Forschung
Förderketten aus Kunststoff
Für den Transport von Stückgütern werden zunehmend Stetigförderer mit zum Teil raumbeweglichen Kunststoff- ketten, insbesondere Gleitketten (Scharnierband- und Multiflexketten) und Mattenketten (Modulbander), eingesetzt.
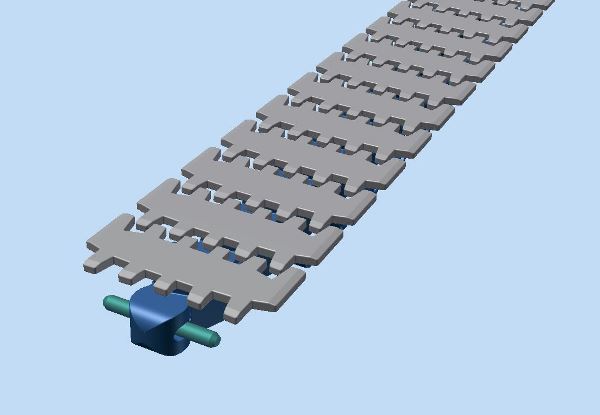
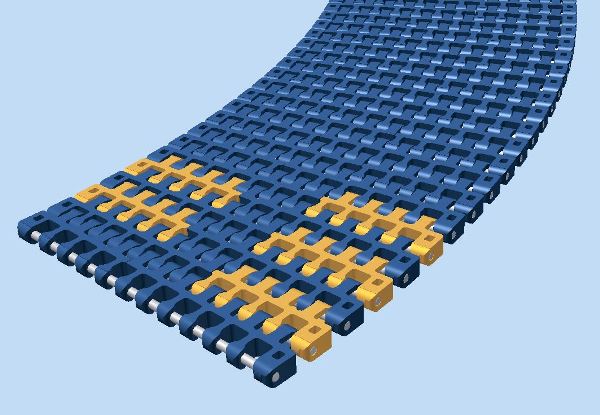
Die Kunststoffteile der Ketten lassen sich im Spritzgussverfahren in großen Stückzahlen und komplexen Geometrien effizient fertigen und zeichnen sich (gegenüber Stahl) u. a. durch geringe Dichte, gutes Gerauschdämpfungsvermögen und hohe Korrosions-/ Medienbeständigkeit aus. Kunststoffe sind vielfaltig verfügbar und lassen sich hinsichtlich der für die Ketten bzw. die Anwendungen interessanten Eigenschaften gut modifizieren. Sie besitzen zum Teil hervorragende Gleiteigenschaften, sodass derartige Fördersysteme in der Regel nicht geschmiert werden müssen, was für eine Vielzahl von industriellen Anwendungen von hoher Bedeutung ist.
Materialbedingt weisen die Kunststoffketten insbesondere hinsichtlich der zulassigen Zugkraft (Festigkeit/Dauerfestigkeit), der Steifigkeit (relativ hohe Dehnung) und der Temperaturbestandigkeit oft Defizite auf. Dadurch müssen z. B. lange Förderstrecken haufig mehrfach geteilt werden, was zusätzliche Antriebe sowie konstruktiv aufwendige und fördertechnisch nachteilige Übergabestellen erfordert.
Als Werkstoffe für Ketten, Gleitschienen und Zusatzelemente kommen thermoplastische Kunststoffe, z. B. POM, PA, PE oder PP, in für verschiedene Einsatz- und Belastungsfalle unterschiedlichen Modifikationen zum Einsatz.
Gleitketten
Gleitkettenförderer sind meist einsträngige Transportsysteme für relativ leichte Stückgüter (bis ca. 20 kg) und mittlere Geschwindigkeiten (bis ca. 1 m/s). Das Führungssystem ist meist modular aufgebaut, sodass auch sehr komplexe Förderstrecken relativ einfach aus Geraden, horizontalen und vertikalen Umlenkungen, Antriebs- und Umlenkmodulen sowie Gestell- und Führungselementen projektiert und aufgebaut werden können.
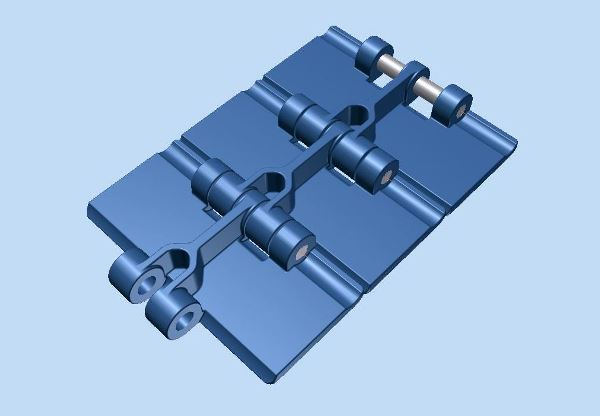
geradgängig
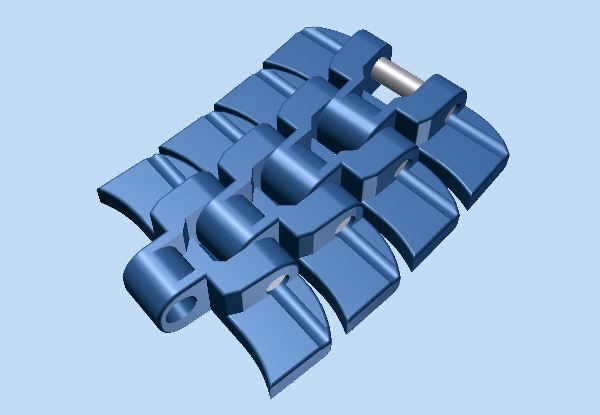
kurvengängig
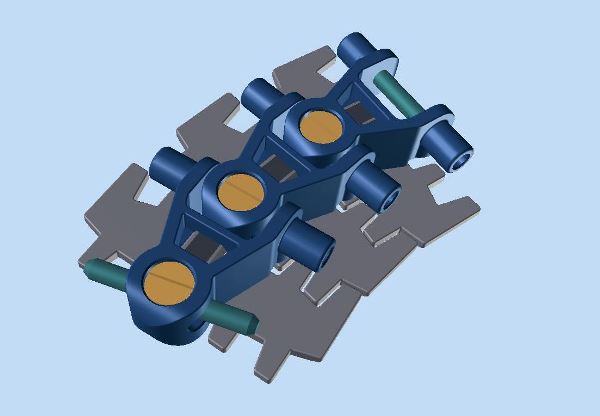
kurvengängig
Bei Gleitketten unterscheidet man grundsätzlich zwei Arten. Die einteiligen Kettenelemente der Scharnierbandketten werden mit einem Stahlbolzen gelenkig verbunden. Durch die Größe des Gelenkspiels kann dabei eine horizontale Kurvengangigkeit mit minimalem Radius von ca. 500 mm erreicht werden. Scharnierbandketten werden neben Kunststoffen auch aus Edelstahl hergestellt. Multiflexketten (auch 3D-Gleitketten) besitzen mit dem sogenannten Pin ein zusätzliches Horizontalgelenk, welches minimale Umlenkradien von ca. 150 mm sowie höhere Kettenzugkräfte ermöglicht.
Gleitkettenförderer werden sehr vielfaltig angewendet. Der schmierungsfreie Betrieb ermöglicht z. B. den Einsatz in der Lebensmittel-, Verpackungs-, Elektronik- und Pharmaindustrie, die Widerstandsfähigkeit gegen verschiedenste Chemikalien sowie die hohe Verschleißfestigkeit lasst jedoch auch Anwendungen in Verkettungseinrichtungen der spanenden Fertigung oder Montagestraßen zu.
Mattenketten
Mattenketten bestehen aus Kunststoffmodulen, die durch Stahl- oder Kunststoffstäbe gelenkig miteinander verbunden werden. Die Module lassen sich meist auch nebeneinander anordnen, sodass dadurch in Abstufungen verschiedenen Breiten bis ca. 4–5 m gefertigt werden können. Das Material und die Ausführung derartiger Ketten sind an die teilweise sehr unterschiedlichen Anforderungen der Anwender angepasst und somit außerst vielfältig. So gibt es in verschiedenen Baugrößen gerad- und kurvengängige Mattenketten mit geschlossener, halboffener oder ggf. strukturierter Oberfläche. Mattenketten sind oftmals nicht nur Zug- und Tragmittel, sondern gestatten auch die Durchführung von Verarbeitungsprozessen, z. B. Trocknen, Waschen usw., während des Transports. Die Anwendungsgebiete reichen von der Lebensmittelindustrie mit Gütern relativ geringer Masse über Papierverarbeitung, Verteilzentren, Gepäcktransport usw. bis hin zu Schwerlastanwendungen im Maschinen- und Fahrzeugbau.
Mattenketten können auf geraden Förderstrecken sehr hohe Zugkräfte übertragen. Die Hauptprobleme treten in horizontalen Kurven auf, in denen die radial gerichteten Stützkräfte zu hohen Reibungsverlusten führen. Zusätzlich werden die Kettenzugkräfte konstruktionsbedingt nur im außeren Randbereich der Kette übertragen, was die Gestaltungsmöglichkeiten solcher Anlagen sehr stark einschränkt und oftmals zu hohem Verschleiß oder gar Kettenbruch führt.
Forschungsschwerpunkte
Die Professur Fördertechnik arbeitet seit vielen Jahren sehr eng mit verschiedenen Ketten- und Systemherstellern sowie Kunststoffherstellern und -verarbeitern zusammen. Schwerpunkte sind die gemeinsame Entwicklung von neuen Kunststoff-Förderketten bzw. kompletten Förderanlagen. Das Spektrum reicht dabei von der konstruktiven Entwicklung der Ketten und des Systems, über Materialauswahl, Fertigung und mechanische bzw. tribologische Untersuchungen bis hin zur Erstellung von Dimensionierungsgrundlagen für das Gesamtsystem. Die wesentliche Zielstellung ist dabei die Effizienzsteigerung des Förderprozesses, d. h. die Leistung und Flexibilitat der Förderanlage wird erhöht und die benötigte Antriebsenergie verringert. Die Schwerpunkte der Forschung und Entwicklung auf dem Gebiet der Kunststoffketten sind:
- Verbesserung der mechanischen Eigenschaften der Ketten, insbesondere Dauerfestigkeit und Steifigkeit, durch konstruktive Gestaltung, Werkstoffe und Herstellungsverfahren
- Minimierung von Reibung und Verschleiß der relevanten Gleitpaarungen, insbesondere zwischen Kette und Führungsschiene zur Reduktion von Kettenzugkraft und Antriebsleistung (siehe auch Forschungsschwerpunkte Tribologie)
- Ersetzen der Gleitreibung durch Rollreibung (siehe auch Projekt „Rollende Fördertechnik”)
- Grundlagenuntersuchungen zum Kraft- und Bewegungsverhalten der Ketten (Kräfte im Kettenglied bzw. im System, Schwingungs- und Geräuschanalysen usw.)
- Werkstoffe und konstruktive Anforderungen für Sonderanwendungen, z. B. Lebensmittel, Chemikalien, elektrostatische Aufladung usw.
- Entwicklung von Testmethoden zur Ermittlung der Dimensionierungskennwerte
- Erstellung von Berechnungs- und Dimensionierungsgrundlagen für Ketten und Gesamtsystem
Förderketten aus Stahl
Obwohl sich Kunststoffketten zunehmend am Fördertechnikmarkt etablieren, sind diese in vielen Anwendungen (noch) keine Alternative für den Einsatz von Stahlketten. Vorrangig werden Stahlketten unter sehr rauen Last- und Umgebungsbedingungen oder bei aggressiven Fördergütern eingesetzt, bei denen Kunststoffe an ihre mechanischen oder thermischen Grenzen stoßen. Stahlketten sind jedoch auch z. B. in Trag- und Staukettenförderern anzutreffen, da sie bei geringer Baugröße relativ hohe kräfte sicher und synchron übertragen können.
Stahlketten müssen in der Regel geschmiert werden, was zum einen die Anwendungsgebiete aufgrund unschöner Verschmutzungen einschränkt und zum anderen eine regelmäßige Wartung erfordert. Ziel ist es, die Schmierwirkung durch die Verwendung spezieller Materialien und Schmierstoffe oder durch konstruktive Maßnahmen dauerhaft an den benötigten Gelenkstellen zu konzentrieren oder komplett und dadurch den Verschleiß bzw. die Wartungsintervalle positiv zu beeinflussen.
Forschungsschwerpunkte
In laufenden Forschungsvorhaben werden Schmierstoffe für Stahlgelenkketten hinsichtlich ihrer Funktionalitat und Lebensdauer untersucht und Möglichkeiten zur Überwachung (z. B. Aufforderung zu Nachschmierung bzw. Kettenwechsel) solcher Fördersysteme geschaffen. Gegenstand der Forschungen sind auch die Kontakte der Kette zum Fördergut und zu den Stütz- bzw. Führungsschienen (meist aus Kunststoff) sowie Zusatzelemente aus Kunststoff.
- Analyse und Dimensionierung von Staukettenförderern bzw. entsprechender Ketten
- überwachungssysteme für Kettenförderer
- Untersuchung von Schmierstoffen für Stahlgelenkketten
- Reibungs- und Verschleißverhalten zwischen Stahlketten und Fördergut bzw. Kunststoff-Führungsschienen
- Untersuchung von Stahlketten mit Kunststoffelementen
- Dimensionierung von Kettenfördersystemen
- Bruch- und Dauerfestigkeitsuntersuchungen
Transportzahnriemen
In der Fördertechnik werden Zahnriemen für Transportaufgaben (Gut liegt direkt auf dem als Zug- und Tragmittel fungierenden Zahnriemen auf) sowie indirekt in Linearantrieben (z. B. Hubvorrichtung für Regalbediengeräte) verwendet. Gegenüber antriebstechnischen Zahnriemen sind die Geschwindigkeiten relativ gering und die Profilgeometrie und Breite der Riemen meist größer.
Der Hauptvorteil ist der formschlüssige Antrieb, der (im Gegensatz zu Flachriemen) eine schlupffreie übertragung des Drehmomentes und damit z. B. eine synchrone Bewegung mehrerer parallel laufender Bahnen ermöglicht – sie werden deshalb auch als Synchronriemen bezeichnet. Fördertechnische Zahnriemen werden meist aus thermoplastischem Polyurethan gefertigt, so können sie z. B. kontinuierlich gefertigt und in beliebiger Lange verbunden werden. Weiterhin ist dadurch die relativ einfache Veredlung möglich, z. B. das Anbringung von Zusatzelementen (Mitnehmer, Befestigungselemente) und funktionellen Rückenbeschichtungen (Anpassung an das Fördergut) sowie spezielle Bearbeitungen des Zahnriemens. Zahnseitig werden diese Riemen oft mit einem speziellen Gewebe beschichtet, um die Reibung zu den Stützschienen sowie im Bereich der Zahnscheiben zu reduzieren.
Forschungsschwerpunkte
Schwerpunkt der Forschung auf diesem Gebiet ist die Senkung des Bewegungswiderstandes zwischen Zahnriemen und Stützschiene, die häufig zu hoher Antriebsleistung sowie temperaturbedingten Verschleißerscheinungen führt. Weiterhin werden u. a. Lösungen zur Funktionalisierung von Zahnriemen, z. B. die Integration von Leitungsträgern zur Energie- und Datenübertragung, Verbindungstechnologien sowie fördertechnische Anwendungen jeder Art untersucht und Dimensionierungsgrundlagen für Zahnriemenförderer erstellt.
- Reibungs- und Verschleißverhalten von Zahnriemen und Führungsschienen
- Integration von Leitungsträgern und berührungslose Energie- und Datenübertragung
- Untersuchung von Transportzahnriemen und Fördersystemen
- Analyse von Zahnriemenverbindungen
- Dimensionierung von Zahnriemenförderern
Download Handzettel (deutsch)
Vorspannung von Antriebszahnriemen
Antriebszahnriemen finden sich in meist schnell laufenden Getrieben und dienen der Drehzahl- und Drehmomentübertragung, wobei dies aufgrund des schlupffreien Betriebes mit hoher Leistung und äußerst prazise erfolgen kann.
Zahnriemen müssen immer vorgespannt werden, wobei die Größe der Vorspannkraft entscheidenden Einfluss auf die Funktion und Lebensdauer des gesamten Getriebes hat. Eine zu geringe Vorspannung kann zu starken Trumschwingungen oder zum überspringen der Zahne an den Zahnscheiben führen, zu hohe Kräfte verursachen dagegen eine starke Belastung der Lager und des Riemens und beeinflussen damit den Verschleiß und die Lebensdauer der Getriebekomponenten negativ.
Die gangigen Methoden zur Aufbringung der Vorspannkraft nutzen einerseits die Elastizität des Zahnriemens und des Getriebes durch Veranderung des Achsabstandes der Zahnscheiben oder eine zusätzliche, gestellfeste Spannrolle. Weiterhin werden komplexe Spannsysteme angewendet, die die Spannkraft mittels Federn aufbringen und oft zusätzliche Dämpfungselemente enthalten.
Eine dritte, zusammen mit einem Industriepartner an der Professur Fördertechnik entwickelte Methode nutzt ein elastisches, ringförmiges Spann- und Dämpfungselement, welches platzsparend zwischen den Riementrumen eingesetzt wird. Durch die spezielle Spanncharakteristik dieses Elementes wird das Getriebe im Stillstand nahezu vollstandig entlastet, im Betriebszustand passt sich die Vorspannkraft automatisch an das wirkende Drehmoment an. Das Spannelement funktioniert drehrichtungsunabhängig, gleicht Achsabstands- oder Rundlauffehler aus und dampft wirkungsvoll Drehmomentstöße und Trumschwingungen.
Einstellung des Achsabstandes
Spann- und Dampfungselement
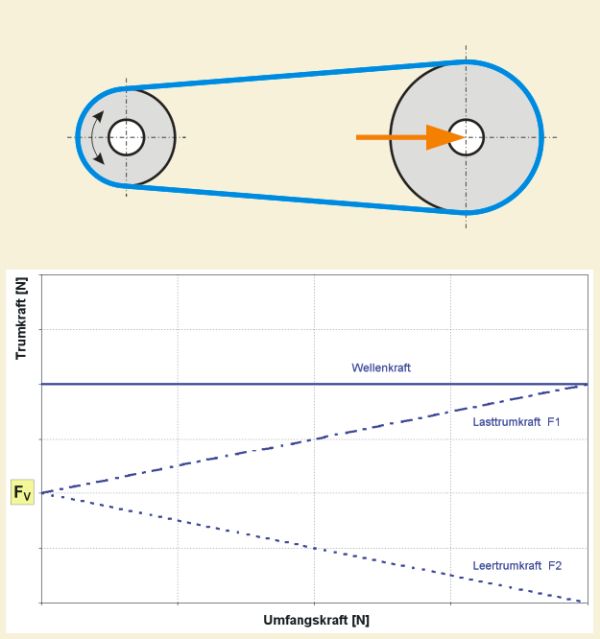
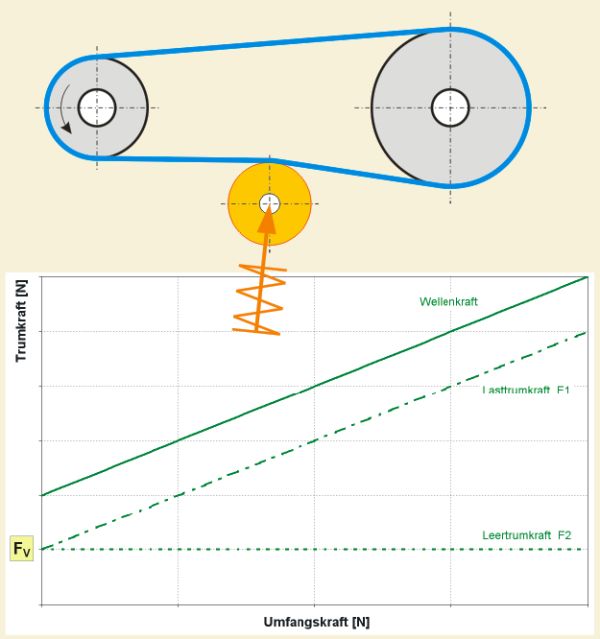
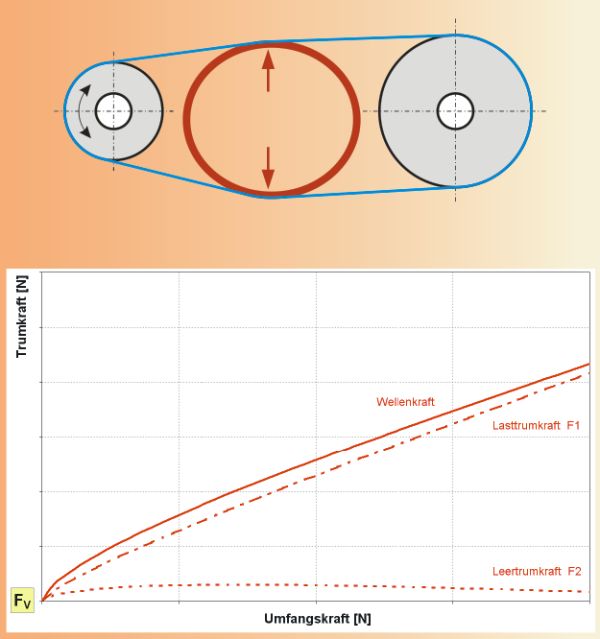
- keine Zusatzelemente nötig
- Reversierfahigkeit
- sehr empfindlich gegenüber Maßtoleranzen (exakte Krafteinstellung schwierig)
- Gefahr von Funktionsstörungen oder Überspannung
- hohe Vorspannung im Ruhezustand notwendig
- keine Schwingungsdämpfung
- relativ geringe Vorspannkraft
- Integration von Schwingungsdampfern möglich
- komplexes Zusatzbauteil
- externe Montagebasis erforderlich (Platzbedarf)
- nicht reversierfähig
- einfache, platzsparende Montage
- nahezu komplette Getriebeentlastung im Einbauzustand
- automatische Spannkraftanpassung an die Last
- Reversierfähigkeit
- effiziente Dämpfung von Trum- und Drehschwingungen
- geringe Drehwinkeldifferenz zwischen An- und Abtrieb
Forschungsschwerpunkte
Die Professur Fördertechnik beschaftigt sich seit vielen Jahren mit der Untersuchung alternativer Spannmethoden für Zahnriemengetriebe. Mit der Entwicklung des ringförmigen Spann- und Dämpfungselementes entstand eine völlig neuartige, getriebeschonende Spanncharakteristik. Die aktuellen Aufgaben dazu bestehen in der Ableitung weiterer Anwendungsfelder sowie der Erarbeitung von dynamischen Berechnungsmodellen. Weitere Forschungsschwerpunkte sind u.a. Untersuchungen zum Übersprungverhalten sowie Schwingungs- und Geräuschanalysen.
- Spannsysteme für Zahnriemengetriebe, insbesondere ringförmiges Spann- und Dämpfungselement Roll-Ring® (Fa. Ebert Kettenspanntechnik GmbH, Schkeuditz)
- übersprungverhalten von Zahnriemen
- Alternative Seitenführung von Zahnriemen
- Schwingungs- und Geräuschanalysen
- Analyse und Dimensionierung von Zahnriemengetrieben, Wirkungsgradmessungen
Tribologie in der Fördertechnik
Tribologie ist die Wissenschaft von Reibung, Verschleiß und Schmierung. An den meisten tribologischen Systemen der Fördertechnik sich Kunststoffe beteiligt. Neben den Vorteilen wie geringe Dichte, sehr gute Verarbeitbarkeit, Geräuschdämpfungsvermögen usw. besitzen viele Kunststoffe hervorragende Gleiteigenschaften, sodass die Systeme normalerweise nicht geschmiert werden müssen. Dies ermöglicht viele Anwendungsgebiete auch in solch sensiblen Bereichen wie z. B. Lebensmittel-, Pharma- oder Elektronikindustrie, in denen eine Schmierung unerwünscht ist.
Wichtige Gleitpaarungen in Stetigförderern sind z. B.
- Zugmittel – Gleitschiene (meist aus Kunststoff)
- Zugmittel – Fördergut (Metall, Kunststoff, Glas, Pappe, …)
Zugmittel können Stahl-/ Kunststoffketten, Zahnriemen, Bänder usw. sein.
In einigen fördertechnischen Anwendungen, z. B. wenn Güter auf ansteigenden Strecken transportiert werden sollen, werden hohe Reibwerte gefordert. Wie auch in anderen technischen Systemen ist jedoch die Reibung in Stetigförderern meist unerwünscht, da sie in direkter Folge zu Erwärmung und Verschleiß an Zugmitteln und/oder Führungselementen, starker Zugmittelbelastung sowie hoher Antriebsleistung fährt. Reibung verursacht demnach teilweise erhebliche Kosten durch Antriebsenergie, turnusmäßige Wechselintervalle von Zugmitteln und Komponenten oder gar unplanmäßige Stillstandzeiten beim Versagen des Fördersystems.
Einer Studie der Gesellschaft für Tribologie (www.gft-ev.de) zur Folge entstehen durch Reibung und Verschleiß allein in Deutschland jährliche Verluste in Höhe von ca. 35 Milliarden Euro. Durch Umsetzen des bereits vorhandenen tribologischen Wissens könnten davon 5 Milliarden EUR/Jahr eingespart werden. Durch weitere tribologische Forschung kann dieses Sparpotential noch gesteigert werden.
Unsere Forschungsgruppe stellt sich der Herausforderung, diesem Ziel ein Stück näher zu kommen.
Ursachen von Reibung und Verschleiß
Die Reibung basiert nach heutigem Kenntnisstand auf zwei wesentlichen Ursachen
- der Deformation (Verformung von Rauheitsspitzen, Furchung, …) und
- der Adhäsion (atomare und molekulare Wechselwirkungen im Bereich der realen Kontaktfläche)
Beide Phänomene treten immer gleichzeitig, jedoch in Abhängigkeit von den Material- und Oberflächeneigenschaften in unterschiedlichen Verhältnissen auf. Insbesondere bei trocken laufenden Reibpaarungen mit Kunststoffbeteiligung sind die Reibwerte deshalb sehr stark von den Belastungs- und Umgebungsbedingungen, z. B. Flächenpressung (Gutmasse), Geschwindigkeit, Umgebungs- und Kontaktflächentemperatur usw. abhängig und ändern sich häufig auch während der Betriebsdauer. In der Praxis fährt dies nach einiger Zeit trotz vermeintlich gleicher Randbedingungen oft zu steigenden Systemreibwerten, die sich durch plötzlich auftretenden Leistungsmangel der Antriebe, starke Erwärmung oder überhöhten Verschleiß und schlimmstenfalls durch den Ausfall des Fördersystems äußern.
Forschungsansätze zur Reibungs- und Verschleißsenkung
Bei Kenntnis der Reibungsursachen und der Wirkungen der äußeren Einflüsse auf das tribologische System können Reibung und Verschleiß gezielt beeinflusst werden. Dabei ist zu berücksichtigen, dass der Reibwert ein Systemparameter und keine Materialeigenschaft ist. So kann ein vermeintlich gleitfreudiges Material in Kombination mit einem anderen Werkstoff durchaus ungünstige Werte aufweisen. Außerdem bedeutet ein niedriger Reibwert nicht gleichzeitig einen geringen Verschleiß.
Die Untersuchung des tribologischen Verhaltens konzentriert sich schwerpunktmäßig auf schmierungsfreie Paarungen mit Kunststoffbeteiligung und Bezug zur Fördertechnik. Reibung und Verschleiß werden in Abhängigkeit der Belastungs- und Umgebungsbedingungen (u. a. in einer Klimakammer) untersucht und die Ergebnisse in einer Tribo-Datenbank erfasst. Zur Reibungs- und Verschleißsenkung werden folgende Hauptansätze verfolgt:
- Untersuchung und Modifikation von Polymerwerkstoffen
- Untersuchung und gezielte Beeinflussung von Oberflächenstrukturen
- Beschichtung von Kunststoffoberflächen
- Untersuchung und Modifikation von textilen Gleitflächen
- Konstruktive Maßnahmen zur Reibwertsenkung – z. B. Ablösung von Gleitreibung durch Rollreibung
Für die Untersuchungen stehen spezielle Prüfstände aus eigener Entwicklung zur Verfügung, die eine möglichst realitätsnahe Belastung der Proben sowie die Erfassung und Analyse der Messwerte auch über sehr lange Zeiträume gestatten.