TUCelino
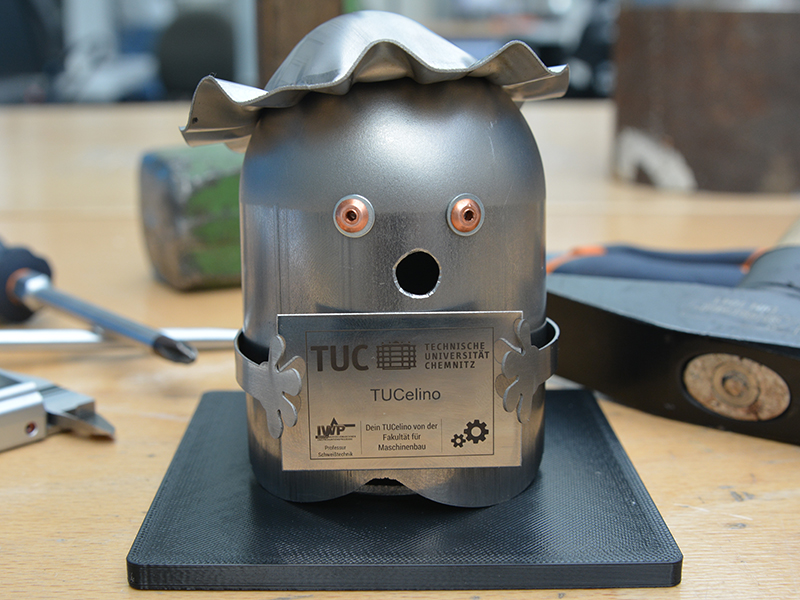
TUCelino (ausgesprochen: Tukelino) ist ein Uni(kat)-Räuchermännchen, welches als Projekt an der Fakultät Maschinenbau entstanden ist. Für den Tag der offenen Tür am 30. Mai 2015 in Verbindung mit der Kinder-Uni, die ebenfalls an diesem Tag stattfand, dachten sich die Professuren Werkzeugmaschinen und Umformtechnik, Virtuelle Fertigungstechnik, Mikrofertigungstechnik, Schweißtechnik sowie Umformendes Formgeben und Fügen etwas Besonderes aus: Eine Art Bastelkurs mit verschiedenen Fertigungsverfahren für Jung und Alt, der mit dem Slogan „Bau dir Deinen eigenen TUCelino. Das Original mit Krempenhut!“ beworben wurde. Besucher hatten die Möglichkeit, an mehreren Stationen Schritt für Schritt ihr eigenes Räuchermännchen entstehen zu lassen. An jeder Fertigungsstation erhielt man Einzelteile, die am Ende nur noch zusammengefügt werden mussten.
Ziel dieser Aktion war es, sich am Ende des Tages nicht nur ein selbst gebautes Andenken, sondern auch viele interessante Eindrücke von der Universität und von Fertigungsverfahren mitnehmen zu können. Der geistige Vater des TUCelinos Dr. Thomas Hänel, Ingenieur an der Professur Werkzeugmaschinen und Umformtechnik, erklärte, dass die Professuren mit dem Räuchermännchen etwas Regionaltypisches vorstellen wollten und damit vor allem jüngere Besucher ansprechen wollten, welche spielerisch die Möglichkeiten der Werkzeugmaschinen-Produktion und somit die Fakultät für Maschinenbau näher kennenlernen sollten.

Arbeitsschritte:
Wer genau wissen will, wie ein TUCelino-Männchen hergestellt wird: es sind insgesamt sieben Arbeitsschritte notwendig:
- Der TUCelino Krempenhut entsteht durch Tiefziehen mit Niederhalter, ein Pressverfahren der Professur Umformendes Formgeben und Fügen
- Der TUCelino Körper wird ähnlich dem vorherigen Schritt mittels Tiefziehen ohne Niederhalter der Professur Virtuelle Fertigungstechnik geformt.
- Der TUCelino Mund entsteht durch Bohren & Drehen in den Körper.
- Die Arme und Händchen des TUCelino werden mittels Wasserstrahlschneiden der Professur Werkzeugmaschinen hergestellt.
- Das Namensschild mit individueller Gravur wird durch die Professur Mikrofertigungstechnik aus einem Edelstahlblech gefertigt, welches durch Lasergravieren personalisiert wird.
- Die Augen des TUCelino bilden Unterlegscheiben, welche von den Schweißtechnikern genau wie die Arme durch Nieten an den Körper montiert werden.
- Sind alle benötigten Teile des Räuchermännchens gefertigt, werden diese mittels Heißkleben verbunden.
Der Spitzentechnologiecluster „Energieeffiziente Produkt- und Prozessinnovationen in der Produktionstechnik eniPROD“
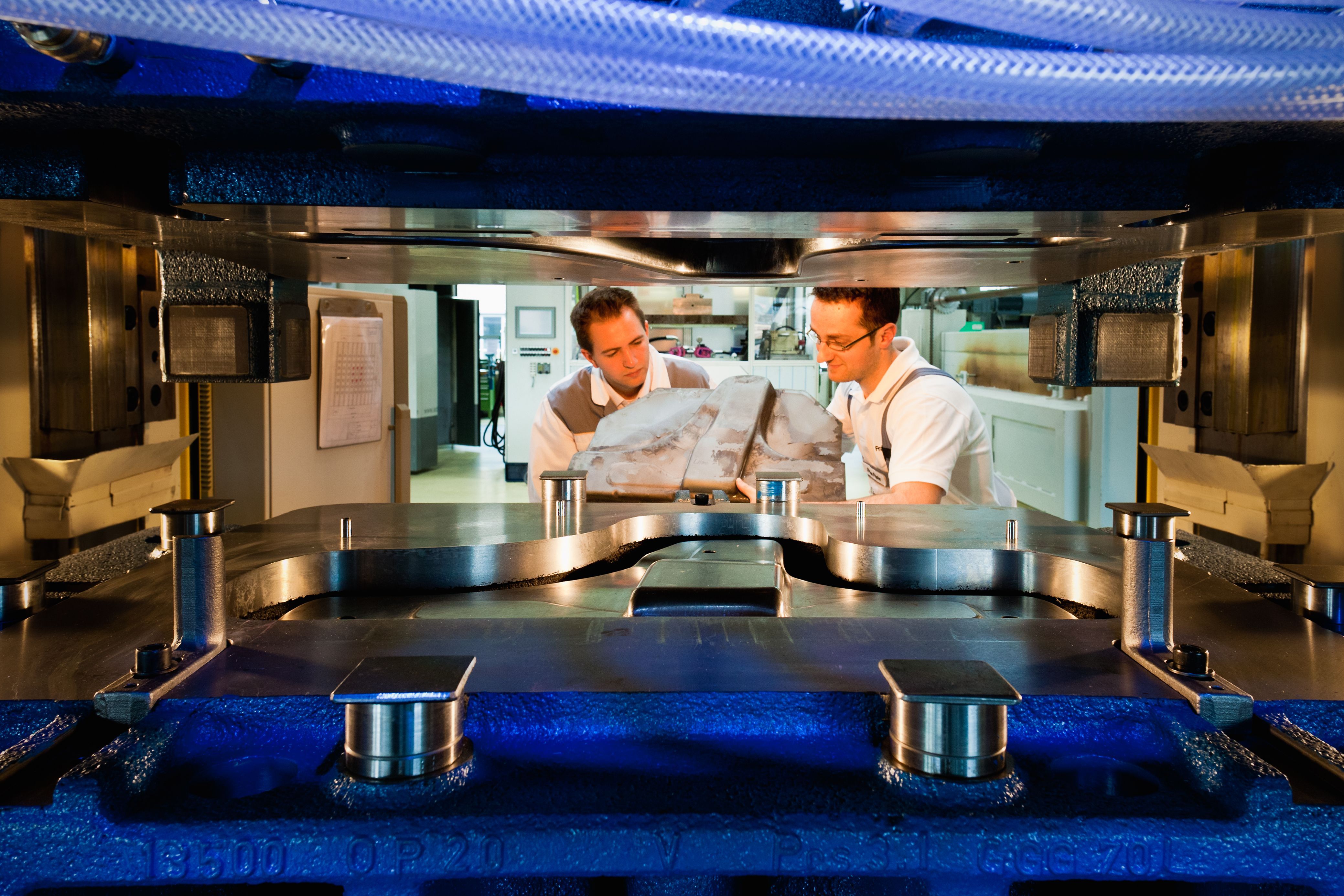
Der Spitzentechnologiecluster „Energieeffiziente Produkt- und Prozessinnovationen in der Produktionstechnik eniPROD“ der Technischen Universität Chemnitz und des Fraunhofer-Instituts für Werkzeugmaschinen und Umformtechnik IWU wurde 2009 im Rahmen der Sächsischen Exzellenzinitiative eingerichtet. Unter der Zielstellung, ganzheitliche Lösungsansätze für eine dreißigprozentige Reduzierung des Energieverbrauches in der Produktion zu erforschen, schlossen sich Wissenschaftler aus dem Maschinenbau, der Mathematik, der Informatik, der Physik sowie der Betriebs- und Geisteswissenschaften zu interdisziplinären Forschungsteams zusammen. An der Realisierung dieser Aufgaben waren bis zum Jahr 2014 über 85 Mitarbeiterinnen und Mitarbeiter unter der Leitung von Prof. Reimund Neugebauer, dem heutigen Präsidenten der Fraunhofer-Gesellschaft, beteiligt. Sie erarbeiteten in den Handlungsfeldern „Produktentwicklung“, „Produktionssysteme“, Prozessketten „Powertrain“ und „Zellstrukturen“, „Werkstoffe“ sowie „Fabrikplanung und Logistik“ wissenschaftliche Grundlagen sowie anwendungsreife Lösungen für die Industrie. Der Spitzentechnologiecluster eniPROD wurde von der Europäischen Union aus Mitteln des Europäischen Fonds für regionale Entwicklung (EFRE) sowie aus Landesmitteln des Freistaats Sachsen gefördert.
Ressourceneffiziente Prozess- und Prozesskettengestaltung für „Powertrain-Komponenten“
Im eniPROD-Handlungsfeld stand die ganzheitliche Betrachtung von Energie- und Materialflüssen bei der Herstellung von Bauteilen des Antriebsstrangs in Fahrzeugen im Mittelpunkt. Ziel war es, die Ressourcen zur Herstellung auf Prozess- und Prozesskettenebene zu analysieren und zu optimieren. Dazu mussten sowohl die Größenverhältnisse, die werkstofftechnischen Eigenschaften, die zulässigen Maßabweichungen als auch die Anforderungen an die Werkstückoberfläche berücksichtigt werden. Hier gelang eine Verkürzung der Prozesskette, indem der Schleifprozess durch drall freies Hartdrehen ersetzt wurde. Die Endbearbeitung hat einen erheblichen Einfluss auf die Energieeffizienz sowohl bei der Herstellung als auch im Betrieb. Durch den Einsatz von „Powertrain-Komponenten“ wurde eine verbesserte Funktionalität in der reibungsminimierten und verschleißbeständigen Oberflächentechnologie erzielt.
Umsetzung hochintegrativer, energiearmer „Presshärteprozessketten – Zellstrukturen“
Im Forschungsgebiet des eniPROD-Handlungsfeldes wurden neue Technologien zur Senkung des Energiebedarfs und zur Erhöhung der Energieeffizienz im Automobilbau entwickelt. Im Zentrum der Arbeiten stand die Blechwarmumformung von höchstfesten Werkstoffen, die in modernen Karosseriekonzepten eingesetzt werden. Durch diese Festigkeitssteigerung werden Wandstärken deutlich reduziert, Material und Masse gespart. Das Presshärten von höchstfesten Werkstoffen ermöglicht die Großserienfertigung von Leichtbau-Karosseriekonzepten mit maßgeschneiderten Bauteileigenschaften wie dieser „B-Säulenfuß“, durch die sich die Crashperformance entscheidend verbessern lässt. Dank einer partiell unterschiedlich starken Erwärmung und Abkühlung des Werkstoffs während des Umformprozesses lassen sich lokal unterschiedliche mechanische Bauteileigenschaften herstellen.