. Kontaktiertechniken eine funktionalisierte Oberfläche benötigt. Dadurch wird eine Anbindung und beispielsweise elektrische Leitfähigkeit auf Kunststoff- oder FKV-Trägermaterialien ermöglicht.
Zuverlässige, energiearme Füge- und Kontaktierverfahren, die hohe mechanische Festigkeiten und temperaturstabile Verbindungen erzeugen, sowie Hochgeschwindigkeits-Fügeprozesse, müssen unter besonderer Berücksichtigung der Verarbeitungstemperatur und Handhabung entwickelt werden. Der Ausdehnungskoeffizient wird mittels Materialauswahl, Abstimmung der Grenzschichten und Justierung der Fügeverfahren bedarfsgerecht angepasst. Dadurch können während der Herstellung- und Betriebszeit entstehende Eigenspannungen hinreichend gehandhabt werden.
Die wissenschaftliche Herausforderung des IRD E ist es, das Interface – den Schwachpunkt des Verbundwerkstoffs - zu konstruieren, anzupassen, und zu gestalten.
- Die Kombination verschiedener Werkstoffklassen in Leichtbaustrukturen erfordert ein genau definiertes Zusammenspiel innerhalb der Grenzflächenverbindung auf der Mikro-, Meso-, und Makroebene. Die unterschiedlichen Wärmeausdehnungen der einzelnen Werkstoffe, in Abhängigkeit von den Prozessparametern, führen oft zu Eigenspannungen im Bereich der Verbindungsstelle, was zum Verzug des gesamten Verbunds führt.
- Um eine Langzeitverwendung von Polymer-Metallverbindungen zu ermöglichen, werden Monomere synthetisiert, welche geeignet sind zu polymerisieren und simultan kovalente Bindungen zu bilden. Dies wird durch die Zusammensetzung der Monomere kontrolliert, welche schwache chemische Bindungen enthalten, die durch die Wärme des Herstellungsprozesses reagieren (Spritzgießen oder Presstechnologie). Dabei wird besondere Aufmerksamkeit auf Lagerungsfähigkeit und Reaktivität gelegt.
- Die Beurteilung des vorhandenen Interfaces erfordert geeignete Methoden auf Mikroebene, wie Nanoindentation, Röntgenbeugung, hochauflösende Mikroskopie und elektrochemische Verfahren. Lokale mechanische Eigenschaften werden durch angepasste Versuchsmethoden bestimmt. Die erhaltenen Daten bilden die Grundlage für die detaillierte Konstruktion und Anpassung der einzelnen Grenzflächenverbindungen.
- Niedrigschmelzende Lote werden für den Fügeprozess funktionaler Elemente auf der Basis von Übergangsmetallkomplexen und organischen Bindemitteln (gefüllt mit Nanopartikeln) entwickelt. Um diese Lote auf temperatursensible Trägermaterialien aufzutragen, werden Techniken wie Dipcoating, Nanodruck angewendet. Hierbei wird der Einfluss von Partikelgrößen und Verteilungen von Nanoteilchen in den Lötsuspensionen sowohl beim Druckprozess als auch bei dem anschließenden Lötprozess systematisch untersucht.
IRD E1 | Optimierung des Interface von metall- und polymerbasierten Herstellungsprozessen für lastkompatible Hybridbauteile |
IRD E2 | Interfacegestaltung für die Integration von mikro- und nanoelektronischen Systemen in hybride Bauteile |
Modellierung, integrative Simulation und Optimierung
Das Hauptziel des interdisziplinären Querschnittsforschungsgebietes IRD F bilden die Simulation, Optimierung und Auslegung multifunktionaler Leichtbaustrukturen. Deren Bauteileigenschaften werden von den Parametern der Herstellungsprozesse beeinflusst. Dazu zählen u.a. prozessinduzierte Eigenspannungen, welche experimentell untersucht werden. In bivalenten Optimierungen werden sowohl voll parametrisierte Simulationen des Herstellungsprozesses als auch die Berechnung der Betriebslastfälle des entstehenden Hybridbauteils ganzheitlich betrachtet. Ein effizientes Datenmanagement und eine dezentralisierte Computerumgebung erleichtern die aufwendigen Berechnungen. Die in IRD F entwickelten Methoden und Ansätze werden auf Grundlage der hybriden Systemdemonstratoren des Forschungsclusters MERGE überprüft und validiert.
Um die Hauptziele des IRD F realisieren zu können, werden folgende wissenschaftliche Strategien verfolgt:
- Experimentelle Charakterisierung von Eigenspannungen
- Analytische Auswertung der Eigenspannungen und deren Einfluss auf das Versagen des Materials
- Weiterentwicklung der Fehlerschätzer und -indikatoren in einer adaptiven FEM-Umgebung
- Formulierung konstitutiver Gleichungen zur Beschreibung verstärkter thermoplastischer Materialien unter Berücksichtigung von Phasenübergangseffekten, Anisotropie und Eigenspannungen
- Aufbau einer voll parametrisierten FEM-Umgebung zur Simulation hybrider Strukturen
- Bivalente Optimierungen mit hoch effizienten Rechenstrategien
IRD F1 | Adaptive hochpräzise Finite-Elemente-Methode für die Simulation von Hybridstrukturen durch fortschrittliche Stoffgesetze und Charakterisierungsmethoden |
IRD F2 | Multikriterielle Optimierung kombinierter Simulationen von Herstellungsprozessen und Bauteilen mit effizientem Datenmanagement und Parallelausführungen |
Netzwerkbereich
Die Aufgaben des Netzwerkbereichs liegen in der interdisziplinären Unterstützung der Forschungsarbeiten in den einzelnen IRDs. Durch zielgerichtete interne Vernetzungsaktivitäten werden die Erkenntnisse aus den IRDs zusammengeführt, um somit existierende Technologien für die ressourcenschonende Massenproduktion für die Herstellung von Leichtbaustrukturen bereitzustellen. Neben den internen Aktivitäten ist die externe Vernetzung zur Industrie ein weiteres Ziel. Dadurch soll gewährleistet sein, dass die auf Grundlagenforschung basierenden Ansätze mittelfristig industriell nutzbar gemacht werden können.
Des Weiteren ist der Netzwerkbereich in den Aktivitäten des Roadmap Teams involviert, dessen Aufgabe es ist, die systematische Analyse, Planung und Priorisierung der eigenen Forschungsaktivitäten sowie das Analysieren internationaler Forschungstätigkeiten durchzuführen.
Schließlich wirkt der Netzwerkbereich daran mit, dass Forschungsergebnisse in geeigneter Form in die Entwicklung von Lehrinhalten der TU Chemnitz und hier insbesondere in das geplante PhD-Programm einfließen. Auf diese Weise wird die exzellente Ausbildung des Forschungsnachwuchses gesichert.
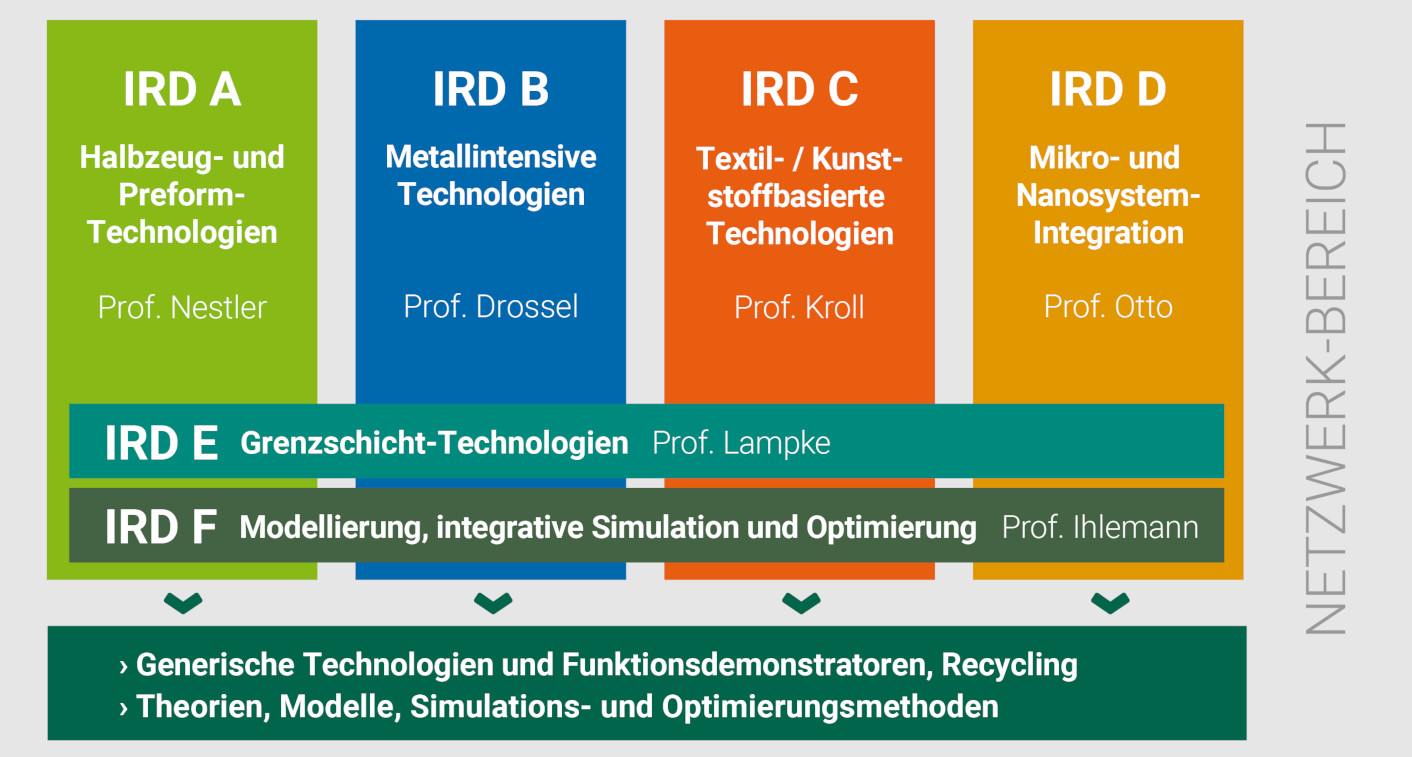